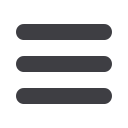
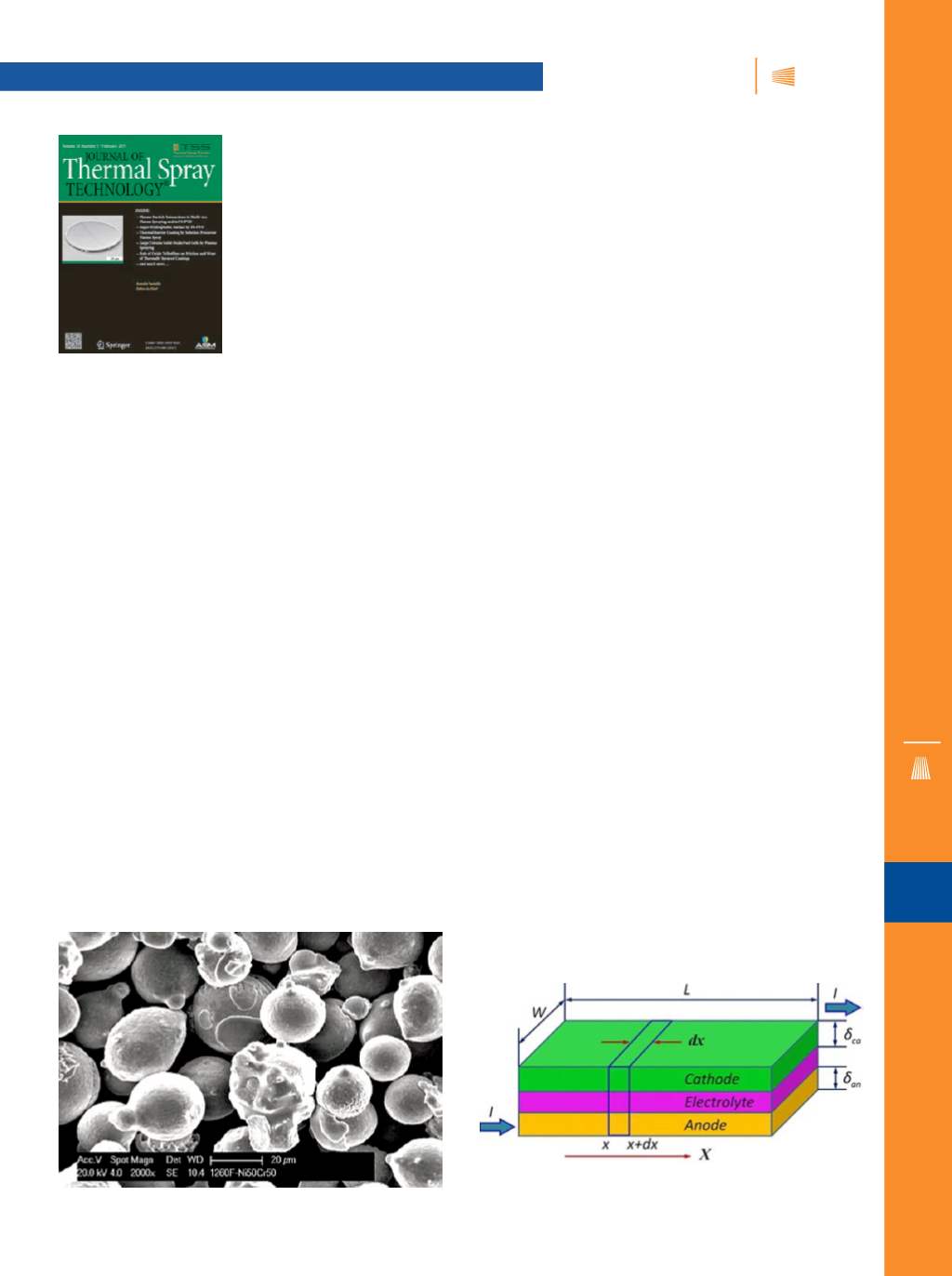
iTSSe
TSS
A D V A N C E D
M A T E R I A L S
&
P R O C E S S E S |
M A Y / J U N E
2 0 1 7
4 5
T
|
iTSSe
TSS
JTST
HIGHLIGHTS
11
The
Journal of Thermal Spray
Technology (JTST),
the official
journal of the ASMThermal Spray
Society, publishes contributions
on all aspects—fundamental and
practical—of thermal spray sci-
ence, including processes, feed-
stock manufacture, testing, and
characterization. As the primary
vehicle for thermal spray infor-
mation transfer, its mission is to
synergize the rapidly advancing
thermal spray industry and related industries by presenting
research and development efforts leading to advancements
in implementable engineering applications of the technolo-
gy. Articles from the February and April issues, as selected by
JTST
Editor-in-Chief Armelle Vardelle, are highlighted here.
