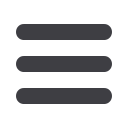
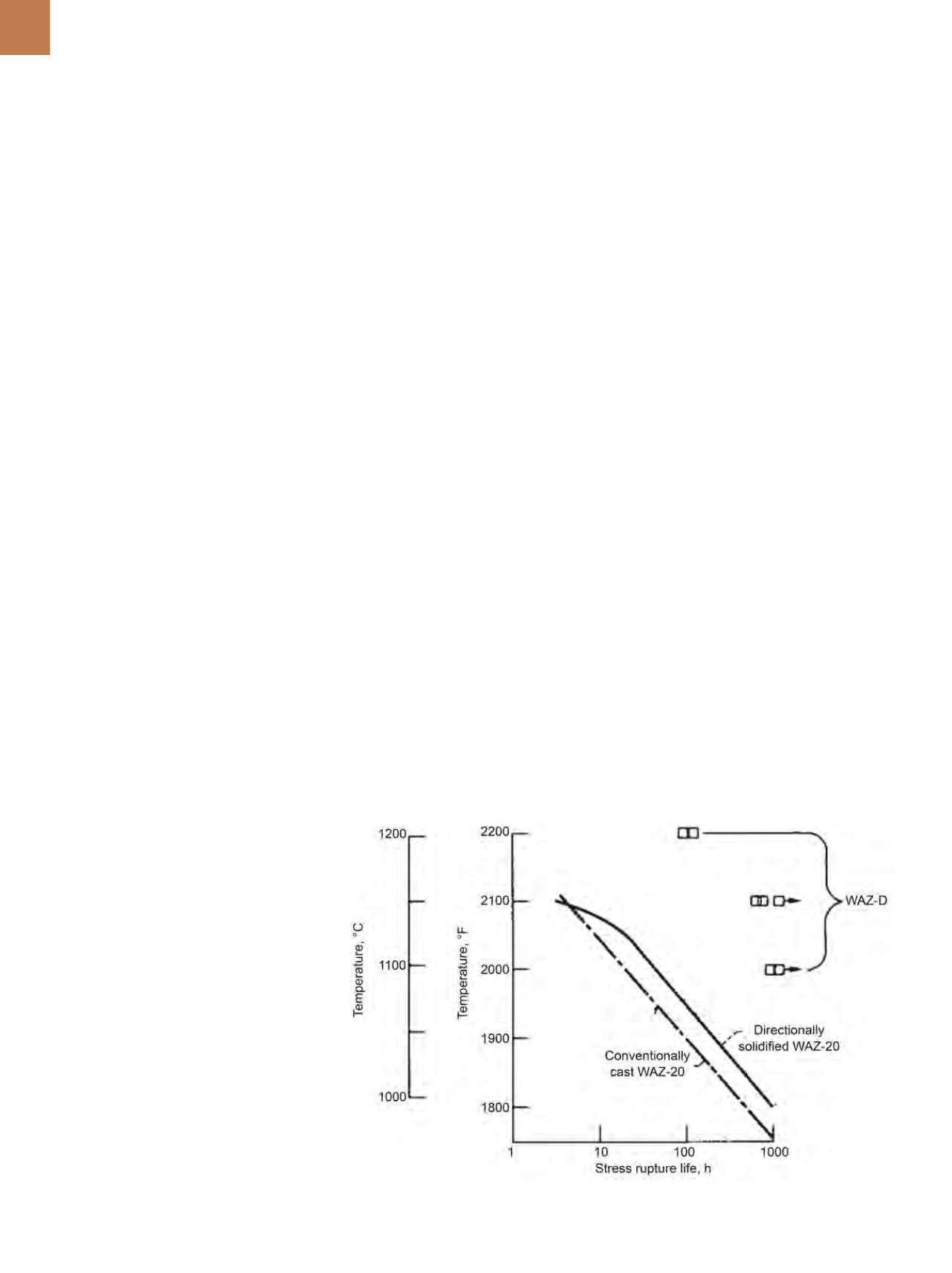
A D V A N C E D M A T E R I A L S & P R O C E S S E S | M A Y 2 0 1 5
2 2
levels for cracking and environmental
ingress, poor response to foreign object
impact events, and moisture-induced
recession effects in high combustion
pressures
[6]
, requiring reliance on envi-
ronmental barrier coatings on compo-
nent surfaces
[7]
. Thus, it is still prema-
ture to assume ubiquitous applications
of CMCs throughout an engine.
