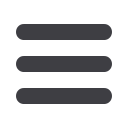
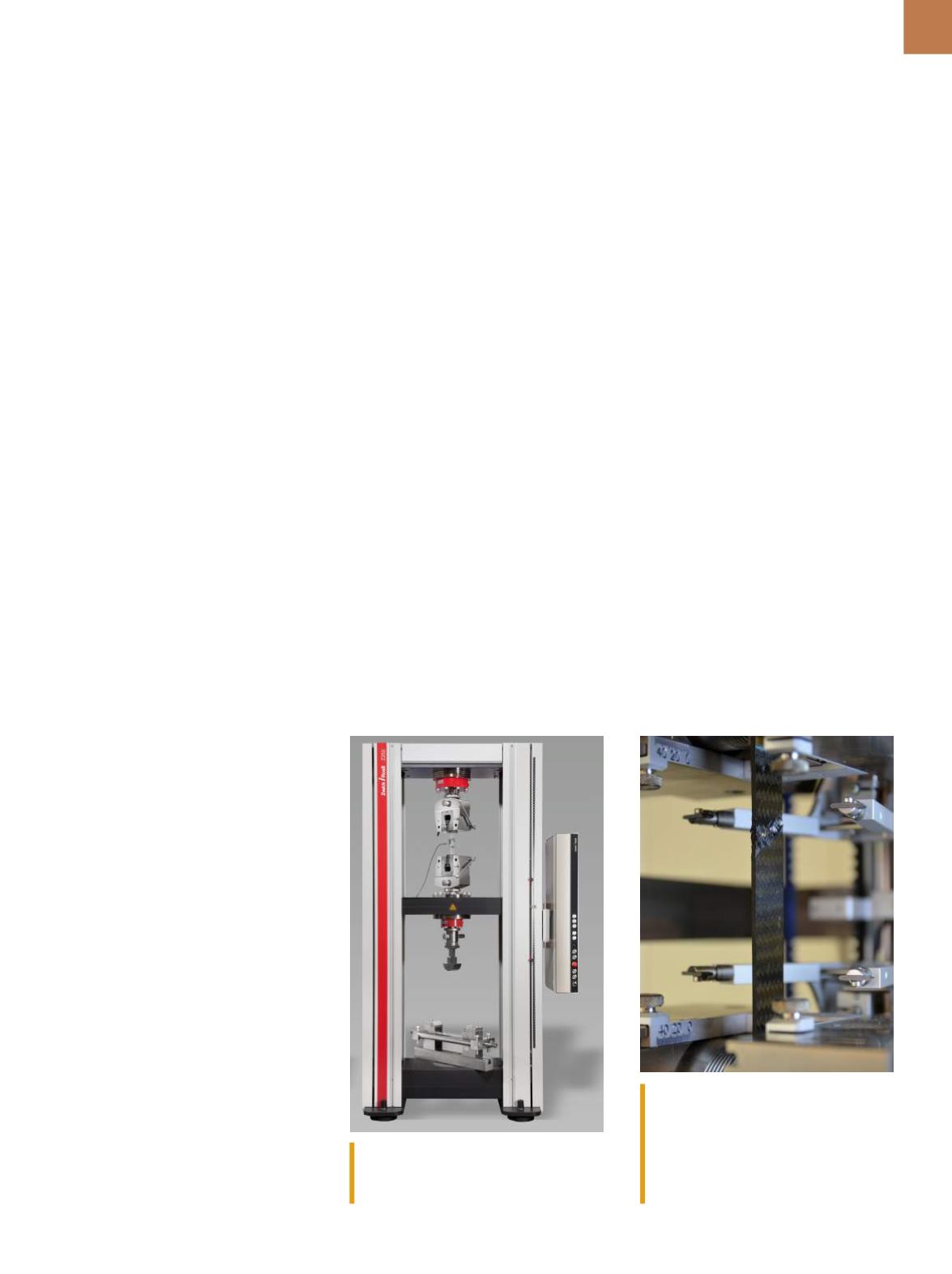
A D V A N C E D
M A T E R I A L S
&
P R O C E S S E S |
A P R I L
2 0 1 6
1 7
M
echanical testing plays a major
role in research and education,
product development and de-
sign, and quality control. Tests can be
conducted using a wide range of stat-
ic and dynamic materials testing ma-
chines, which engineers and scientists
frequently use during product develop-
ment. Mechanical testing incorporates a
wide range of techniques, from common
tensile and compression tests to flexur-
al or torsional characterization. Testing
may also occur under ambient or non-
ambient conditions, with widely var-
ied temperatures and environmental
conditions.
