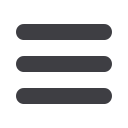
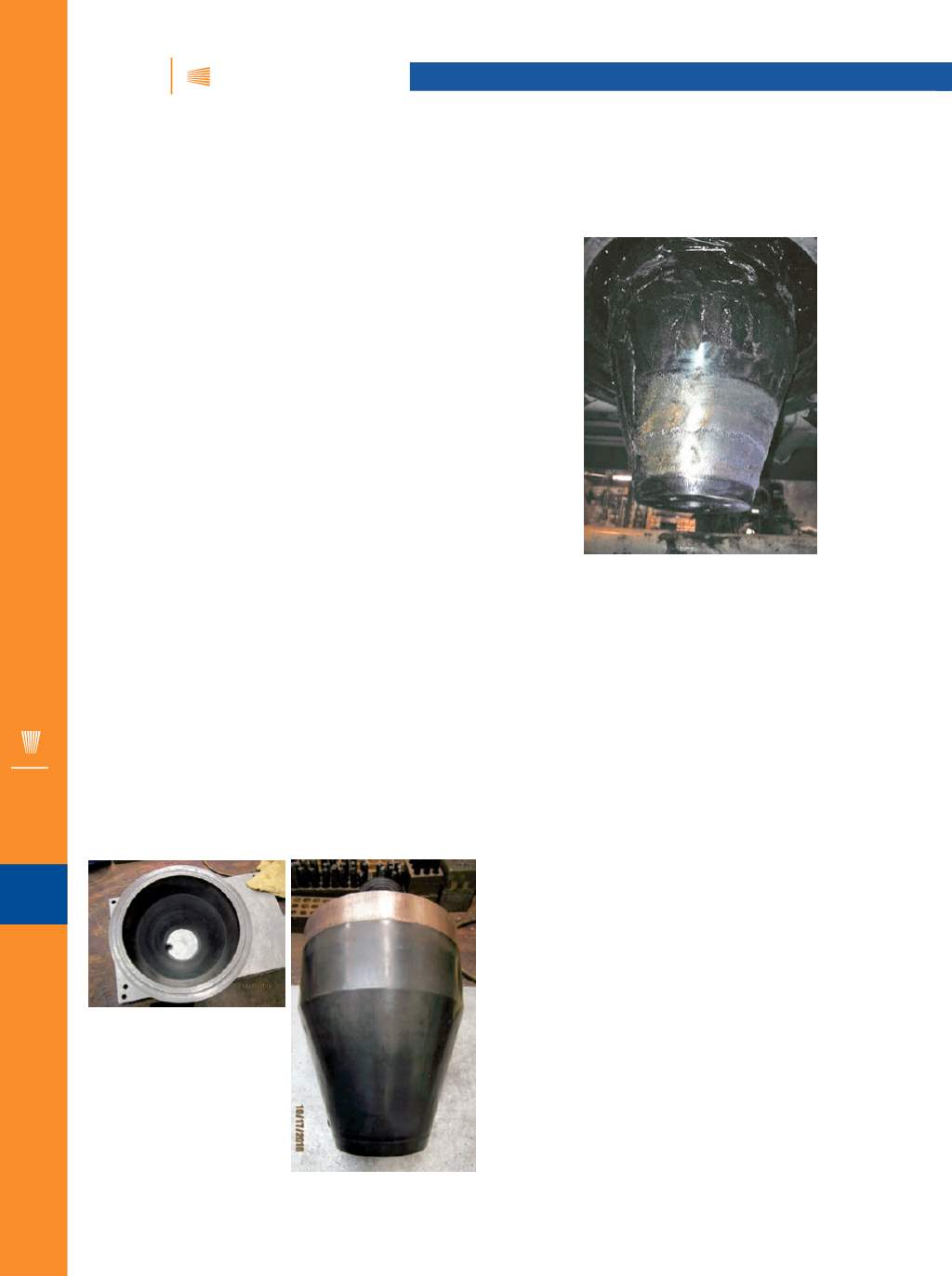
iTSSe
TSS
A D V A N C E D M A T E R I A L S & P R O C E S S E S | M A Y / J U N E 2 0 1 7
4 4
iTSSe
TSS
CASE STUDY
10
REASON TO CONSIDER SURFACING
Finished surface quality is of paramount importance to
parts that are mass-produced using blowmolding and
plastic injectionmolding technologies. Wear that causes dimensional
changes in tooling (and final parts) can be greatly reduced by
applying a wear-resistant carbide, stainless steel, or ceramic
surface to tooling components via thermal spray.
Carbide ther- mal spraysurfacing is an established additive surfacing tech-
nique used in many plastic material processing applications.
New parts processed with a wear-resistant thermal spray
coating give tooling components remarkably greater service
life. During routine maintenance, worn parts often can be re-
surfaced back to OEM specifications, significantly reducing
replacement costs.
ASB Industries works with OEMs and rebuilders to pro-
tect and maintain quality tooling components to meet equip-
ment design specifications. ASB recently worked with a local
manufacturer of blowmolded and injectionmolded products.
This application is discussed here.
ISSUES
Blowmold head tooling wear was being caused by glass-
filled nylonmaterial. This tooling wear was creating die gap is-
sues, disrupting material flow during production, and causing
nonconforming parts to be manufactured.
OPTION
ASB Industries applied a commercially available tung-
sten carbide coating on the head tooling using the high
velocity oxy-fuel (HVOF) process. A coating thickness of 0.010
in. per side is applied to the die component ID and to the pin
component OD. Each component requires diamond finish
grinding to achieve the final dimensions and a surface finish
of 32 Ra micro-in.
BENEFITS
Tooling that was not coatedwith tungsten carbide began
to showwear and create die gap issues after only eightmonths
of runtime, but continued to be used in production. Worn tool-
ing was eventually replaced with newly coated components.
Tooling service life went from just eight months to more
than 23 months so far; the customer is experiencing less
downtime and labor to remove worn components.
As of this writing, the manufacturer has plans to install a
new set of nitride components due to less cost compared to
the HVOF carbide coating. Some of the engineers and mainte-
nance personnel believe a quick repair is easier than the two
or three weeks of turnaround time for coating removal, car-
bide coating, and diamond grinding. The other engineers and
maintenance personnel believe the HVOF carbide coating is a
better value. This will be an ongoing case study.
~iTSSe
For more information:
Scott Whitten is an application
specialist at ASB Industries Inc., 1031 Lambert St., Bar-
berton, OH 44203, 330.753.8458,
scott@asbindustries.com,
www.asbindustries.com.
CARBIDE THERMAL SPRAY SURFACING
PROTECTS BLOW MOLD HEAD TOOLING
Fig. 1
– Blowmold head tooling (die and pin) coated with a tung-
sten carbide/cobalt matrix aer 19 months in service.
Fig. 2
– Non-coated blowmold head tooling (pin) aer 17 months
in service.