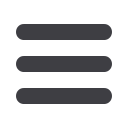
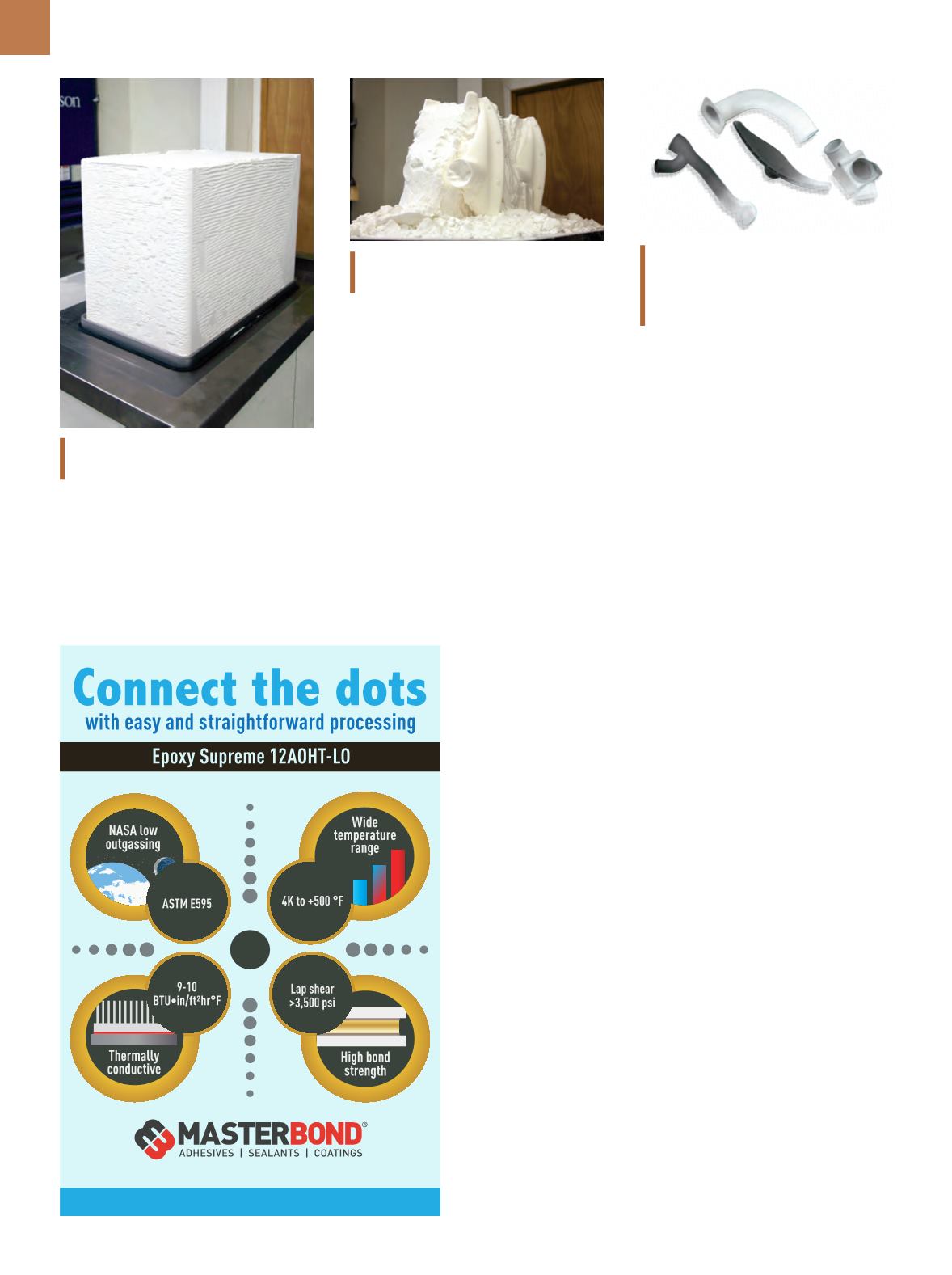
A D V A N C E D M A T E R I A L S & P R O C E S S E S | M A Y 2 0 1 5
1 8
Gravelle, leader of Bell Helicopter’s rapid
prototyping lab. For example, it might
not be possible to use the exact config-
uration of bosses made of laser-sintered
nylon for attachment points as those
used for a metal part. Many designs are
treated as a mostly “clean slate,” be-
cause laser sintering provides a great
deal of flexibility and freedom.
After final review of the design for
system producibility, a 3D CAD mod-
el is sent to Harvest with a request for
quote for development of a build strat-
egy. Some questions include: Is the part
large enough to manufacture on its
side, speeding up the build? Should it
be made (or grown) standing vertically
to take advantage of tighter uniformi-
ty and accuracy on the
x
-
y
axis? How
nestable is it, and how many units can
be made in a single build? Answering
these and other questions enables sub-
mitting an accurate pricing quotation.
When production begins, before
each batch, a rigorous checklist of pre-
production inspections (for example, a
nitrogen leak rate check) developed by
Harvest is carried out, which reduces
waste and ensures part quality. The list
is developed specifically for the P 730
based on previous production runs.
Batches of laser-sintered parts
built successively (often left unattend-
ed overnight) are thoroughly inspected
and tested for tensile and flexural prop-
erties. This requirement was estab-
lished by Harvest for process assurance.
Tensile bars are incorporated along the
x
,
y
, and
z
axes of each batch during part
production. If the bars pass the tensile
test, parts built in that batch pass as
well. Harvest also documents manufac-
turing from beginning to end, including
After laser sintering, completed parts
require “breaking out” from the powder.
Excess powder is removed and much of
it reused for subsequent builds.
Plastic laser sintering is capable of creat-
ing complex shapes such as ductwork.
Images on this page courtesy of Harvest
Technologies.
periodically reviewing Harvest’s QA
system with respect to AS 9100C—the
SAE quality management standard for
aerospace. After qualifying the AM sys-
tem and nylon materials, Bell Helicop-
ter and Harvest began the meticulous
sequence of manufacturing aerospace
hardware, which involves many checks
and confirmations along the way.
PARTS PRODUCTION
Consider a hypothetical example
of Bell Helicopter wanting to incorpo-
rate a new piece of ductwork into the
environmental control system (ECS) of a
commercial helicopter.
The engineering team
would use the data-
base created to qualify
the P 730 to design a
duct based on specified
mechanical properties.
The part could differ
from an earlier design
by merging several
components into one
(part consolidation), or
by creating its form for
maximum functionality
rather than manufac-
turing demands such as
draft angle for molding,
wall thickness limita-
tions due tomaterial in-
put, or rounded corners
for CNC machining. The
final design must meet
the same performance
specifications.
It is possible that
the redesigned part
could have a different
shape and features, ac-
cording to Christopher
Hackensack, NJ 07601, USA +1.201.343.8983 main masterbond.com www.masterbond.comBell Helicopter also followed its
standard procedure used to audit sup-
pliers, which not only ensures con-
formance to its process specification,
but also serves as a quality audit by