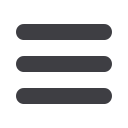
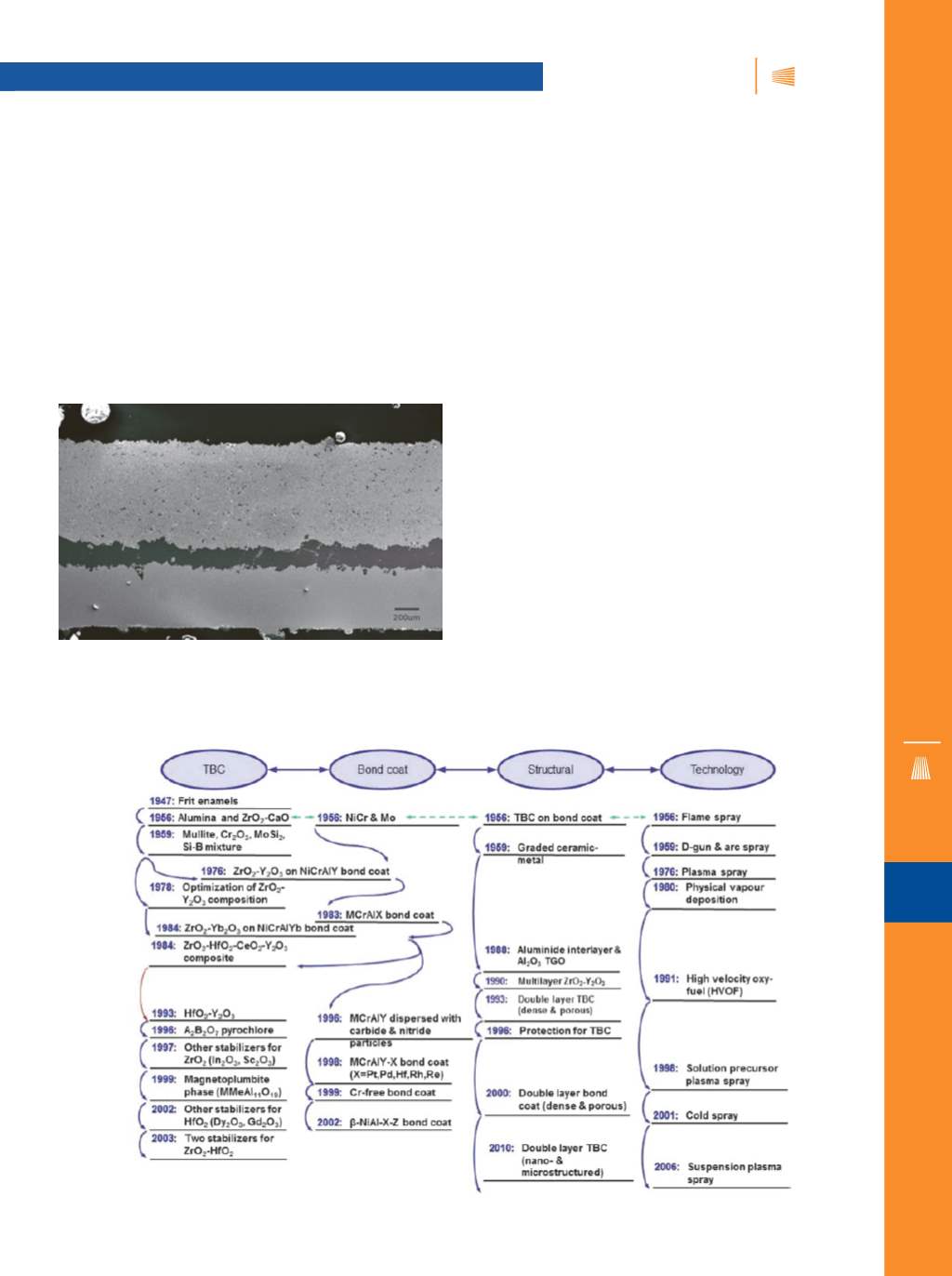
iTSSe
TSS
A D V A N C E D
M A T E R I A L S
&
P R O C E S S E S |
M A Y / J U N E
2 0 1 7
3 9
T
L
|
iTSSe
TSS
FEATURE ARTICLE
5
an abundance of micrographs
[7]
and scientific data to show TS
coatings applied as a thermal barrier. However, pedigreed fi-
nancial data is lacking because the information is proprietary.
The point remains that thermal spray in a thermal barrier
coating (TBC) application is worth the investment. For exam-
ple, a study
[8]
by BCC Research notes that the global market
for TBCs totaled $834.9 million in 2016 and should total near-
ly $1.1 billion in 2021 at a five-year compound annual growth
rate (CAGR) of 5.6%. However, not all of this investment and
growth is aimed toward TS because other advanced technol-
ogies compete for the TBC market. This raises the question:
What is the future of TS in the energy sector?
IS TINKERING WITH COMPOSITIONS
THE ANSWER?
This question may shock many researchers and engi-
neers because their work has centered on finding and refining
TBC layers and compositions that reflect known degradation
and failure mechanisms. Figure 3 shows a typical genera-
tion-1 TBC consisting of a plasma sprayed, 100 to 150-²mthick
MCrAlY bond coat under a 350-²m thick top coat of ZrO
2
-Y
2
O
3
.
Use of TBCs in gas turbine engines enables metal temperature
reductions of about 190 K. Further, materials scientists and
engineers have advanced TBC development over the past 70
years as shown in Fig. 4. Often, this is driven by the push for ef-
ficiency gains, more powerful turbine engines, and the need to
address critical operational issues such as Si-Al-Mg-Ca (CMAS)
oxides that attack and cause coating erosion in gas turbines.
Figure 5 shows a typical generation-3 coating comprising a
multilayer microstructure developed for use in a hypersonic
application.
The science behind composition control is critical for
TBCs because it strongly correlates to engine performance,
efficiency, and lifecycle. The significance of the thermally
grown oxide (TGO) that forms between the bond coat and ce-
ramic overlay during service has been discussed extensively.
The materials engineering approach has been to determine
TGO growth rate and phase composition by measuring its
thicknesses at specific temperatures after soaking for times
that mimic service conditions. Composition control of input
elements (bond coat and ceramic overlay) enable determin-
ing TGO characteristics and influence on TBC longevity. This
Fig. 4
—Development of TBCs over the past 70 years.
Fig. 3
—Micrograph of generation-1 thermal barrier coating (TBC)
consisting of a plasma spray MCrAlY bond coat and ZrO
2
-Y
2
O
3
top coat.