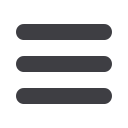
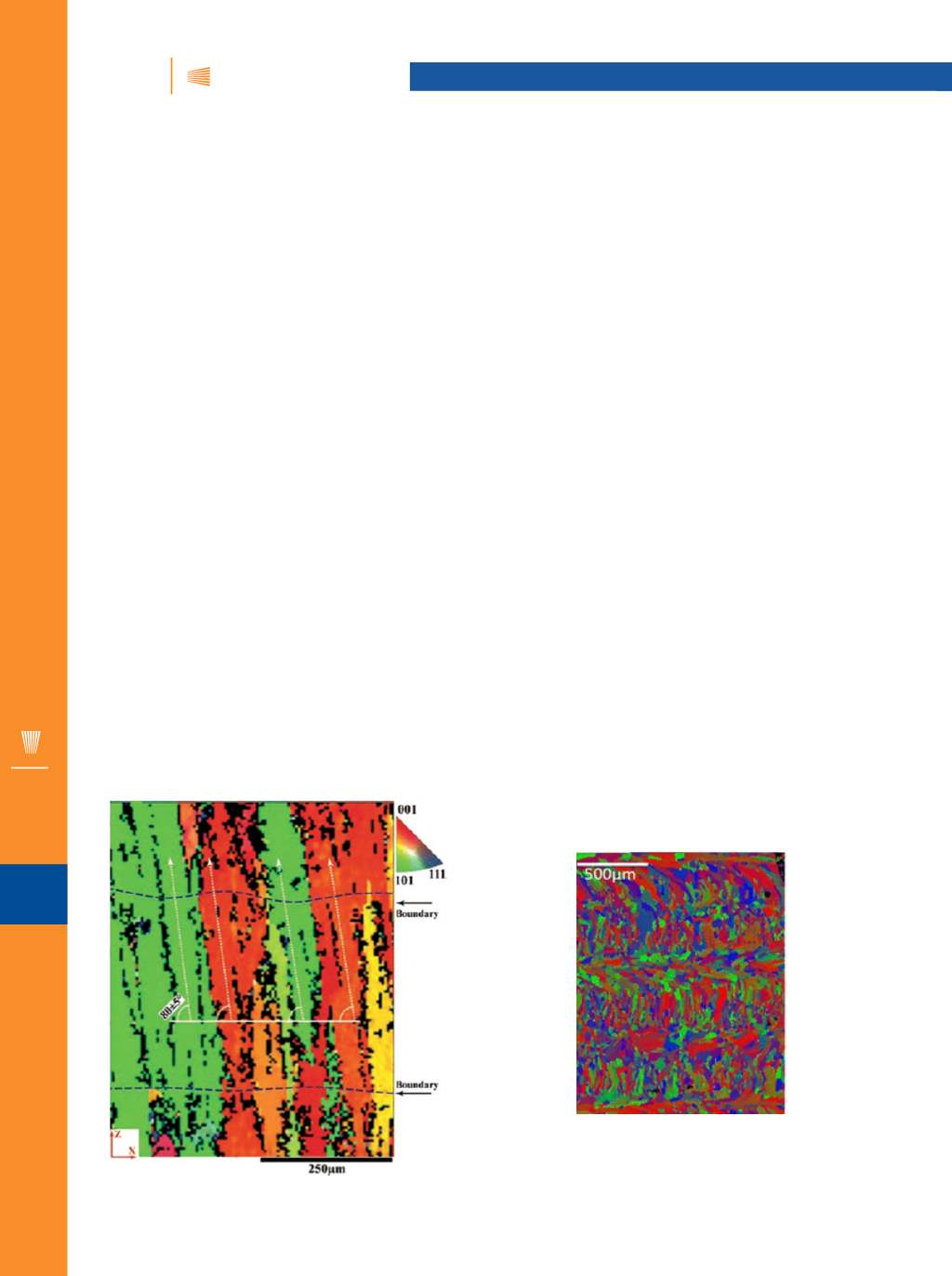
iTSSe
TSS
A D V A N C E D M A T E R I A L S & P R O C E S S E S | M A Y / J U N E 2 0 1 7
4 6
iTSSe
TSS
JTST
HIGHLIGHTS
12
ADDITIVE MANUFACTURING OF ALSI
10
MG
ALLOY USING DIRECT ENERGY DEPOSITION:
MICROSTRUCTURE AND HARDNESS
CHARACTERIZATION
M. Javidani, J. Arreguin-Zavala, J. Danovitch, Y. Tian, and
M. Brochu
This paper aims to study AlSi
10
Mg alloy manufacturing
with the direct energy deposition (DED) process. Following
fabrication, the macro- and microstructural evolution of the
as-processed specimens were initially investigated using
optical microscopy and scanning electron microscopy. A co-
lumnar dendritic structure was the dominant solidification
feature of the deposit; nevertheless, detailed microstructural
analysis revealed cellular morphology near the substrate and
equiaxed dendrites at the top end of the deposit. Moreover,
the microstructural morphology in the melt pool boundary of
the deposit differed from the one in the core of the layers. The
remaining porosity of the deposit was evaluated by Archime-
des’ principle and by image analysis of the polished surface.
Crystallographic texture in the deposit was also assessed us-
ing electron backscatter diffraction (EBSD) and x-ray diffrac-
tion analysis. The dendrites were unidirectionally oriented at
an angle of ~80° to the substrate. EPMA line scans were per-
formed to evaluate the compositional variation and elemental
segregation in different locations. Eventually, microhardness
(HV) tests were conducted in order to study the hardness gra-
dient in the as-DED-processed specimen along the deposition
direction. The results, which exhibit a deposit with an almost
defect-free structure, indicate that the DED process is suitable
for the deposition of Al-Si-base alloys with a highly consolidat-
ed structure (Fig. 3).
PROCESS-STRUCTURE-PROPERTY
RELATIONSHIPS FOR 316L STAINLESS STEEL
