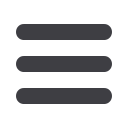
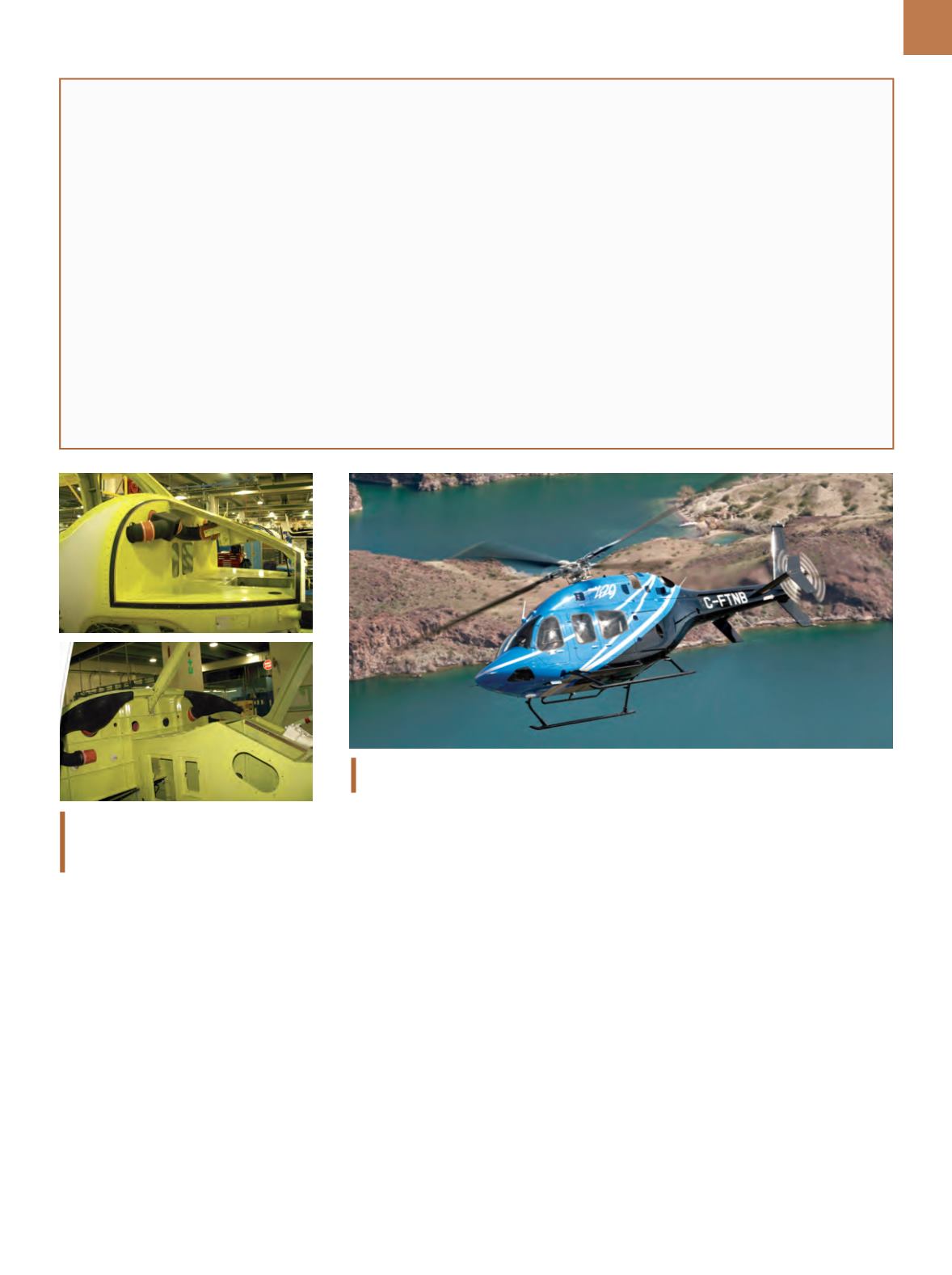
A D V A N C E D
M A T E R I A L S
&
P R O C E S S E S |
M A Y
2 0 1 5
1 9
B
ell Helicopter and Harvest selected the EOSINT P 730
for manufacturing aircraft parts after careful study and
testing, focusing on the intertwined technical and financial
benefits. In addition to increased nestability, the larger EOS
build platform provides a number of benefits. For example,
building bigger components in one piece rather than in sec-
tions enables a stronger andmore lightweight part, and also
eliminates some assembly operations.
Another advantage of the EOS system is the clean sur-
face it produces. Some competing AM technologies produce
satisfactory parts, but peripheral heat from the laser beam
melts adjacent powder resulting in unwanted particle adhe-
sion and the need for additional post-processing to polish
the surfaces.
“We were able to achieve the desired quality with the
other additive system,” says Ron Clemons,
director of busi-
ness development at Harvest,
“but there was a lot more fin-
ishing labor associated with it than on the EOS platform.”
The P 730 incorporates a software fix for laser sintering
that provides crisper detail and smoother surfaces.
Switch-
ing to the EOS system offered significant post-processing
cost savings and shorter lead times for Bell Helicopter.
An important secondary benefit of EOS laser-sintering
technology is increased recyclability of the plastic powder.
With other AM processes, breaking out the part from the bed
of powder leaves behind a significant amount of unusable par-
tially melted powder, which must be discarded, so the bulk of
production is performed with virgin powder. The reduction of
waste in the P 730 enables recycling of leftover powder.
Parts of the environmental control system of the Bell 429 commercial helicopter were pro-
duced using EOS laser-sintering technology.
Laser-sintered ductwork installed in a
helicopter airframe. Images on this page
courtesy of Bell Helicopter Textron Inc.
MAKING AIRCRAFT PARTS ON THE EOSINT P 730
mechanical integrity, unique serial IDs
for each part, andmaterial certification.
A preproduction sample is sent to
Bell Helicopter for examination to ensure
that it is functional, fits accurately with
other components, meets engineering
specifications, and that Harvest’s inspec-
tion procedure is correct and complete.
“We have full confidence in Harvest
and their quality assurance program,”
says Schulte. “Once their QA is com-
plete, when warranted, we go to some
lengths ourselves to make sure that the
design intent is also met. We continue
to work with Harvest to streamline pro-
duction and take advantage of additive
manufacturing technology maturation.”
Only when this final scrutiny is complete
does Harvest ship the rest of the pro-
duction batch to Bell Helicopter.
LOOKING AHEAD
Bell Helicopter continues to pro-
pose innovative designs in the form
of CAD models that Harvest turns into
physical parts. In fact, Bell is interested
in using laser-sintered parts throughout
the aircraft systems of its commercial
helicopters. Currently, the company is
mostly using laser-sintered components
in the ECS system, but is starting to in-
corporate laser-sintered hardware into
other assemblies. It will also evaluate
laser sintering of high-temperature
plastics intended for use in more de-
manding roles and environments.
AM is transforming more than the
designs at Bell Helicopter. Engineers are
taking advantage of the freedom that
comes with applying EOS technology,
creating small components, working
with larger ones than in the past, and
using the part-integrating capability of
laser sintering to eliminate assembly
costs.
~AM&P
For more information:
Jessica Neh-
ro is field marketing manager, EOS of
North America Inc., 28970 Cabot Dr.,
Suite 700, Novi, MI 48377, 248.306.0143
ext. 8104,
jessica.nehro@eos-na.com,
www.eos-na.com.