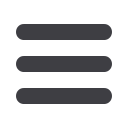

A D V A N C E D
M A T E R I A L S
&
P R O C E S S E S |
M A Y
2 0 1 5
2 3
results is that the exceptional creep
properties were obtained without any
Re additions.
These properties underlie the cen-
tral reason for the current proposal to
revive ODS alloys as turbine blade ma-
terials. Exceptional creep properties
were already demonstrated in com-
positions that are inherently ductile,
oxidation and corrosion resistant, and
of acceptable density. Further, design
of ODS alloys is comparatively unex-
plored, so the opportunity for future
improvements is quite large. For ex-
ample, MA6000’s high Cr content (15%)
and low refractory metal content reflect
its targeted application of industrial gas
turbines and betrays its age—and is a
major reason for optimism in predicting
improved properties via alloying.
POTENTIAL BARRIERS
TO ODS ALLOYS
As mentioned previously, in the
1980s and 90s, ODS alloys suffered from
competing with single-crystal superal-
loys. Described here are past ODS short-
comings, which can serve as a list for
technology improvements required to
develop these alloys for future engines.
Competition from single crystals
in terms of creep strength
. Continued
improvements in single-crystal proper-
ties since the 1980s are reported in the
literature, in contrast to very limited
improvements in ODS alloys, especial-
ly over the temperature range of inter-
est from 750
o
to 1100
o
C. As described
previously, it is under-appreciated that
exceptional creep properties were gen-
erated in Re-free alloys by Glasgow
in 1976 and Kawasaki, et al., in 1990.
These studies may have been discount-
ed due to other issues with ODS alloys,
but they have more significance now
because development of single-crystals
appears to have reached a point of lim-
ited improvements.
Competition from single crystals in
terms of cost and near-net shape pro-
cessing with internal cooling passages
.
The high-cost processing route for ODS
alloys was exacerbated in components
with complex hollow geometries. How-
ever, the cost differential has shrunk,
because advanced single-crystal alloys
contain substantial amounts of ex-
pensive elements such as Re, Ru, and
Ta. Also, complex cooling geometries
can be achieved by fabricating blades
from stacked wafers with etched cool-
ing passages
[21]
. While the methods are
not inexpensive, they became more vi-
able as they matured over the past 20
years. Another potential route to lower
costs is improving the mechanical al-
loying process, including application
of modern process-modeling methods.
Several new processing methods are
applied to Fe-base alloys
[22]
and might
work with Ni alloys. Also, on a cost ba-
sis, ODS alloys compare more favorably
than CMCs.
Low ductility of ODS alloys
. ODS
alloys have low ductility, especially in
transverse directions
[23]
. They also suf-
fer from embrittlement due to prior
creep exposure
[24]
. However, experience
with low ductility materials has broad-
ened since the 1980s, and ductilities
of ODS alloys reported in earlier pub-
lications do not seem as intimidating
to engineers experienced with
γ
-TiAl
and CMCs, especially when combined
with fracture toughness values of about
40 MPa √ —m
[25]
. In addition, convention-
al superalloys also suffer from reduced
ductility after high temperature expo-
sure
[26]
, yet still perform well in service.
A reexamination of ductility is an essen-
tial part of a revitalized ODS develop-
ment program. However, incorporating
alternative tests to determine ductil-
ity, such as ballistic impact testing
[27]
,
would be more relevant to the intended
application.
Anisotropy in ODS alloys
. MA6000
has a predominantly [110] texture after
directional recrystallization, and TMO
alloys have textures ranging from [100]
to [111], depending on the alloy. This
raises a question of whether exception-
al creep properties in ODS alloys are a
result of their non-[001] orientations.
This appears to be unlikely, because
creepanisotropy at temperatures above
1000
o
C is generally not very significant.
The debit in thermal fatigue resistance
in non-[001] orientations
[28]
is also of
concern. This is a more serious issue
and must be addressed in future devel-
opment efforts. Two lines of thought
indicate a degree of optimism that the
issue can be resolved. First, it is known
that texture after recrystallization is a
function of alloy composition
[29]
, and
it is conceivable that a more desirable
texture can be achieved through alloy
and process development. Second, a
wafer-blade processing scheme allows
for reorienting wafers prior to bonding.
Fig. 3 —
Early ODS alloys show substantial improvements in creep capability over the best
single crystals, which is still true today, and without any refractory element additions
[18,19]
.