FABRICATED BY ADDITIVE MANUFACTURING
AND ITS IMPLICATION FOR COMPONENT
ENGINEERING
N. Yang, J. Yee, B. Zheng, K. Gaiser, T. Reynolds, L. Clemon,
W.Y. Lu, J.M. Schoenung, and E.J. Lavernia
This study investigates the process-structure-property
relationships for 316L stainless steel prototyping utilizing 3D
laser engineered net shaping (LENS), a commercial direct en-
ergy deposition additive manufacturing process. The study
concludes that the resultant physical metallurgy of 3D LENS
316L prototypes is dictated by interactive metallurgical reac-
tions during instantaneous powder feeding/melting, molten
metal flow, and liquid metal solidification. The study also
shows that 3D LENSmanufacturing is capable of building high
strength and ductile 316L prototypes due to its fine cellular
spacing from fast solidification cooling, and well-fused epi-
taxial interfaces at metal flow trails and interpass boundaries.
However, without further LENS process control and optimiza-
tion, deposits are vulnerable to localized hardness variation
attributed to heterogeneous microstructure, i.e., the inter-
pass heat-affected zone (HAZ) from repetitive thermal heating
during successive layer depositions. Most significantly, current
deposits exhibit anisotropic tensile behavior, i.e., lower strain
and/or premature interpass delamination parallel to build di-
rection (axial). This anisotropic behavior is attributed to the
presence of interpass HAZ, which coexists with flying feed-
stock inclusions and porosity from incomplete molten metal
fusion. The current observations and findings contribute to
the scientific basis for future process control and optimization
necessary for material property control and defect mitigation
(Fig. 4).
Fig. 3
− EBSDmapping at middle (half height) of specimen; inverse
pole figure (IPF) colored orientation image map, with IPF.
Fig. 4
− Morphology, size, and crystal orientation for the solidifica-
tion cells: EBSD orientation map.