
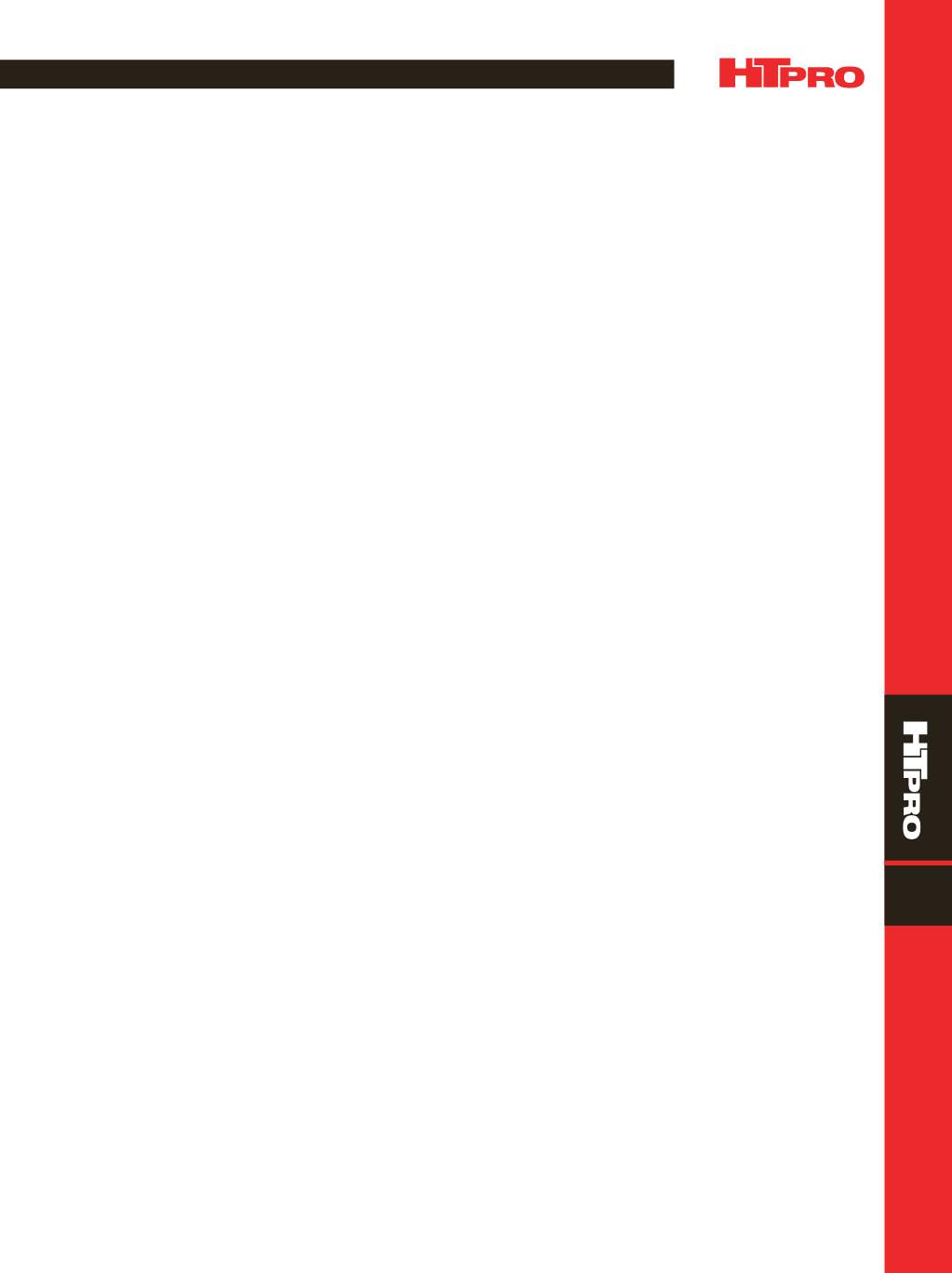
3 5
A D V A N C E D
M A T E R I A L S
&
P R O C E S S E S | J U N E
2 0 1 6
FEATURE
9
INDUCTION COUPLED THERMOMAGNETIC PROCESSING:
A DISRUPTIVE TECHNOLOGY
Properties and performance of lower cost “simple” alloy steels processed using induction coupled
thermomagnetic processing can rival those of conventionally processed, expensive specialty alloys.