ELECTROMECHANICAL
SYSTEMS
Electromechanical (EM) testing
systems are often applied to static test-
ing applications in tensile or compres-
sive mode. Two types of load frames
are available for EM testing systems,
single-column and dual-column frames.
Dual-column systems come in bench-
top and floor-standing models. Addi-
tional elements of EM systems include
a load cell, a crosshead, and a means of
measuring extension, also commonly
referred to as elongation. A load cell is
a transducer that creates an electrical
signal whose magnitude is directly pro-
portional to the force being measured.
A moveable crosshead moves up or
down at a given rate of speed specified
by the standard to which the test is be-
ing conducted. Some applications re-
quire a constant rate of extension while
others require a ramped rate.
As an example, EM testing systems
from Zwick incorporate modern design
elements to deliver the most reliable
test results possible. In these systems,
AC drive technology couples virtually
maintenance-free operation with the
advantages of digital control. In addi-
tion, an innovative motor feedback sys-
tem ensures excellent constant velocity
properties, even at very low speeds.
These test machines are also equipped
with a patented, flexurally stiff hol-
low profile with a guide cylinder, while
long crosshead guides with a large
surface area provide extremely precise
guidance. This combination minimizes
undesirable mechanical influences on
the specimen.
EM testing systems are particular-
ly beneficial for applications that call
for high levels of precision. Applica-
tions that require support for measur-
ing complex strain may be addressed
through the use of an extensometer.
The requirements to be met by an ex-
tensometer are determined primarily
by the characteristics of the material to
be tested. This includes its shape and
dimensions, test requirements, and
the formal standards that must be met.
These define the gage length, accuracy,
test sequence, and environmental con-
ditions, such as the test temperature.
During the tensile test, the elongation
of the gage section is recorded against
the applied force. Typically, elongation
is measured between two fixed points
on the specimen.
The primary scope of tests ad-
dressed by EM systems are classic static
materials tests such as tensile, flexure,
or bending tests. EM represents the
most suitable technology because for
these kinds of tests, especially tensile
tests, a high degree of control and pre-
cision in strain rate measurement is
relevant. This is only possible with EM
systems. In addition to materials tests,
EM systems are also applicable to com-
ponent tests when high precision is
necessary.
SERVOHYDRAULIC SYSTEMS
Servohydraulic testing machines
may be used in static, dynamic, or fa-
tigue materials testing applications.
They operate through a closed-loop
system consisting of a bidirectional hy-
draulic actuator linked to the test speci-
men; a servo valve and controller for ad-
justing actuator position, velocity, and
force; a load frame with close-coupled
hydraulic power source; and an elec-
trical feedback loop enabling the test
variables to be controlled utilizing po-
sition and load transducers. Although
they require infrastructure for both
electrical and hydraulic connections,
servohydraulic testing machines can
be a cost-effective static testing choice
at very high forces (where screw-driven
electromechanical machines may be
expensive to produce) or if a high test-
ing speed is required.
Electromechanical testing systems within
the AllroundLine contain dual test areas
to support efficiency in testing.
The makroXtens extensometer incor-
porates unique knife edges that remain
in contact with the test specimen up
through breakage. Pictured here is a car-
bon fiber composite specimen undergo-
ing brittle failure.