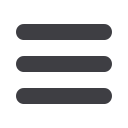
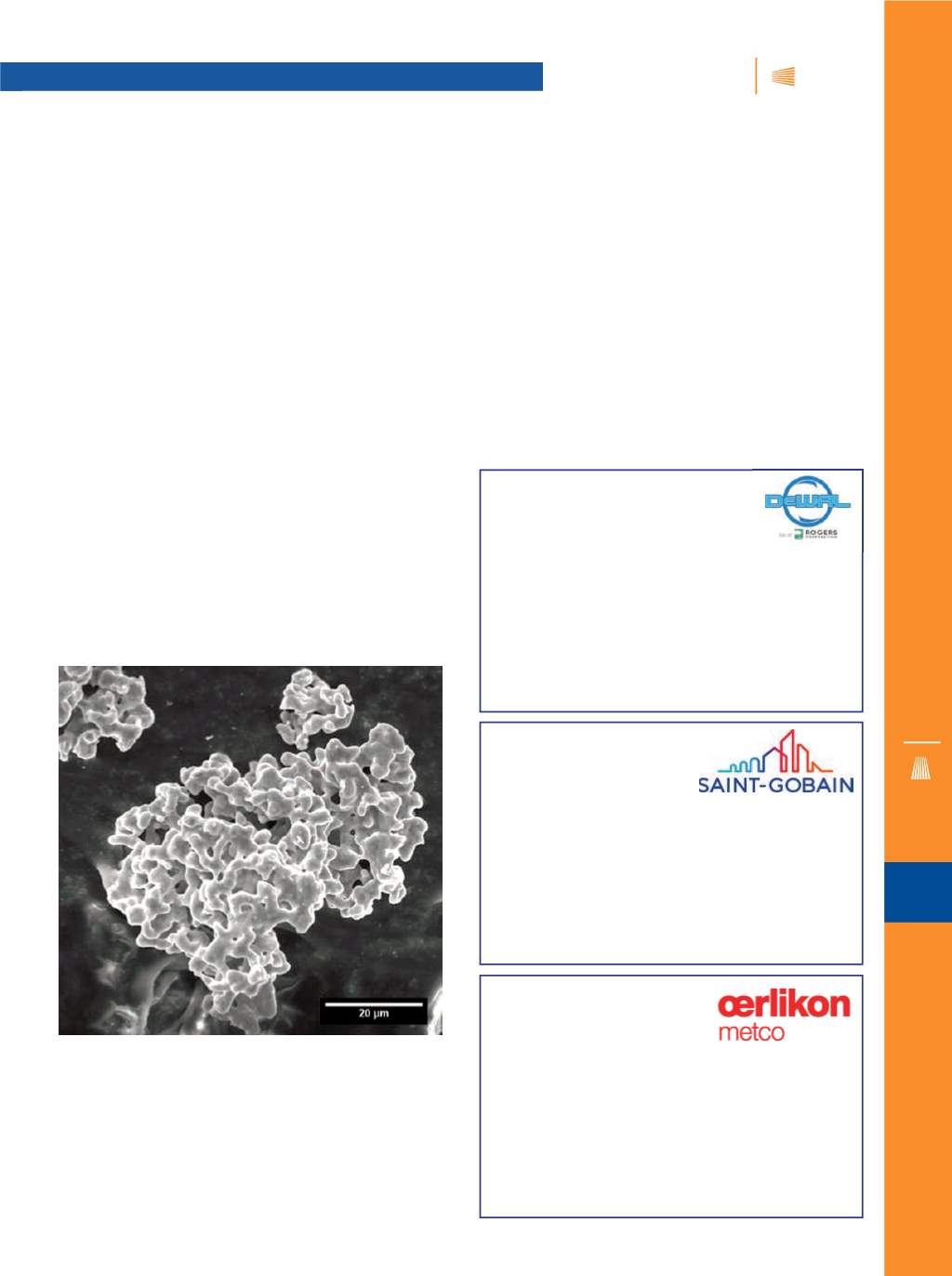
iTSSe
TSS
A D V A N C E D
M A T E R I A L S
&
P R O C E S S E S |
M A Y / J U N E
2 0 1 7
4 7
T
I
|
iTSSe
TSS
JTST
HIGHLIGHTS
13
COLD SPRAYING OF ARMSTRONG PROCESS
TITANIUM POWDER FOR ADDITIVE
MANUFACTURING
D. MacDonald, R. Fernández, F. Delloro, and B. Jodoin
Titanium parts are ideally suited for aerospace applica-
tions due to their unique combination of high specific strength
andexcellent corrosion resistance. However, titaniumbulkma-
terial is expensive and challenging to machine. Production of
complex titanium parts through additive manufacturing looks
promising, but there are still many barriers to overcome before
reachingmainstreamcommercialization. The cold gas dynam-
ic spraying process has potential for additivemanufacturing of
large titanium parts due to its reduced reactive environment,
simple operation, and high deposition rates. However, a few
challenges must first be addressed. In particular, it is known
that titanium is easy to deposit by cold gas dynamic spraying,
but the deposits are usually porous when nitrogen is used as
the carrier gas. In this work, a method tomanufacture low-po-
rosity titanium components at high deposition efficiencies is
revealed. Components are produced by combining low-pres-
sure cold spray using nitrogen as the carrier gas with low-cost
titanium powder produced using the Armstrong process. The
microstructure andmechanical properties of additivelymanu-
factured titanium components are investigated (Fig. 5).
Fig. 5
− SEM image of coral-shaped titaniumpowder produced
using the Armstrong process.
2017 ITSC EXHIBITOR
SHOWCASE
VISIT THESE KEY EXHIBITORS AND
MORE AT ITSC 2017
EXHIBITIONHOURS
CCD Congress Center Düsseldorf, Stadthalle
Wednesday, June 7 • noon to 6:00 p.m.
Thursday, June 8 • 9:00 a.m. to 6:00 p.m.
Friday, June 9 • 9:00 a.m. to 4:00 p.m.
DeWAL manufactures the world’s most
complete line of thermal spray tapes.
After years developing and improving these preci-
sion plasma tapes, DeWAL manufactures them in Rhode
Island for aircraft engine, automotive and medical manufacturers. DeWAL tapes
