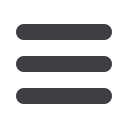
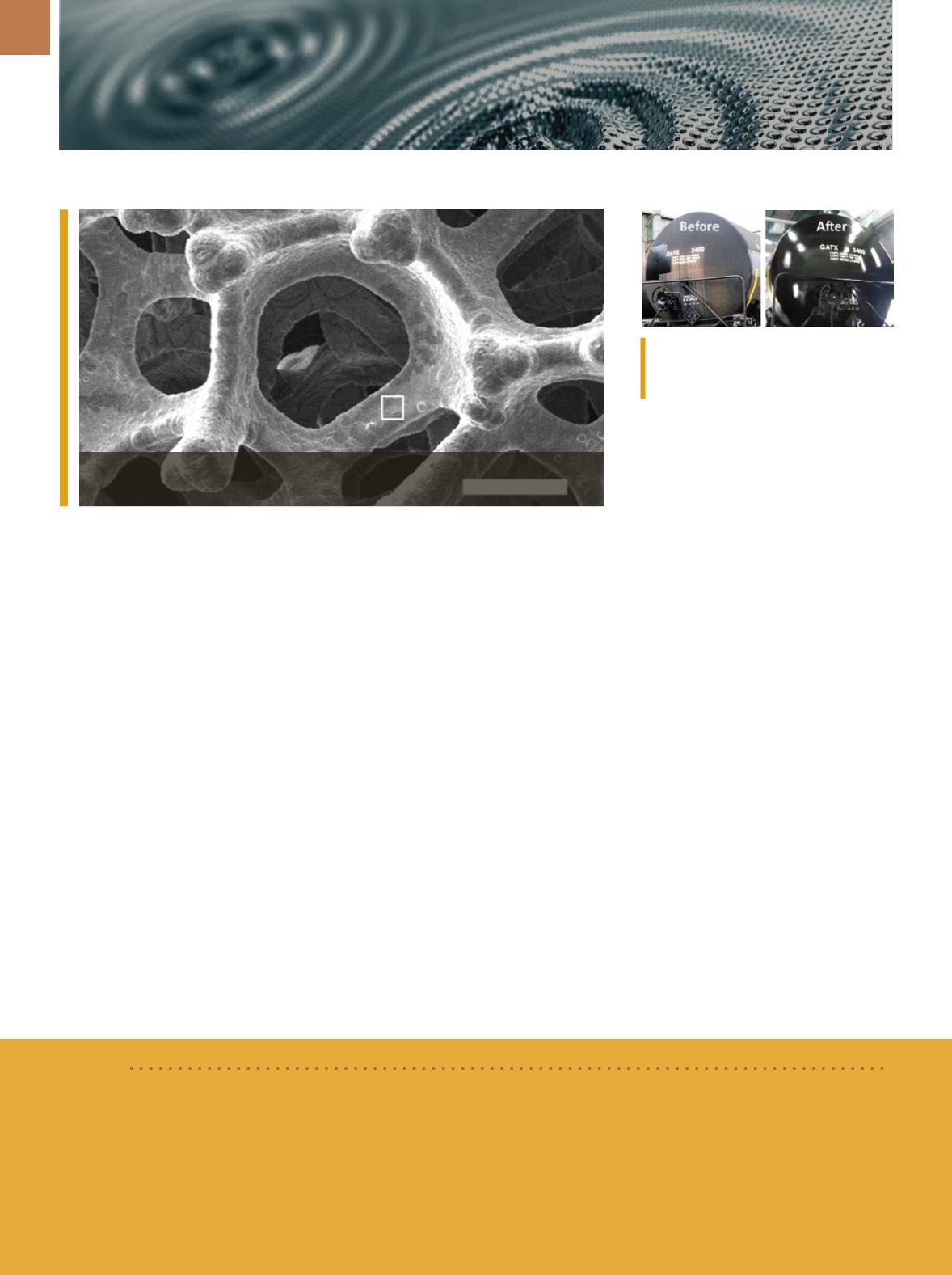
A D V A N C E D M A T E R I A L S & P R O C E S S E S | J U N E 2 0 1 5
1 6
SURFACE ENGINEERING
NEW ELECTRODE FOR
SPLITTING WATER
University of New South Wales, UK,
scientists developed a highly efficient
oxygen-producing electrode for split-
ting water that could potentially scale
up industrial hydrogen production. The
technology is based on an inexpensive,
specially coated foam material that lets
the bubbles of oxygen escape quickly.
