
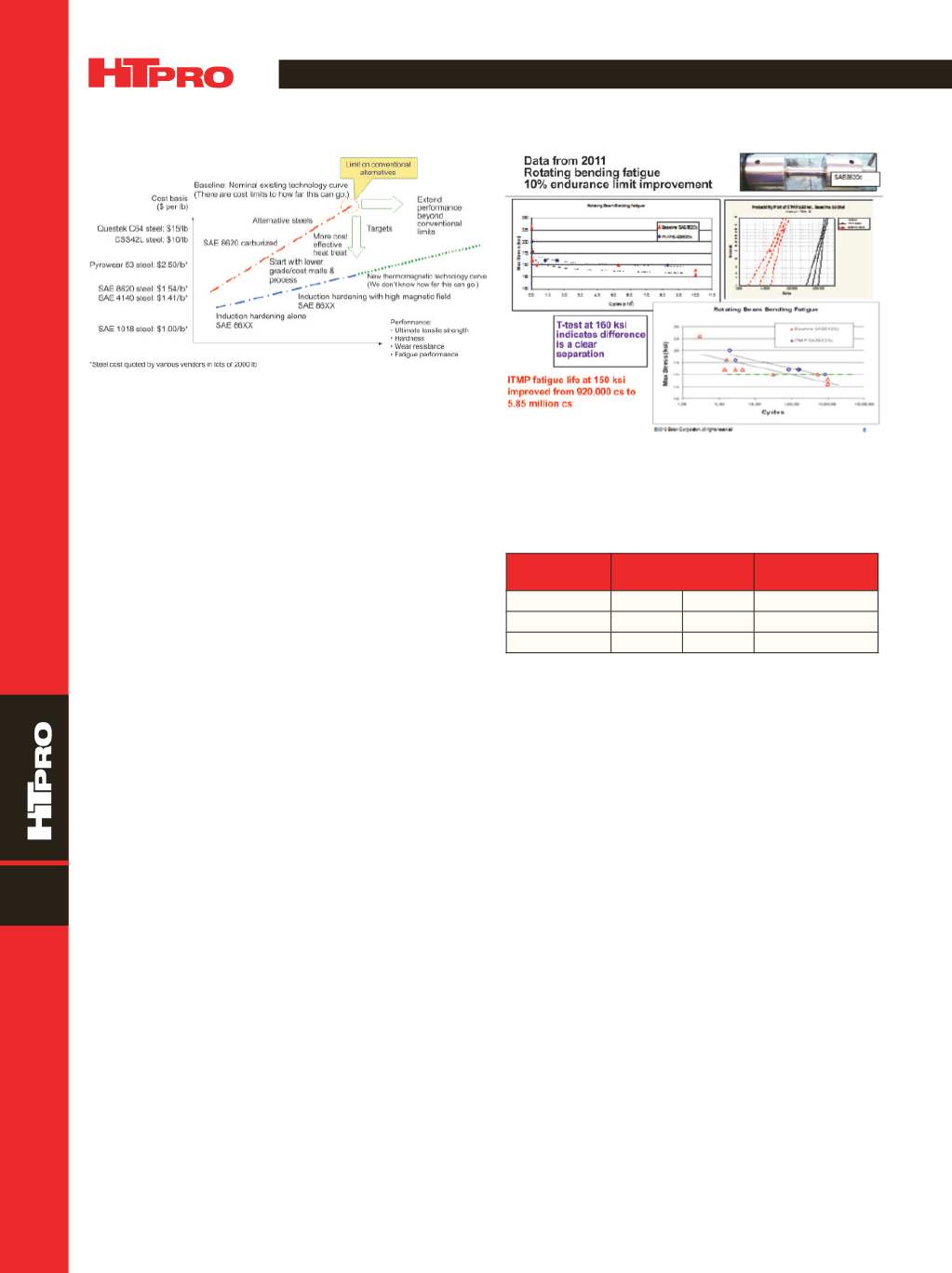
3 6
A D V A N C E D M A T E R I A L S & P R O C E S S E S | J U N E 2 0 1 6
FEATURE
10
Fig. 1 —
ITMP potential for improvement in steel performance
versus cost per lb.
Fig. 2 —
Improvement in rotating bending fatigue life of ITMP
samples over baseline properties.
stant Amplitude Axial Fatigue Tests of Metallic Materials.”
Figure 2 shows an improvement of 6.4 times for ITMP sam-
ples over baseline carburized samples at a stress of 150
ksi (sample size: 6 in. long with 2 in. taper section; 0.75 in.
diam.; 0.375 in. minor diam.).
Evaluation of reverse torsion fatigue in torsion shafts
was not completed due to incompatibility of sample size
and processing equipment. With the availability of a new
industrial prototype thermomagnetic processing facil-
ity (Fig. 3), further studies were conducted on gear tooth
bending fatigue.
Reverse idler gear single-tooth fatigue.
Gears were
processed in an 8-in. diameter superconducting mag-
net system incorporating a 10-30 kHz, 200-kW induction
heating power supply with an integral 75 gpm polymer
quench capability. Heat treated gears were shot peened
to the same parameters as baseline gears. The goal was
to improve single tooth bending fatigue by 200%. Tech-
nical challenges included developing a fine microstruc-
ture-scale understanding of ITMP and performing finite
element analysis (FEA) and modeling calculations.
The first of two sets of experimental runs fell short
of expectations and processing time and temperature
parameters were revised for the second series of exper-
iments. The new parameters for rapid heat up and hold
time at temperature were based on Ajax Tocco calculations
for achieving appropriate solid solution of carbon in the
austenite phase, determined from results of joint research
by Colorado School of Mines, ORNL, and Torrington
[3]
. FEA
work was conducted such that the targeted carbon con-
tent in austenite before rapid quenching was achieved in
the gear root without overheating the gear tip. (Note: Hot
root, cool tip, and cold core.)
Single-tooth bending-fatigue test results for the
second batch of gears showed an improvement of 2.5 to
5 times that of baseline gears (Fig.4). Probability analysis
clearly demonstrates the mean shift in the curve for 202 ksi
and 215 ksi. Results are as follows:
Stress level,
ksi
Mean cycles
Baseline ITMP Improvement
174
70,751 360,658
5.1
×
202
23,822 75,626
3.17
×
215
16,344 40,950
2.5
×
Hardness and case depth of ITMP and as-carburized
gears are comparable. ITMP dramatically accelerates the
tempering process resulting in significant energy efficiency
improvements, as well as reducing the carbon footprint.
For example, tempering as-carburized gears at 350°F via
ITMP required only 10 minutes compared with two hours
using conventional processing.
ITMP gears have a refined microstructure with a fine
dispersion of carbides and negligible segregation at the
grain boundaries compared with the microstructure of
baseline gears (Fig. 5). The thermodynamic effect of the
strong magnetic field raises the martensite start tem-
perature (M
s
), resulting in a reduced volume of retained
austenite. Induction hardening alone does not have this
fundamental driving force. The lower volume percent of
retained austenite and fine dispersion of carbides com-
pared with the baseline microstructure leads to improved
properties plus higher wear resistance.
CONCLUSIONS
•
ITMP modified processing parameters on the reverse
idler gears demonstrated major improvement in
fatigue life (~3x) at very high stress levels.
•
Tempering parts for 10 minutes in a magnetic field
provides improved fatigue life properties compared
with the conventional tempering for two hours
at 350°F.