are used by all three major aircraft engine manufacturers—GE, Pratt & Whitney,
and Rolls-Royce.
DeWAL tapes are free of carbonizingmaterials for grit blast, ceramic, plas-
ma, arc, and HVOF spraying. Whatever temperature or spray angle, they adhere
aggressively, ensuring sharp edges, then separate cleanly.
Single and double-ply tapes, all manufactured with proprietary silicone
adhesive technology, are available worldwide.
www.dewal.comBooth D14
DEWAL THERMAL SPRAY TAPES
DeWAL is part of Rogers Corp
Saint-Gobain is a world class manufacturer
of equipment and consumables for the
thermal spray coatings industry. Our expansive equipment experience dates
back to 1920 with the development of the first oxy-acteylene flame wire gun
followed by Rokide® Spray Systems, Plasma Spray Systems, PTA andmany in-
novative materials. We offer a wide range of consumables in the form of powder,
flexible cords, Rokide® rods, and ingots for use in many different applications
and industries. We supply our own rawmaterials and this enables us to develop
a product to meet your exact needs.
www.coatingsolutions.saint-gobain.com.
Booth D3
SAINT-GOBAIN
COATING SOLUTIONS
Oerlikon Metco enhances surfaces that bring
benefits to customers through a uniquely broad
range of surface technologies, equipment,
materials, services, specializedmachining
services and components. The surface technologies such as Thermal Spray and
Laser Cladding improve the performance and increase efficiency and reliability.
As an innovation leader, Oerlikon Metco is forging new paths with materials for
additive manufacturing, brazing, conductive fillers, powder injectionmolding,
plasma transferred arc weld hardfacing and other industrial processes.
Oerlikon Metco serves industries such as aviation, power generation, automo-
tive, oil & gas, industrial and other specializedmarkets and operates a dynami-
cally growing network of more than 40 sites in EMEA, Americas and Asia Pacific.
Oerlikon Metco, together with Oerlikon Balzers, belongs to the Surface Solutions
Segment of the Switzerland-based Oerlikon Group.
Booth B4
OERLIKONMETCO