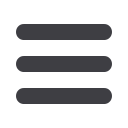
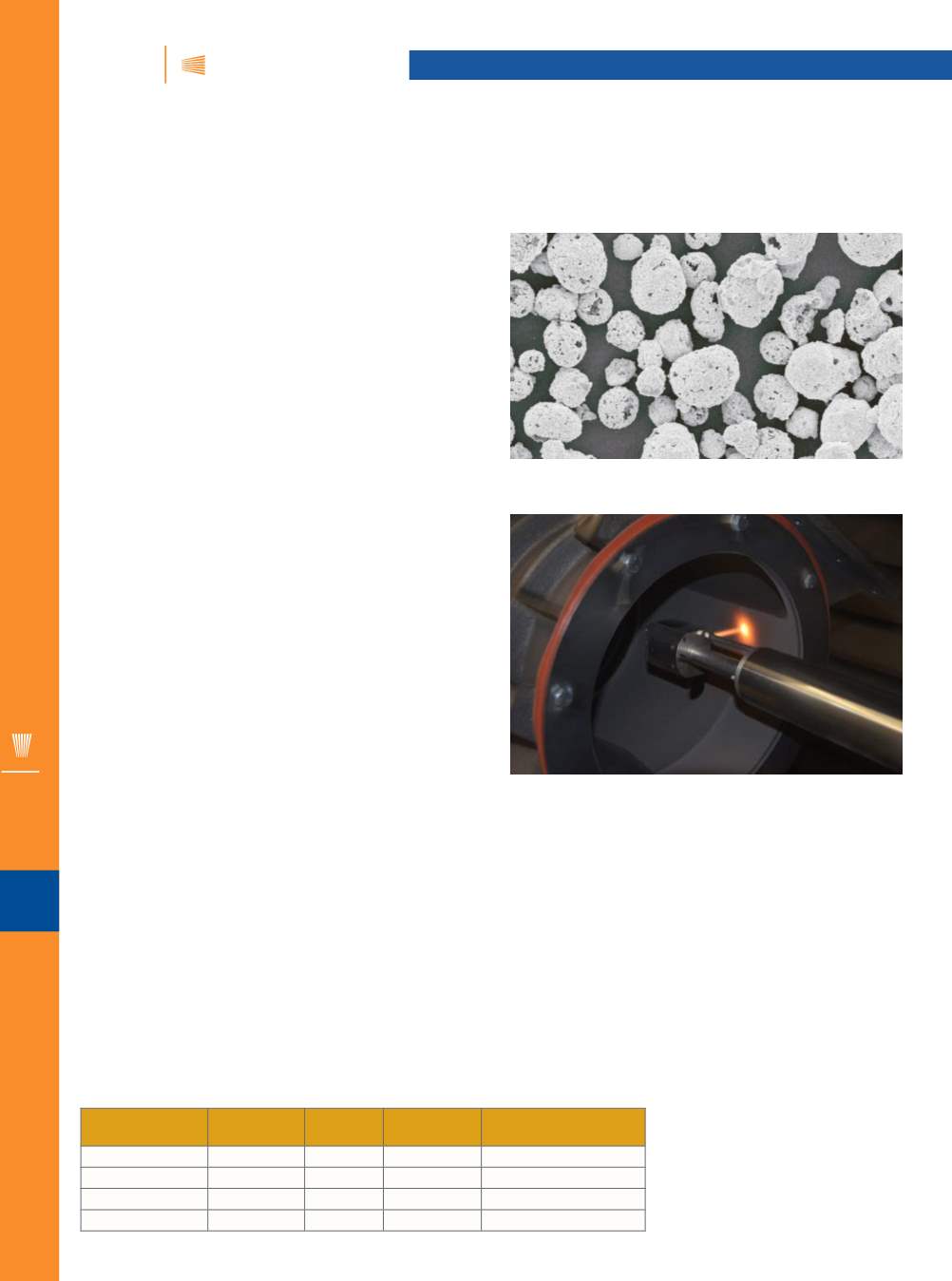
iTSSe
TSS
A D V A N C E D M A T E R I A L S & P R O C E S S E S | J U L Y / A U G U S T 2 0 1 6
4 0
iTSSe
TSS
10
CASE STUDY
REASON TO CONSIDER SURFACING
Using thermal spray to coat the interiors of pipes and
tubes used in heavy duty applications enhances mechani-
cal properties and extends component lifetimes. However,
thermal spray processing of internal diameters (IDs) creates
a range of processing challenges related to both workpiece
diameter and length. The physical size of equipment, hoses,
and spray distance boundaries—along with temperature and
contamination issues—are considerations for both equipment
andmaterial manufacturers.
H.C. Starck GmbHandUniqueCoat Technologies recently
conducted a range of trials to optimize coating properties pro-
duced with new hardware designed to coat IDs down to less
than 5 in., an application area that has traditionally been a
challenge for the production of high quality coatings.
VALUE OF COATING
The flame characteristics (thermal and kinetic) had to
be matched to a spray material that would provide coating
quality comparable to that achieved by larger standard coat-
ing equipment. This is especially important for heavy duty
industries such as oil and gas, where ID protection in drilling
and pumping applications has long been an area requiring
improvement. In order tomatch the spray device to the correct
powder consumable, a few simple principles must be taken
into account:
1. Can the hardware be sized to allow for consistent
energy transfer (both thermal and kinetic) to the pow-
der, in order to reach the desired particle temperature
and velocity to produce a high quality coating—dense,
hard, and well bonded, at a reasonable efficiency?
2. Can the powder be produced to a very tightly con-
trolled specification on a consistent basis so that opti-
mum coating properties are reliable and reproducible
for ID applications?
OPTION
Specially sized materials of very specific morphology
were used to run coating trials to find the optimum match
between the small ID torch’s energy (UniqueCoat’s I7 torch)
OPTIMIZING COATING MATERIALS FOR
HEAVY DUTY APPLICATIONS
TABLE 1
—
TRIAL RESULTS
Powder
designation
Hardness –
HV300 Porosity Powder
sizing (µm)
Morphology
Amperit 558.185
1140
<1% -30 + 5
Agglomerated sintered
Amperit 554.071
1380
<1% -25 + 5
Sintered crushed
Amperit 554.090
1540
<1% -20 + 5
Sintered crushed
Amperit 554.067
1502
<1% -15 + 5
Sintered crushed
Fig. 1 —
Amperit 558—spray dried/agglomerated and sintered.
Courtesy of H.C. Starck GmbH.
and the size and thermal conductivity of the spray material
(Fig. 1). Coating chemistry was WC/Co/Cr (86/10/4)—a coating
commonly used in the oil and gas industry due to its mix of
wear and corrosion resistance. Trial results appear in Table 1.
BENEFITS
The I7 torch coating the interior of a rotary valve is shown
in Fig. 2, an application that will be run as part of a large scale
evaluation of this emerging technology. Further trials will
focus on optimizing the performance of specialized coatings
for erosion and slurry resistance.
iTSSe
For more information:
Michael Bre-
itsameter is senior global sales man-
ager, H.C. Starck North American
Trading LLC, 45 Industrial Place, New-
ton, MA 02461, 617.893.7367, michael.
breitsameter@hcstarck.com, www.
hcstarck.com.
Fig. 2 —
UniqueCoat’s I7 torch coating the internals of a rotary valve.