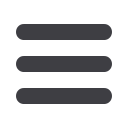
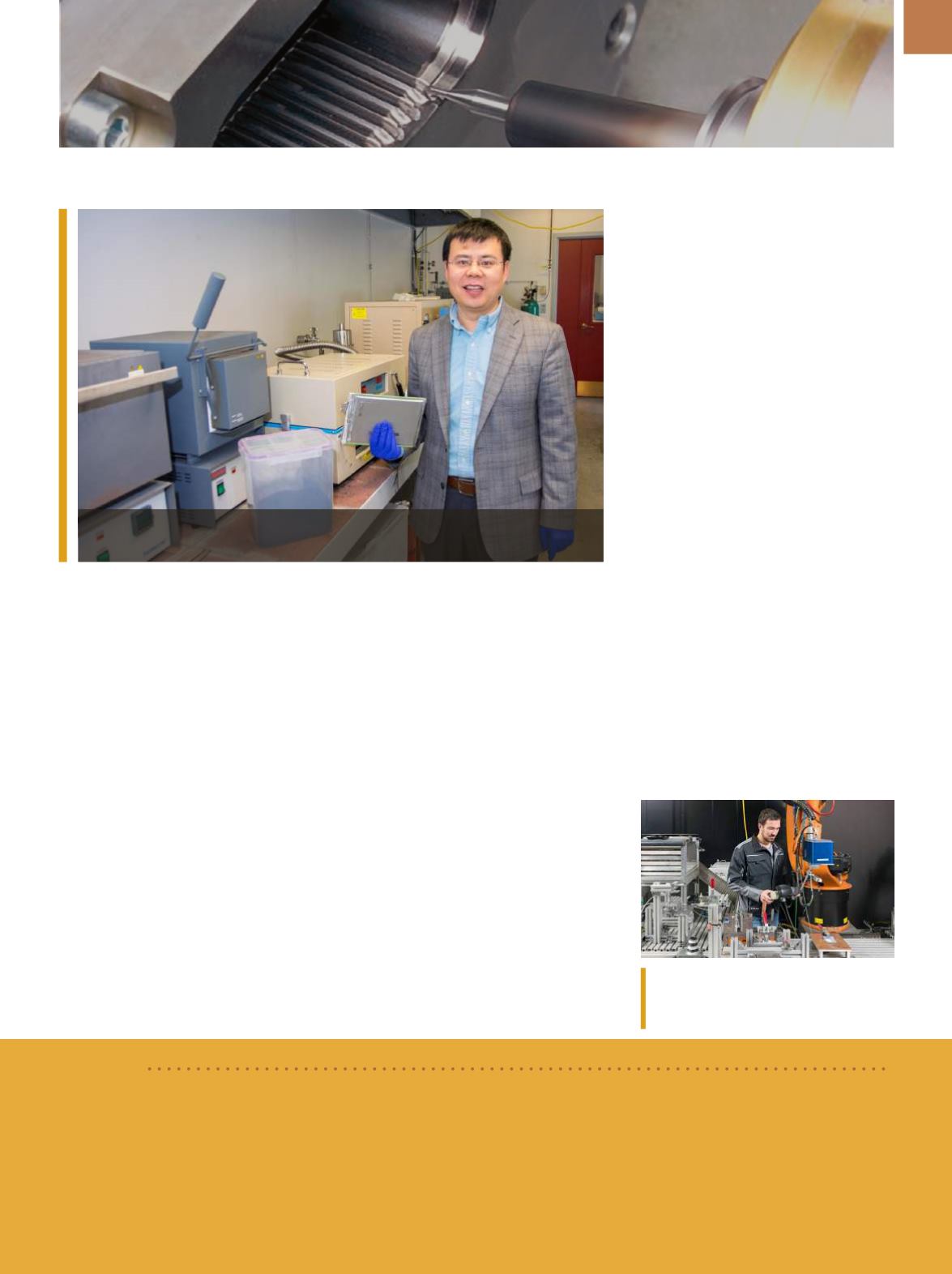
A D V A N C E D
M A T E R I A L S
&
P R O C E S S E S |
A P R I L
2 0 1 6
1 3
PROCESS TECHNOLOGY
Yan Wang holds a Li-ion battery cell used in electric vehicles. His process breaks down
the batteries to produce the powder shown on the left.
NO-SORT BATTERY RECYCLING
A team of researchers at Worces-
ter Polytechnic Institute (WPI), Mass.,
developed a novel process for recycling
lithium-ion (Li-ion) batteries and using
the recovered cathode material to pro-
duce new plug-in hybrid electric vehicle
battery cells. Because commercially
produced Li-ion batteries use a variety
of chemistries for their cathodes, re-
cyclers must sort these batteries, a
labor-intensive and expensive process.
The new method works with any cath-
ode chemistry, so little to no sorting is
required. Batteries are shredded, and
the steel, aluminum, iron, copper, and
plastics are recovered and recycled.
Cathode materials—lithium, nickel,
manganese, and cobalt—are recovered
and used to synthesize new cathodes
in a formula that can be adapted based
on industry needs. Using this process,
Doctoral candidate André Heckert is
working with a laser to fuse plastics with
metals. Courtesy of Ulrich Benz/TUM.
BRIEFS
UTC Aerospace Systems,
Charlotte, N.C., opened a Materials and Process Engineering (MPE) laboratory in Windsor Locks,
Conn., to support research, engineering, and production. The lab has 3D printing capabilities for fabricating metal and plastic
engineering development parts, as well as high-temperature composite capabilities for developing carbon-carbon and silicon
carbide-based composites. UTC also established the Materials Engineering Center of Excellence at the
University of Connecticut
(UCONN). The agreement includes a five-year, $1 million commitment to work with UCONN in areas such as additive manufactur-
ing, high-temperature composites, and thermoplastics.
utcaerospacesystems.com.
the WPI team was able to recycle up to
80% of the cathode materials from un-
sorted batteries. Researchers say their
approach could cut the cost of cath-
ode materials for vehicle batteries by
more than 30%. Further, WPI received a
$1 million contract from The United
States Advanced Battery Consortium
LLC to scale-up the process from coin
cells to 25 Ah cells.
wpi.edu.
HEAT IS ON IN
MATERIALS JOINING
Materials such as fiber-reinforced
plastics and light metals have led to
low-density components in the automo-
bile, aircraft, and aerospace industries,
although joining these materials has
proved challenging. Researchers fromthe
Institute for Machine Tools and Industrial
Management at the Technical Universi-
ty of Munich (TUM) developed a secure
joining technique that uses heat appli-
cation. Their process involves texturing
the metal surface with a laser beam to
produce tiny hollows, pressing the metal
and plastic together, and then applying
heat until the plastic melts and flows into
the hollows. On cooling, a stable bond is
formed between the twomaterials.
Depending on the particular plas-
tic, researchers vary the depth of the
laser-beam grooves from nanometers to
a fewmillimeters. A groove pattern a few
tenths of a millimeter deep is suitable
for plastics reinforced with short fibers,
while fine surface structures are effective
for continuous fiber-reinforced plastics.
Different methods of heating are used
as well. A laser beam can melt plastic,
while friction press joining creates ther-
mal energy by pressing a rotating cylin-
drical tool against the metal surface. For
a fast bond, researchers use NanoFoil,
which can briefly reach a temperature as
high as 1000°-1500°C when ignited. One
possible application of this technology is
the rapid joining of metal cable clips to
an aircraft fuselage via a thermoplastic
intermediate layer.
www.iwb.tum.de/en.