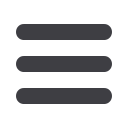

A D V A N C E D
M A T E R I A L S
&
P R O C E S S E S |
M A Y
2 0 1 5
2 9
in metal production for a brief time and
then left the field. Cramet Inc., jointly
owned by Crane Co. and Republic Steel
Corp., ceased operation and Republic
stopped producing titaniummetal prod-
ucts. DowChemical first put their sponge
plant on standby, then closed it shortly
after. Union Carbide reduced sponge
production to 25% of capacity and later
closed. Mallory-Sharon Titanium Corp.
sold a one-third interest to National Dis-
tillers, a new sponge producer. Within a
few years, both P.R. Mallory and Sharon
Steel sold their interests to National Dis-
tillers, who renamed the operation Reac-
tive Metals. Even DuPont, the first com-
pany to enter sponge production, closed
their plant in 1962. Witnesses to this
situation believed that the DoD Sheet
Rolling Program was a major factor in
holding together what remained of the
industry. One new producer was build-
ing a plant in Albany, Ore., called Oregon
Metallurgical Corp. They would struggle
through this period, but remained in the
titanium business.
Titanium metal shipments would
not exceed those of 1957 (5600 tons)
until 1962 (6500 tons). During this time,
the remaining producers were pressed
to find other applications. One new,
all-titanium military plane from the
1960s was the SR-71 Blackbird, built to
replace a spy plane that was shot down
over Russia. The reduced jet engine
market was still the major customer,
but slowly applications were found in
chemical and nuclear plant construc-
tion where corrosion resistance was the
main property required. In addition, the
growing missile technology field began
to consume higher amounts of titani-
um, as did the civilian airline industry
with the introduction of jet-powered
aircraft. These planes included the
Boeing 707 and Douglas DC-8, in addi-
tion to later models such as the Boeing
727 and 737, and the DC-9. All of these
planes featured a few percent of the air-
frame weight in titanium as well as sub-
stantial weight in the engines.
AIRFRAMES AND ENGINES
Jet engine builders were the major
consumers of titanium and Pratt & Whit-
ney was the first to embrace this metal in
their military jets from the early 1950s.
Later, when commercial jet engines be-
came popular in the 1960s and beyond,
they continued to expand titanium use.
Eli Bradley was chief materials engineer
at Pratt during this crucial period of com-
mercial jet engine development. For 20
years, hewas a leading expert in titanium
applications in the jet engine industry.
Bradley received the ASM Engineering
Achievement Award in 1975, and the ASM
Gold Medal in 2002—the same award
that was given to WilliamKroll in 1967.
Introduction of wide-bodied air
transport planes in the late 1960s im-
proved the markets for titanium. A
number of factors coincided to increase
titanium use to nearly 30,000 tons, the
amount forecast in the early 1950s. Ci-
vilian transport aircraft construction
and chemical and nuclear uses reached
peak levels and an export business had
developed to serve the growing mil-
itary and civilian aircraft production
in Europe. This peak usage would not
be repeated for many years due to the
rapid decline in all of these markets in
1982-83. The one bright spot was the
100 all-titanium, Mach 3, B-1 bombers
built by North American Rockwell.
The most recent commercial air-
craft designs use substantial amounts
of titanium, according to Rodney R. Boy-
er, a technical fellow at Boeing Materi-
als Technology, Commercial Airplane
Group. The Boeing 777 uses 13,000 lb
of Ti-10V-2FE-3Al in the landing gear of
each plane. This is a beta alloy that is
heat treated to 160,000 to 170,000 psi.
The Air Force F-22 uses approx-
imately 42% (9000 lb) of titanium al-
loys in the airframe: Although several
alloys are now available, the largest
amount is still Ti-6Al-4V. The Pratt &
Whitney engines for this plane contain
both Ti-6Al-4V and the newer alloy,
Ti-6Al-2Sn-4Zr-2Mo-0.2Si.
The original enthusiasts, individu-
als, companies, government agencies,
universities, and research laboratories
believed in a great future for a strong,
lightweight, heat-resistant, corrosion-
resistant metal. Their dream came to
pass after a decade of difficult R&D and
an investment of several hundredmillion
dollars by the government and industry.
The cost of producing titanium, howev-
er, has limited its major applications to
jet engine and airframe construction. Ti-
tanium has fulfilled its promise as a new
metal for the aerospace age.
For more information:
Charles R.
Simcoe can be reached at
crsimcoe1@ gmail.com.
The transition frommanned aircraft to
missiles in 1957 cut the B-52 Bomber
program from 17 wings to 11. Many other
aircraft were canceled entirely.
The B-1 Bomber was built to withstand
speeds of 2000 mph. The heat generated
required titanium alloys, mainly Ti-6Al-4V.
The Lockheed SR-71 Blackbird, built in
the 1960s, was the first plane with all-tita-
nium construction.
The Boeing 777 is the first commercial
plane to use a titanium alloy (Ti-10V-2Fe-
3Al) for landing gear. Courtesy of Altair78/
Wikimedia Commons images.