Aquil Ahmad,*
(retired), Eaton Corp., Cleveland;
George Pfaffmann, FASM,*
Ajax Tocco
Magnethermic, Madison Heights, Mich.;
Gail Ludtka*
(retired) and
Gerard Ludtka, FASM,*
Oak Ridge National Laboratory, Tenn.
O
ne of the major goals of the U.S. Department of
Energy (DoE) is to achieve energy savings with a
corresponding reduction in the carbon footprint.
With this in mind, the DoE sponsored the Induction Cou-
pled Thermomagnetic Processing (ITMP) project with
major partners Eaton Corp., Ajax Tocco Magnethermic,
and Oak Ridge National Laboratory (ORNL) to evaluate the
viability of processing metals in a strong magnetic field.
Processing materials in such a manner is a novel,
game changing concept
[1]
. Applying a strongmagnetic field
with controlled-frequency induction heat treatment to
metals results in properties not achievable using conven-
tional processing techniques. The magnetic field produces
a change in thermodynamics that alters conventional
phase diagrams resulting in new phase equilibria and sol-
ute solubilities. This provides opportunities to develop
alloys with novel microstructures and improved physical
and mechanical properties. In addition, phase transfor-
mation kinetics, especially for tempering, are dramatically
accelerated. This results in improved processing efficiency
and refined microstructural features, such as finer marten-
site-lath populations and large amounts of finer carbides
after tempering.
The use of a coupled induction heat treatment with
high magnetic field heat treatment enables the develop-
ment of metals with improved performance using faster
processing times and less energy. The technology allows
substituting lower cost alloys for more expensive alloys
[2]
while achieving greater combinations of strength and
ductility. In addition, microstructures can be tailored
for improved magnetic properties, wear resistance, and
mechanical performance. Processing lower cost, simple
alloy steels under a strong magnetic field achieves proper-
ties comparable to those achieved in highly alloyed steels
processed using conventional techniques. In addition,
the enhanced strength and toughness in ITMP materials
improves power density in a significant number of indus-
trial mechanical components.
This article discusses some of the demonstrated
improved mechanical properties achieved for steels in
*Member of ASM International; George Pfaffmann is recently deceased.
the ITMP project. The technology can also be applied to
forging operations resulting in lower temperature forma-
bility, thus reducing energy consumption while improving
mechanical properties. These results would be beneficial
in components such as gears, shafts, net-shape forged
valves, and forging dies. The technology is also applicable
to non-ferrous alloys. For example, ITMP reduces solution
heat treating and aging times by 80% for precipitation
hardening aluminum alloys.
MAGNETIC PROCESSING DEFINED
Earth’s magnetic field is 60micro-tesla (
µ
T) at the sur-
face. By comparison, the industrial prototype supercon-
ducting magnet system at ORNL is capable of 9 T, 150,000
stronger than the earth’s magnetic field. Application of a
9-T magnetic field in heat treat processing achieves prop-
erties in low cost alloy steels that rival properties achieved
in more expensive higher alloy steels. Figure 1 shows the
potential for improvement in steel performance versus
cost per pound. The trend line indicates that the potential
of thermomagnetic technology is unlimited.
BENEFITS OF ITMP
A strong magnetic field significantly affects the iron-
iron carbide (Fe-Fe
3
C) phase diagram, as well as the kinetic
behaviors of continuous cooling and isothermal transfor-
mation. Benefits of ITMP include:
•
Accelerated transformation kinetics
•
Refined microstructure
•
Fine carbide dispersion
•
Minimum grain boundary segregation
•
Mitigation of segregation banding
•
Reduced volume fraction of retained austenite
•
Improved mechanical properties including tensile
and yield strengths, and ductility (elongation and
reduction in area)
Rotating beam bending fatigue
was evaluated using
R.R. Moore type test equipment according to ASTM E466
“Standard Practice for Conducting Force Controlled Con-