
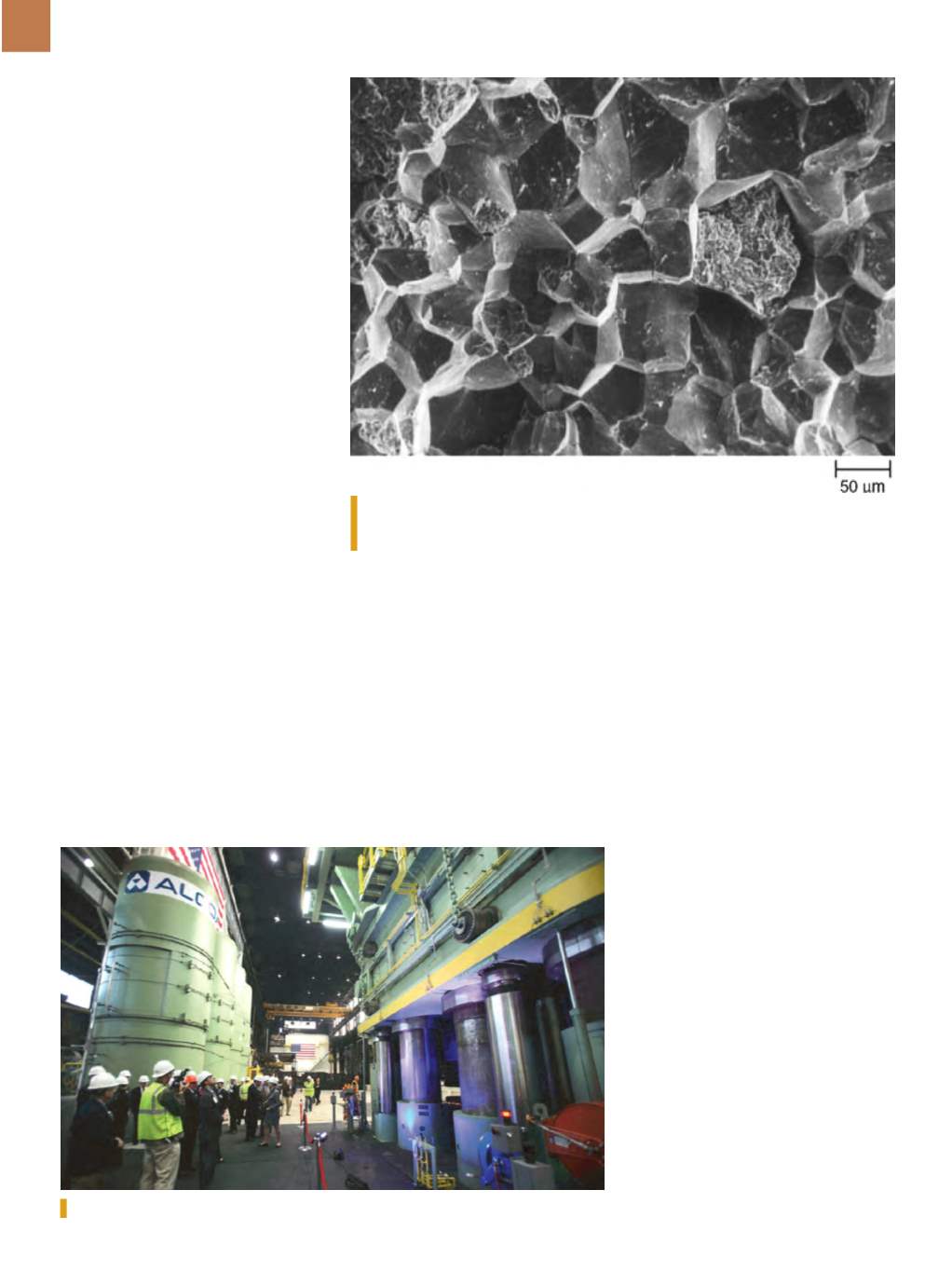
A D V A N C E D M A T E R I A L S & P R O C E S S E S | J A N U A R Y 2 0 1 7
2 6
SYMPOSIUMHIGHLIGHTS
In “The Age of Bessemer Steel,”
AM&P
editor-in-chief Frances Richards
presented the story behind the devel-
opment of the revolutionary processing
pathway that simultaneously reduced
the cost and increased the quality of
steel, fueling the Industrial Revolution
and enabling reliable rail transport
across continents. Based on the arti-
cles, “Metallurgy Lane: The Age of Steel”
(Parts I and II) published by ASM life
member Charles Simcoe in this mag-
azine, the talk highlighted that both
Henry Bessemer (of Sheffield, England)
and WilliamKelly (of Kentucky) simulta-
neously and separately (around 1850)
discovered that bubbling air through
molten blast furnace cast iron removes
carbon, thus enabling efficient steel
production.
Along with Robert Mushet’s dis-
covery that the addition of manganese
reduces “hot-shortness” by manganese
sulfide formation, these developments
allowed William Kelly to open a small
plant using his process in Wyandotte,
Mich., in 1863. At the same time, Alexan-
der Lyman Holley was able to navigate
the patent space in the U.S. and build the
first Bessemer steel plant in Troy, N.Y., in
1865. By the end of the century, Andrew
Carnegie became the leading producer
of steel and the industrial and techno-
logical revolution was at full steam.
Jon Tirpak, FASM, immediate past
president of ASM, then spoke about
the technology development that
enabled the move from hammer forg-
ing of steels in the years prior to World
War II to hydraulic press use to control
strain rates. This development allowed
light metal forging and enabled the
burgeoning aerospace industry. After
the war, technologies originally devel-
oped in Germany were transferred to
the U.S. and U.S.S.R., and a race to pro-
duce the largest presses to enable the
production of large aluminum, magne-
sium, titanium, and steel components
ensued. ASM International recognized
the historical significance of six of these
heavy hydraulic presses worldwide in
2013 by naming them ASM Historical
Landmarks.
Press size correlates directly to
the size of components that can be pro-
duced, which determines the largest air-
craft size possible. In a worldwhere new
technologies for manufacturing compo-
nents are being developed, including
additive manufacturing, this talk high-
lighted the critical need to teach and
develop expertise in processes such as
forging. Unlike many other techniques,
materials produced by forging feature
refined grain structures and substantial
mechanical work, and allow designers
flexibility and opportunities to reduce
weight in large structural components
where properties and repeatability are
critical to performance.
The third speaker, Prof. Rian Dippe-
naar from the University of Wollongong,
discussed development of high-quality
lenses that enabled optical metallogra-
phy use, which in turn allowed for iden-
tification of phases and constituents in
microstructures, transforming metal-
lurgy. Initial observations using optical
Alcoa’s 50,000 ton press, Cleveland, refurbished in 2012.
Brittle intergranular fracture along prior austenite grain boundaries in carbon steels
quenched and tempered tomartensite, known as quench embrittlement.