The April issue contains a special focus on “Metal Additive
Manufacturing,” organized by guest editors Bertrand Jodoin,
Mathieu Brochu, Jean-Yves Hascoet, and Todd Palmer. The
third, fourth, and fifth articles highlighted here are from this
special focus. In addition to the print publication,
JTST
is avail-
able online through springerlink.com. For more information,
visit asminternational.org/tss.
ROLE OF OXIDES AND POROSITY ON HIGH-
TEMPERATURE OXIDATION OF LIQUID-FUELED
HVOF THERMAL-SPRAYED NI50CR COATINGS
B. Song, M. Bai, K.T. Voisey, and T. Hussain
Highchromiumcontent inNi50Cr thermally sprayedcoat-
ings can generate a dense and protective scale at the coating
surface. Thus, the Ni50Cr coating is widely used in high-tem-
perature oxidation and corrosion applications. A commercial-
ly available, gas atomized Ni50Cr powder was sprayed onto
a power plant steel (ASME P92) using a liquid-fueled HVOF
thermal spray with three processing parameters in this study.
The microstructure of as-sprayed coatings was examined
using oxygen content analysis, mercury intrusion porosimetry,
scanning electron microscopy (SEM), energy-dispersive x-ray
spectroscopy (EDX), and x-ray diffraction (XRD). Short-term air
oxidation tests (4 h) of freestanding coatings (without boiler
steel substrate) in a thermogravimetric analyzer at 700°C were
performed to obtain the kinetics of oxidation of the as-sprayed
coating. Long-term air oxidation tests (100 h) of the coated
substrates were performed at the same temperature to obtain
the oxidation products for further characterization in detail
using SEM/EDX and XRD. In all samples, oxides of various mor-
phologies developed on top of the Ni50Cr coatings. Cr
2
O
3
was
themain oxidation product on the surface of all three coatings.
The coating with medium porosity and medium oxygen con-
tent had the best high-temperature oxidation performance in
this study (Fig. 1).
THERMALLY SPRAYED LARGE TUBULAR
SOLID OXIDE FUEL CELLS AND ITS STACK:
GEOMETRY OPTIMIZATION, PREPARATION,
AND PERFORMANCE
Shan-Lin Zhang, Cheng-Xin Li, Shuai Liu, Chang-Jiu Li,
Guan-Jun Yang, Peng-Jiang He, Liang-Liang Yun, Bo Song,
and Ying-Xin Xie
In this study, a large tubular solid oxide fuel cell (SOFC)
design was developed with several cells in series on a porous
cermet support with characteristics such as self-sealing, low
ohmic loss, high strength, and good thermal expansion co-
efficient matching. Aspects of the cell design, manufacture,
performance, and application are investigated. First, the cell
length and number of cells in series are optimized by theoret-
ical analysis. Thermal spray is then applied as a cost-effective
method to prepare cell components. Finally, performance of
different types of cells and two types of stacks is character-
ized. The maximum output power of one tube, which has 20
cells in series, reaches 31 W and 40.5 W at 800°C and 900°C,
respectively. Moreover, the output power of a stack assembled
with 56 tubes, each with 10 in series, reaches 800 W at 830°C.
Excellent single tube and cell stack performance suggests that
thermally sprayed tubular SOFCs have significant potential for
commercial applications (Fig. 2).
Fig. 1
− SEM image of as-received powder particle morphology.
Fig. 2
− Schematic of the current flow inside a single cell in SS-SOFC
design.