Significant resources were invest-
ed over the past 20 years on high-tem-
perature silicides as potential replace-
ments for superalloys. MoSi
2
-
[8]
, MoSiB-
[9]
and NbSi-
[10]
base alloys emerged from
screening numerous research results as
the most promising candidates, as they
improved strength, toughness, and ox-
idation resistance. However, no alloys
were developed with the balance of
properties required for a turbine blade,
especially for a high-pressure turbine. In
addition, many improvements in tough-
ness were achieved through compos-
iting strategies, which can be equally
applied to CMCs that have much lower
density than any other silicide. Thus,
there appears to be very little room for
silicides between superalloys and CMCs.
The recent discovery of
γ
-
γ
’
mi-
crostructures in Co-base alloys has
sparked interest
[11]
. Advantages include
higher melting points and improved so-
lidification behavior compared with Ni-
base alloys, and high toughness com-
pared with ceramics. However, their
high densities (exceeding 9 g/cm
3
), low
γ
’
solvus, and unknown oxidation re-
sistance remain formidable barriers to
their use. While it is too early to rule
out Co-base alloys as candidates for
high-pressure turbines, the alloy strat-
egy is yet unproven.
In this article, the case is made
for what appears to be “low-hanging
fruit” to replace single crystals as high-
pressure turbine blades—oxide disper-
sion strengthened (ODS) Ni-base alloys.
ODS alloys combine proven technology,
substantial gains in capability over to-
day’s alloys, and a clear development
path to overcome identified risks.
HISTORICAL BACKGROUND
Mechanically alloyed ODS super-
alloys were developed in the 1970s,
primarily by Inco Alloys. Both Fe- and
Ni-base alloys were developed and
commercialized, and are used in aircraft
gas-turbine engines and industrial tur-
bines
[12]
. Components include turbine
blades and vanes, nozzles, and com-
bustor/augmenter assemblies. Howev-
er, ODS alloys fell out of favor and have
not been actively pursued in the U.S. for
more than 20 years.
Mechanical alloying is used to pro-
duce a uniform distribution of submi-
cron oxide particles in a highly alloyed
matrix
[13]
. Alloys are formed from pure
elemental or pre-alloyed powders plus
about 2 vol% very fine (25 nm) yttria
(Y
2
O
3
). The powder mixture is milled in
high-energy ball mills to fully homoge-
nize the elemental additions, followed
by consolidation and hot working. Typ-
ically, ODS alloys are then directional-
ly recrystallized to form an elongated
grain structure. After milling and con-
solidation, Y
2
O
3
is converted to yttrium
aluminum garnet (YAG). FeCrAl-base
alloys MA956 and PM2000, NiCrAl-
base solid solution alloys MA754 and
PM1000, and
γ
’-strengthened MA6000
were the most widely used alloys.
Oxidation and hot corrosion resis-
tance of commercial ODS alloys range
from good to excellent
[14]
. In addition,
ODS alloy compositions are so similar
to those of superalloy single crystals
that compatibility with existing alu-
minide and overlay coatings
[15]
, as well
as TBCs, is expected to be excellent.
Solid-solution alloys have excellent
creep strengths at very high tempera-
tures, usually at or above 1100
o
C. How-
ever, creep strengths at intermediate
temperatures (750-850
o
C) are much
lower than
γ
’-strengthened alloys. MA
6000 was developed to compete with
single crystals as a turbine airfoil alloy,
and is strengthened by both oxides and
γ
’. It has significantly improved interme-
diate temperature creep strength with-
out sacrificing very high temperature
strength. Benn and coworkers devel-
oped more advanced alloys, known as
Alloys 51 and 92, that improved the in-
termediate temperature creep strength
of MA6000
[16]
.
Most importantly, two other stud-
ies show substantial improvements
in high-temperature creep strength.
Glasgow
[17]
showed that combining ODS
with
γ
’ strengthening produced an alloy
with more than 150
o
C increase in tem-
perature capability compared with the
same alloy with
γ
’ strengthening only
(Fig. 2). Kawasaki, et al.
[18,19]
, reported
exceptional creep properties for two
alloys, TMO-20 and TMO-16. Figure 3
shows that TMO-16 has a 100
o
C ad-
vantage over Rene N6 at 200 MPa. Al-
loy densities of ~8.9 g/cm
3
, calculated
using JMatPro
[20]
, are roughly equiva-
lent to third generation single-crystal
alloys. An important feature of these
Fig. 2 —
Benefits from combining
γ
’ and oxide strengthening. ODS alloy WAZ-D shows a creep
strength improvement of 130
o
C over WAZ-20, with essentially the same composition
[17]
.