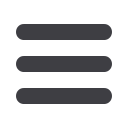
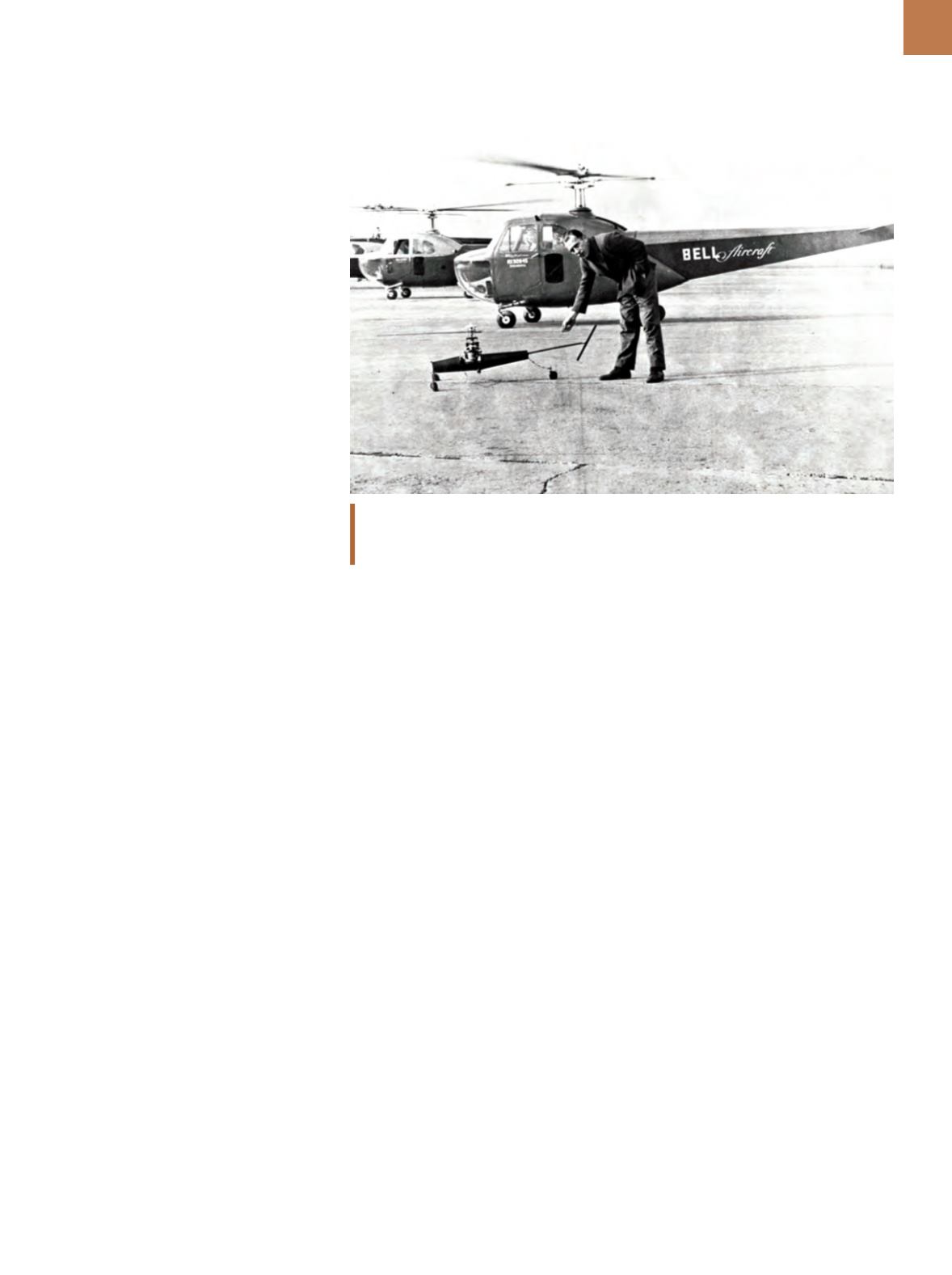
A D V A N C E D
M A T E R I A L S
&
P R O C E S S E S |
M A Y
2 0 1 5
1 7
I
n 1941, Arthur M. Young demonstrated
an ingeniously engineered model heli-
copter flying on a tether while working
for Bell Aircraft Corp. Five years later, the
company received the first-ever certifica-
tion for a commercial helicopter. Today,
Bell Helicopter Textron Inc., Fort Worth,
Texas, has manufactured more than
35,000 helicopters. Bell Helicopter works
with Harvest Technologies, Belton, Texas,
an additive manufacturing (AM) services
provider with more than 40 AM systems,
many of them used to create end-use
components and assemblies.
