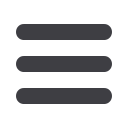
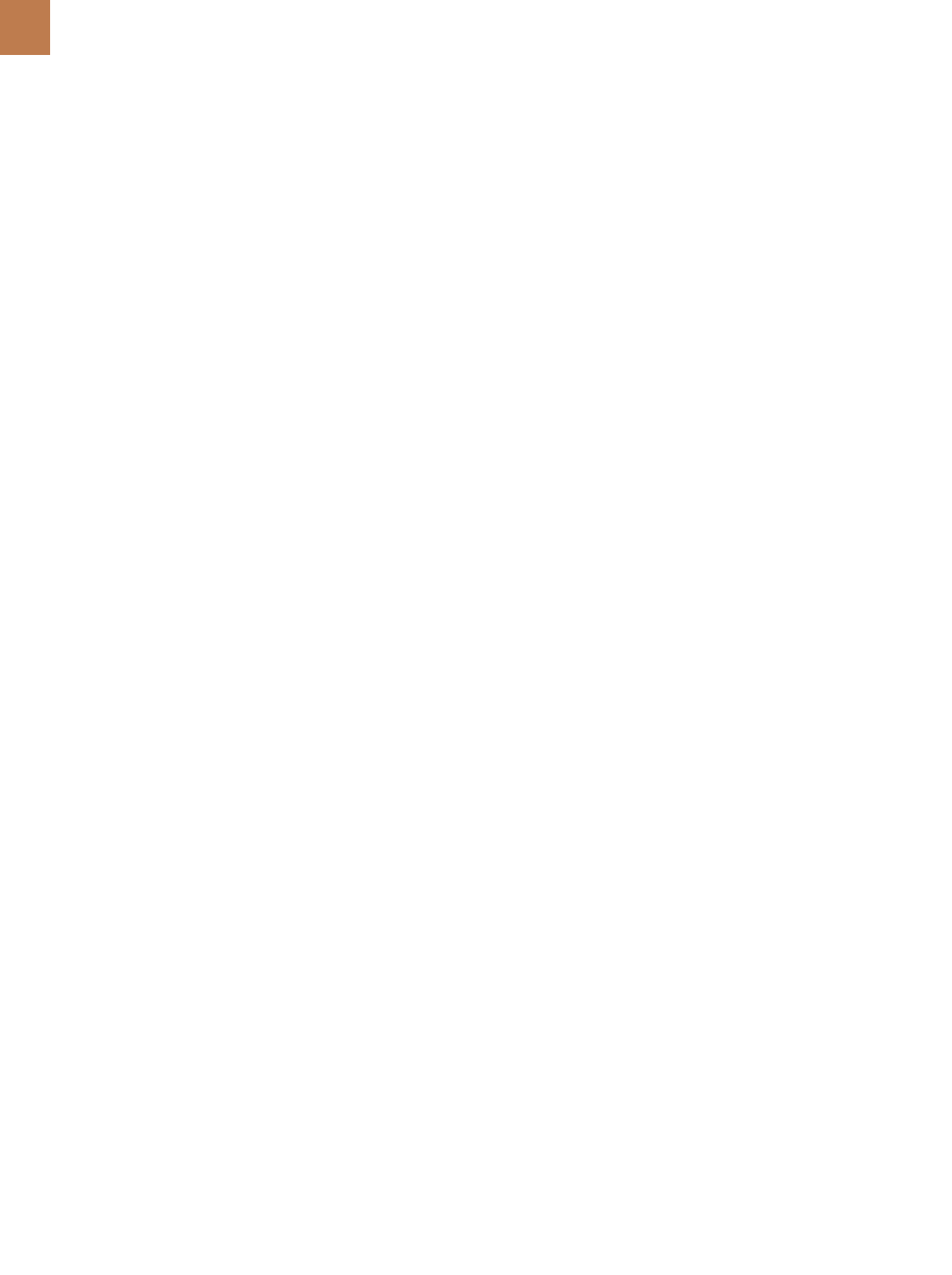
A D V A N C E D M A T E R I A L S & P R O C E S S E S | M A Y 2 0 1 5
2 4
Transverse properties of ODS al-
loys
. In addition to lower ductility, men-
tioned previously, the creep strength of
ODS alloys is noticeably weak in trans-
verse directions. It is not clear how se-
rious this issue is, as many successful
ground engine tests of ODS alloys
[30]
and directionally solidified eutectics
(also with large creep anisotropy) were
accomplished in the past. If transverse
properties are a serious issue, one route
for mitigation could be improved un-
derstanding of recrystallization meth-
ods. The ability to control recrystalli-
zation to produce single crystals
[31]
in
wafers, for example, would eliminate
the transverse-property debit. The en-
tire topic of recrystallization would be
an excellent focus for future integrated
computational materials engineering
(ICME) study. Models to predict recrys-
tallization response as a function of
alloy composition, oxide dispersion pa-
rameters, and thermomechanical pro-
cessing history would accelerate ODS
alloy development.
Inspection limits
. An unpublished
reason for the lack of success for
MA6000 as a turbine blade material is
its sensitivity to small unrecrystallized
regions that could serve as sites for pre-
mature failure. These regions could not
be reliably detected by nondestructive
inspection methods. Future work must
revisit this issue and quantify its ef-
fect. Adopting a wafer-blade processing
scheme should enable easier inspec-
tion of wafers prior to bonding.