“Our electrode is the most efficient ox-
ygen-producing electrode in alkaline
electrolytes reported to date, to the best
of our knowledge,” says Chuan Zhao of
the School of Chemistry. “It is inexpen-
sive, sturdy, and simple to make, and
can potentially be scaled up for industri-
al scale water splitting.”
Inefficient and costly oxygen-pro-
ducing electrodes are one of the major
barriers to the widespread commercial
production of hydrogen by electrolysis,
where the water is split into hydrogen
and oxygen using an electrical current.
Unlike other water electrolyzers that
use precious metals as catalysts, the
new UNSW electrode is made entirely
of two non-precious and abundant met-
als—nickel and iron. Commercially avail-
able nickel foam, which contains holes
roughly 200
μ
m across, is electroplated
with a highly active nickel-iron catalyst,
reducing the amount of costly electrici-
ty required for the water-splitting to oc-
cur.
For more information: Chuan Zhao,
+612.9385.4645,
chuan.zhao@unsw.edu. au, www.unsw.edu.au.
INDUSTRIAL COATING
PROTECTS OXIDIZED
TANK CARS
Over the last two years, Industri-
al Solutions USA, Sioux Falls, S.D., has
conducted two application demonstra-
tions at GATX’s Hearne, Texas, facility
using Nano-Clear Industrial (NCI) coat-
ing manufactured by Nanovere Technol-
ogies, Mich. NCI was spray applied over
SEM image shows the porous structure of the nickel foam electrode. Scale bar is
200
μ
m.
BRIEF
ASTM International,
West Conshohocken, Pa., announces a new
Standard Specification for Nickel-Cobalt Alloy Coat-
ing.
The document outlines requirements for corrosion-resistant coatings of electrodeposited nickel-cobalt on metal-
lic substrates and electrodeposited nickel-cobalt used for electroforming. It also incorporates a classification scheme
that establishes service conditions for thickness, classes of deposits based on the level of monitoring, and type based
on supplemental coatings used after deposition. Coating thickness ranges from 5 to >30
μ
m and can be applied to
machined parts, springs, latches, threaded parts, fasteners, and other components.
astm.org.
Oxidized tank car before and after with
Nano-Clear Industrial coating. Courtesy
of PRNewsFoto/Industrial Solutions USA.
two highly oxidized tank cars and over
one newly painted tank car. The coated
tank cars were then put back into service
throughout the U.S. for a 12-month per-
formance study to provide a long-term,
best practice solution to the epoxy paint
oxidation issue on tank cars.
The black epoxy mastic current-
ly used on the tank cars is continually
exposed to high levels of UV rays and
oxidizes rapidly. Highly oxidized epoxy
paint coatings fall short in areas of abra-
sion, chemical, and corrosion resistance.
UV tests conducted during the two-year
study on the NCI coating by two different
OEMs confirm no discoloration, chalk-
ing, or delamination from the substrate
or between coats after 1500 hours (the
equivalent of 18 months), and 4000
hours, respectively. NCI penetrates
deep into the smallest pores of paint,
enhancing the underlying color and im-
proving gloss while also increasing re-
sistance to UV rays, abrasion, corrosion,
and chemicals. Nano-Clear eliminates
the need to prematurely repaint, sav-
ing millions of dollars in maintenance
costs and thousands of pounds of VOCs.
industrialsolutionsusa.com.