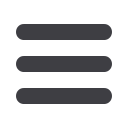
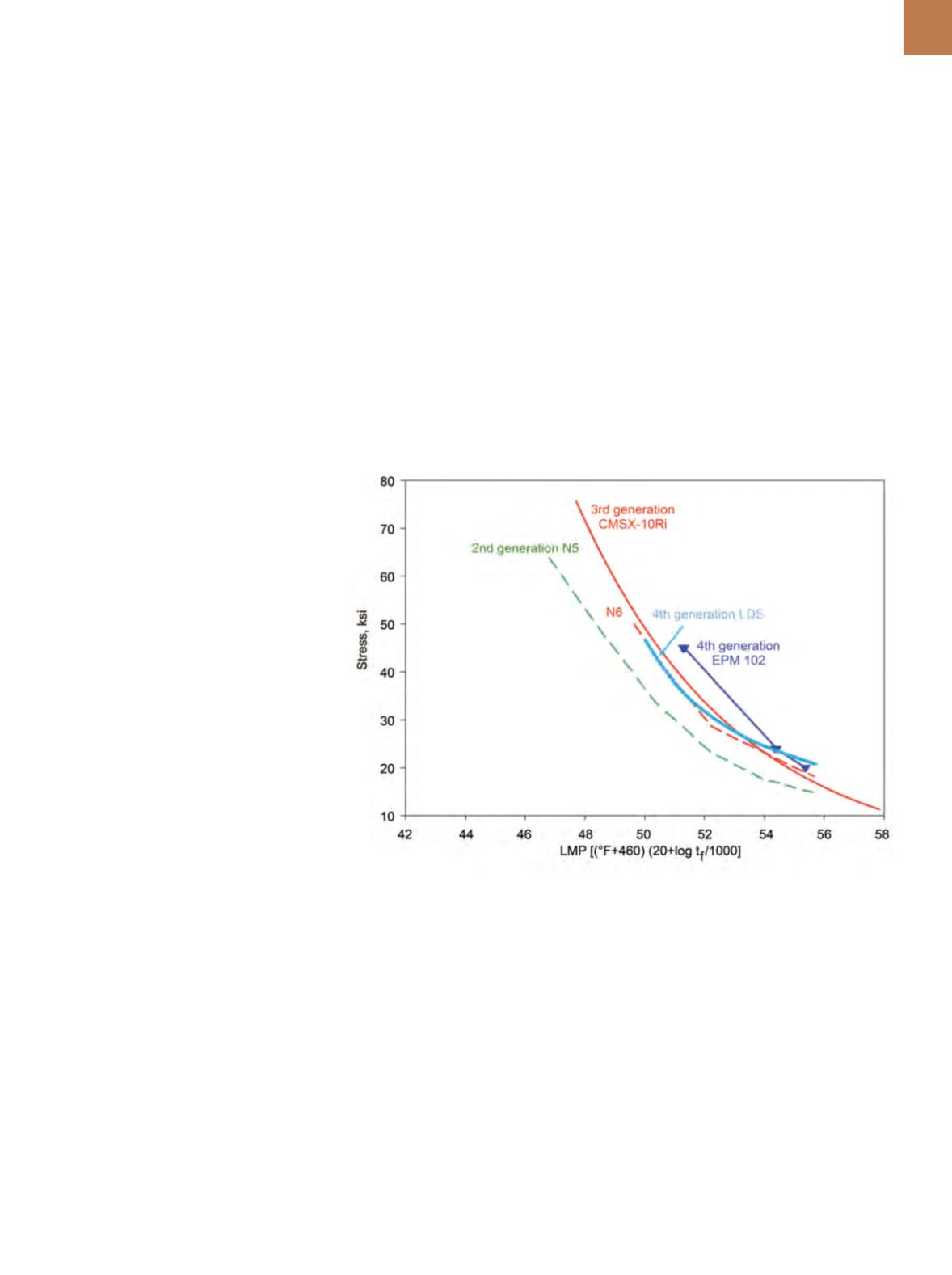
A D V A N C E D
M A T E R I A L S
&
P R O C E S S E S |
M A Y
2 0 1 5
2 1
ADVANCED TURBINE
AIRFOIL DEVELOPMENT
STRATEGIES: HARVESTING
LOW-HANGING FRUIT
Oxide dispersion strengthened alloys still have potential to improve turbine
blade temperature capability beyond that of superalloy single crystals.
Mike Nathal, NASA Glenn Research Center (retired), Cleveland
A
high-pressure turbine rotor is sub-
jected to the most demanding
conditions in the turbine engine,
which places stringent requirements on
the materials used. Turbine blades re-
quire a balance of creep resistance, high
temperature capability, environmental
resistance, and damage tolerance. To-
day’s blade performance and durability
are achieved through a combination of
advanced alloys, sophisticated internal
cooling schemes, and thermal barrier
coatings (TBCs). Turbine blades have
been made of nickel-base superalloy sin-
gle crystals for 30 years. Improvements
in alloy strength were achieved over the
years by increasing refractory element
(RE) content and reducing chromium
content, and the various alloys are cat-
egorized into about four generations of
development.
Successive generations of alloys
significantly increased creep strength
together with concurrent increases in
cost and alloy density and decreases in
microstructural stability and environ-
mental resistance (especially in the third
and fourth generations). Further, the
magnitude of improvement in creep re-
sistance with each succeeding genera-
tion diminished as shown in Fig. 1. Alloy
development in recent years has aimed
at reducing density
[1]
and Re levels
[2]
while maintaining current creep resis-
tance rather than increasing it.
Improvements in fuel efficiency
and exhaust emissions expected from
next-generation turbine engines require
further increases in hot sectionmaterials
capability. There is no obvious materials
development strategy available to pro-
duce further improvements in tempera-
ture capability without upsetting the
balance of properties achieved in sin-
gle-crystal superalloys. Higher reliance
on TBCs is a possible strategy, although
the consequences of coating spallation
are still quite serious. One means of mit-
igating the risk of coating spallation is to
incorporate self-indicating features into
the coating system, whereby dopants at
different depths within the topcoat lay-
er have varying luminescence and thus
enable easy inspection for erosion or
spallation
[3]
.
Ceramic-matrix composites (CMCs)
remain the prime candidates to replace
superalloys for ultimate gains in per-
formance, especially at temperatures
above about 1200
o
C. SiC/SiC composites
exhibit substantial improvements inme-
chanical performance
[4]
, and manufac-
turing technology has matured substan-
tially
[5]
. However, risks associated with
CMCs include relatively low strength
Fig. 1 —
Larson-Miller curves for single-crystal superalloys. Improvements in creep strength of
succeeding generations of alloys have diminished.