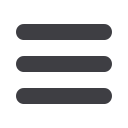
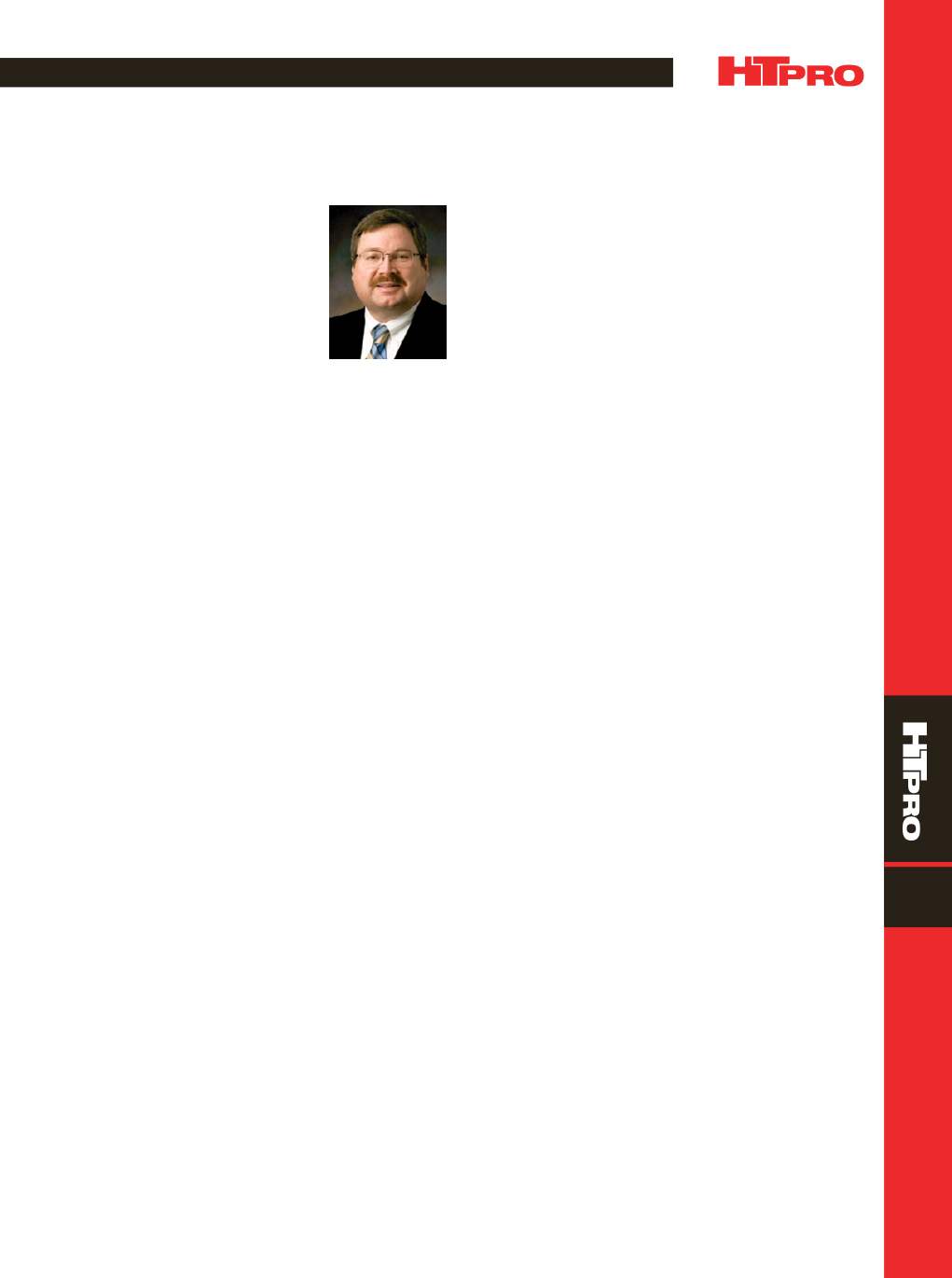
FEATURE
A D V A N C E D
M A T E R I A L S
&
P R O C E S S E S |
M A Y / J U N E
2 0 1 7
5 3
2
Current approaches of leaving residual stresses as an
afterthought that machining suppliers need to worry about
will not work for the future. Defining and controlling residual
stresses within heat treated products is required to enable
controlled, repeatable machining of tight-tolerance compo-
nent geometries. Modeling and simulation tools of various
types are commercially available to provide prediction of
thermal stresses and subsequent residual stresses. Addition-
ally, the input material data required for such modeling and
simulation is critical for accurate, quantitative predictions. A
new entity called the Center for Materials Processing Data is
being formed at Worcester Polytechnic Institute to support
industry with materials property data at manufacturing pro-
cess-relevant conditions. The combination of commercial
software and accurate materials data will enable increased
application of modeling and simulation.
In addition to modeling and simulation, advances in
process monitoring, data capture, and data analytics are be-
coming commonplace and are a needed pillar for required
process control and continuous improvement. The heat
treating industry must take on “Big Data” as equipment
and processes become more complex and final product re-
quirements become more demanding. The combination of
computational modeling and use of data will drive the heat
treating industry forward to meet the evolving demands of
the aerospace industry.
David Furrer, FASM
Senior Fellow Discipline Lead
Manager, Manufacturing Technologies
Pratt &Whitney, Materials and Processes Engineering
AEROSPACE HEAT TREATMENT: ADVANCES
THROUGH MODELING AND DATA
H
eat treatment is a critical manu-
facturing process that drives the
final mechanical properties and
performance of metallic components
and subsequent systems. Unique me-
chanical properties are often the target
for specific heat treating processes,
but other attributes are extremely im-
portant for the aerospace heat treating
industry, including understanding and controlling final part
residual stress and distortion.
Residual stress that results from heat treating process-
es can cause two major issues: distortion and lack of dimen-
sional control during final machining processes, and interac-
tionwithappliedapplication stresses that cangreatly impact
part performance or even part life. The aerospace industry
strives for enhanced component capabilities that enable
overarching systems improvements, especially those that
provide tangible benefits to final customers, such as initial
system costs, fuel efficiency, and durability. Manufacturing
yield and component dimensional control are key attributes.
Many organizations have focused activities aimed at
mitigating heat treatment-induced residual stresses. Model-
ing has advanced to the point where efforts should be taken
to enable industrywide standards for modeling, prediction,
and control of these stresses. There is a need for residual
stresses to be systematically incorporated into product defi-
nitions, which the thermal processing industry can address.
GUEST EDITORIAL
3