Collaboration between Bell and
Harvest proves that AM is a high quali-
ty, repeatable, and cost-effective man-
ufacturing process, in this case with
plastic laser-sintering technology from
EOS GmbH Electro Optical Systems,
Germany.
LASER SINTERING PRODUCES
3D-PRINTED PARTS
For years, Bell Helicopter and
Harvest have partnered to produce
flight-certified hardware on a standard
laser-sintering platform. Bell believed it
could achieve success with laser sinter-
ing due to its extensive experience qual-
ifying both products and manufacturing
processes, while Harvest has the neces-
sary expertise in AM.
Harvest purchasedanEOSINTP730
plastic laser-sintering system in 2011.
The system features twin 50-W lasers
working in tandem over an expansive
build area—a first for laser-sintering
technology—to achieve a layer-by-layer
build speed of 35 mm (1.38 in.) per hour
of height. The platform offers several
advantages for qualifying this machine
for end-use parts production.
“The parts we get from the P 730
have very good feature definition, and
the powder color is consistently less ox-
idized,” says Harvest quality manager
Caleb Ferrell. “Mechanical properties
are also good. We’re especially happy
with the larger platform size and the
nestability aspect.”
The ample platform size and nesta-
bility contribute to reducing per-unit
cost. The build platformmeasures 700
×
380
×
580 mm (27.5
×
15
×
23 in.), larger
than Harvest’s standard laser-sintering
systems. The increased size enables pro-
duction of more components in a batch
and far more than traditional laser-
sintering platforms, especially when
careful nesting practices are used. Nest-
ing also achieves more cost effective,
low volume production.
For example, Bell Helicopter and
Harvest converted a number of aircraft
parts made using other manufacturing
processes to laser sintering. “A precon-
ception is that additive manufacturing
is more costly compared with alternate
manufacturing methods, with design
flexibility being the premium feature,
but we often discover that production
cost per piece is substantially reduced
using the P 730,” says Elliott Schulte,
Bell Helicopter engineer. (See sidebar.)
VERIFICATION PROCESS
Before production could begin,
Bell Helicopter and Harvest needed to
prove out the P 730 and its processing
capabilities to certify the platform for
use. While the new technological ad-
vances included in the system along
with the sheer platform size provide
greater efficiencies, the companies
needed to ensure this was not at the
cost of part integrity.
The dual laser system and subse-
quent “knit line” presented new consid-
erations to analyze and evaluate. Veri-
fying a new platform meant not only
addressing these factors, but also ex-
amining other common issues such as
heat distribution (part bed temperature
consistency), powder degradation, di-
mensional accuracy, repeatability, part
quality, part performance, and overall
economics of the platform.
Bell Helicopter initially
character-
ized a variety of laser-sinterable Nylon
11s and 12s, for which materials and
manufacturing methods were covered
by company-authored specifications.
The resulting materials characteriza-
tion and properties database ensured
that the P 730 machine qualification
(both system and process) was accom-
plished quickly.
Mechanical properties of each
laser-sintered build were characterized
to confirm that the EOS system met
specification requirements and pro-
duced the same product quality each
time. A number of different material
lots and a series of individual builds
were tested to establish that laser sin-
tering was robust and highly repeatable
for producing identical results.
From concept to reality, Arthur Young poses with his final research model, alongside the
commercially certified Bell Model 47B helicopter. Courtesy of Bell Helicopter Textron Inc.,
circa 1947.