SUMMARY
The case for reemphasizing ODS
alloys to improve turbine blade tem-
perature capability beyond that of
superalloy single crystals appears to
be quite strong. Experimental alloys
already exist that exceed the best sin-
gle crystals, and further improvements
are possible through updated alloy de-
sign. Exceptional creep properties were
achieved without relying on expensive,
strategic elements such as rhenium.
Compared with ceramics, interme-
tallics, and cobalt alloys, the risks are
modest and the payoffs significant. In
contrasttothesealternatives,technology
solutions either already exist or have
been identified to achieve the bal-
ance of properties required for a high-
pressure turbine blade including cost,
strength, toughness, impact resistance,
oxidation and corrosion resistance, TBC
compatibility, and manufacturability.
A program directed at develop-
ing ODS alloys for use in turbine blade
applications is recommended. In ad-
dition to alloy development, concerns
that must be addressed in future de-
velopment efforts include ductility,
thermomechanical fatigue, and pro-
cessability. Use of modern modeling
and design tools could accelerate mat-
uration of this promising technology.
~AM&P
For more information:
Mike Nathal
(retired) was chief of the Advanced Me-
tallics Branch, Structures and Materials
Division, NASA Glenn Research Center,
miken345@wowway.com,
www.etsy.com/ shop/MikesCoolWoodArt.Acknowledgment
The author thanks Tom Glasgow
and Ray Benn for helpful discussions.
References
1. R.A. MacKay, et al.,
JOM
, p 48, Jan.
2010.
2. L.J. Carroll and K.S. O’Hara, U.S. Pat-
ent 20,110,120,597 A1, 2011.
3. J.I. Eldridge, et al.,
J. Am. Ceram. Soc.,
Vol 89, (10), p 3246-3251, 2006.
4. Handbook of Ceramic Composites,
N. Bansal, Ed., Kluwer Academic Pub-
lishers, Boston, 2005.
5. M. Mecham, Out of the Lab,
Aviation
Week,
p 13, July 2012.
6. J.L. Smialek, et al.,
Adv. Composite
Mater.,
Vol 8, No. 1, p 33-45, 1999.
7. K.N. Lee, et al.,
J. Eur. Ceram. Soc.,
Vol 25, No. 10, p 1705-1715, 2005.
8. M.G. Hebsur, et al., Structural Inter-
metallics, K.J. Hemker, et al., Eds., TMS,
Warrendale, PA, p 745-753, 2001.
9. J.H. Perepezko, et al., Structural Inter-
metallics, K.J. Hemker, et al., Eds., TMS,
Warrendale, PA, p 505, 2001.
10. S.J. Balsone, et al., Structural Inter-
metallics, K.J. Hemker, et al., Eds., TMS,
Warrendale, PA, p 50, 2001.
11. T.M. Pollock, et al.,
JOM,
Vol 62,
p 58-63, Jan. 2010.
12. J.J. deBarbadillo and J.J. Fisher,
Properties and Selection: Nonferrous Al-
loys and Special-Purpose Materials, ASM
Handbook Online, Vol 2, p 2-8, 2000.
13. S.H. Kang and R.C. Benn,
Met. Trans.
,
A16, p 1285, 1985.
14. V. Guttmann, et al., Oxidation of
Metals, Vol 51, p 159, 1999.
15. R.C. Benn, et al., Proc. High Temp.
Coatings Symp. (M. Khobaib and R.
Krutenat, Eds.), TMS-AIME, p 119, 1988.
16. R.C. Benn, Superalloys, (J.K. Tien, et
al., Eds.), ASM International, Materials
Park, OH, p 541-550, 1980.
17. T.K. Glasgow, Proc. 3rd Intl. Symp. on
Superalloys, B.H. Kear, et al., Eds., Clai-
tor’s Publishing, p 385-394, 1976.
18. Y. Kawasaki, et al.,
High Temperature
Materials for Power Engineering, Part II
,
E. Bachelet, et al., Eds., p 1443, 1990.
19. M. Yamazaki, et al.,
Structural Appli-
cations of Mechanical Alloying
, F.H. Froes
and J.J. deBarbadillo, Eds., ASM Interna-
tional, Materials Park, OH, p 33, 1990.
20. N. Saunders, et al.,
JOM
, Vol 55,
No. 12, p 60, 2003.
21. W.G. Hess, U.S. Patent 4,203,706 A,
1980.
22. G.R. Odette and D.T. Hoelzer,
JOM
,
p 84, Sept. 2010.
23. J.D. Whittenberger,
Metall. Trans. A
,
Vol 8A, p 1155, 1977.
24. J.D. Whittenberger,
Metall. Trans. A
,
Vol 8A, p 1863, 1977.
25. Y. Lino,
Mat. Sci. Eng. A
, Vol A 234-236,
p 802, 1997.
26. W.H. Chang,
Proc. 2nd Intl. Conf. on
Superalloys
, National Technical Informa-
tion Service, Springfield, VA, V-1, 1972.
27. S.L. Draper, et al.,
Met. Trans. A
,
Vol 32 A, p 2743, 2001.
28. B.H. Kear and B.J. Piearcey,
Trans.
Metall. Soc. AIME
, Vol 239, p 1209, 1967.
29. H.A. Chin and A.M. Adair,
Proc. 5th
Intl. Symp. on Superalloys
, M. Gell, et al.,
Eds., TMS, Warrendale, PA, p 335, 1984.
30. R.L. Dreshfield, et al.,
Frontiers of
High Temperature Materials II
, J.S. Benja-
min and R.C. Benn, Eds., London, p 235,
1983.
31. R.C. Benn, U.S. Patent 4,961,818,
1990.