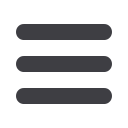
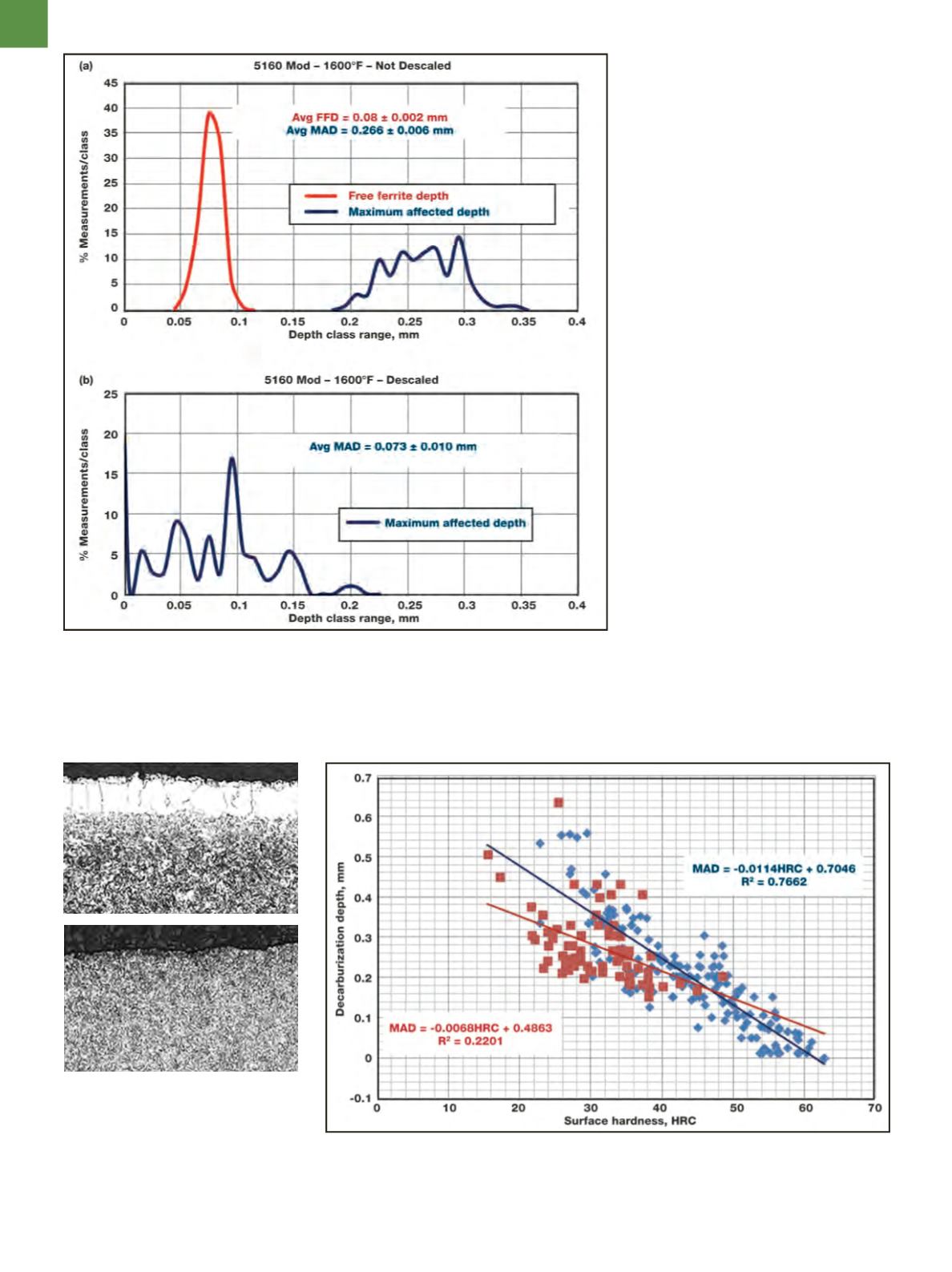
SiC abrasive paper can be used for grind-
ing, resin-bonded diamond discs such as
MD-Piano provide excellent flatness and
long life. Napless cloths are used for di-
amond polishing while low-nap clothes
are used to polish with alumina or colloi-
dal silica abrasives. In most cases, a ret-
icule is used to make the measurement.
Alternatively, many image-capture soft-
ware programs allow operators to make
point-to-point distance measurements.
However, these systems must be proper-
ly calibrated.
Hot working temperatures can
produce ferrite at the surface with the
amount and size of the ferrite grains
growing as carbon loss increases at the
surface. The upper critical tempera-
ture, Ac
3
, of these grains could be above
1600°F, as alloy composition and residu-
al elements influence the Ac
3
of the steel
grade. Spring steels are used as an ex-
ample. If a decarburized specimen is in-
duction hardened, the heating rate to the
austenitization temperature is extremely
fast. To put all of the carbon in solution
(assuming that the steel has a carbon
content of 0.60-0.65%), it is heated to
roughly 1700°-1750°F. As the holding
time is short, perhaps no more than 10 s,
there is little time for appreciable carbon
diffusion and the decarburization depth
after heat treatment is a function of the
as-rolledmill decarburization depth.
Fig. 4
— Frequency histograms of decarburization measurements made around the periphery
of 5160 modified bars after heat treatment. a) 1600°F specimen with a mill scaled surface has an
average FFD of 0.08 mm and average MAD of 0.266 mm for 132 measurements. Note the narrow,
peaked distribution of the FFDmeasurements and broad distribution of MADmeasurements.
b) 1600°F specimen with a descaled surface does not exhibit any free ferrite. No decarburization
was observed for almost 19.5% of the measurements and distribution of MAD values is broad.
Fig. 5
—Decarburized surfaces of 5160
Mod austenitized at 1600°F for 80 min.
and oil quenched. Free ferrite on the
scale covered specimen, top. No free
ferrite present on the specimen that was
descaled before being austenitized (2%
nital, 200×), bottom.
Fig. 6
—Rockwell C hardness tests on the surface of 5160H, 5160M, and 9260M (after glass bead
blasting) is a simple screening test to determine if the surface is decarburized or free of
decarburization. The correlation is much better when there are no free-ferrite grains at the surface
(blue data points) than when free ferrite (red data points) is present.
A D V A N C E D M A T E R I A L S & P R O C E S S E S | F E B R U A R Y 2 0 1 5
2 4