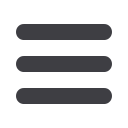
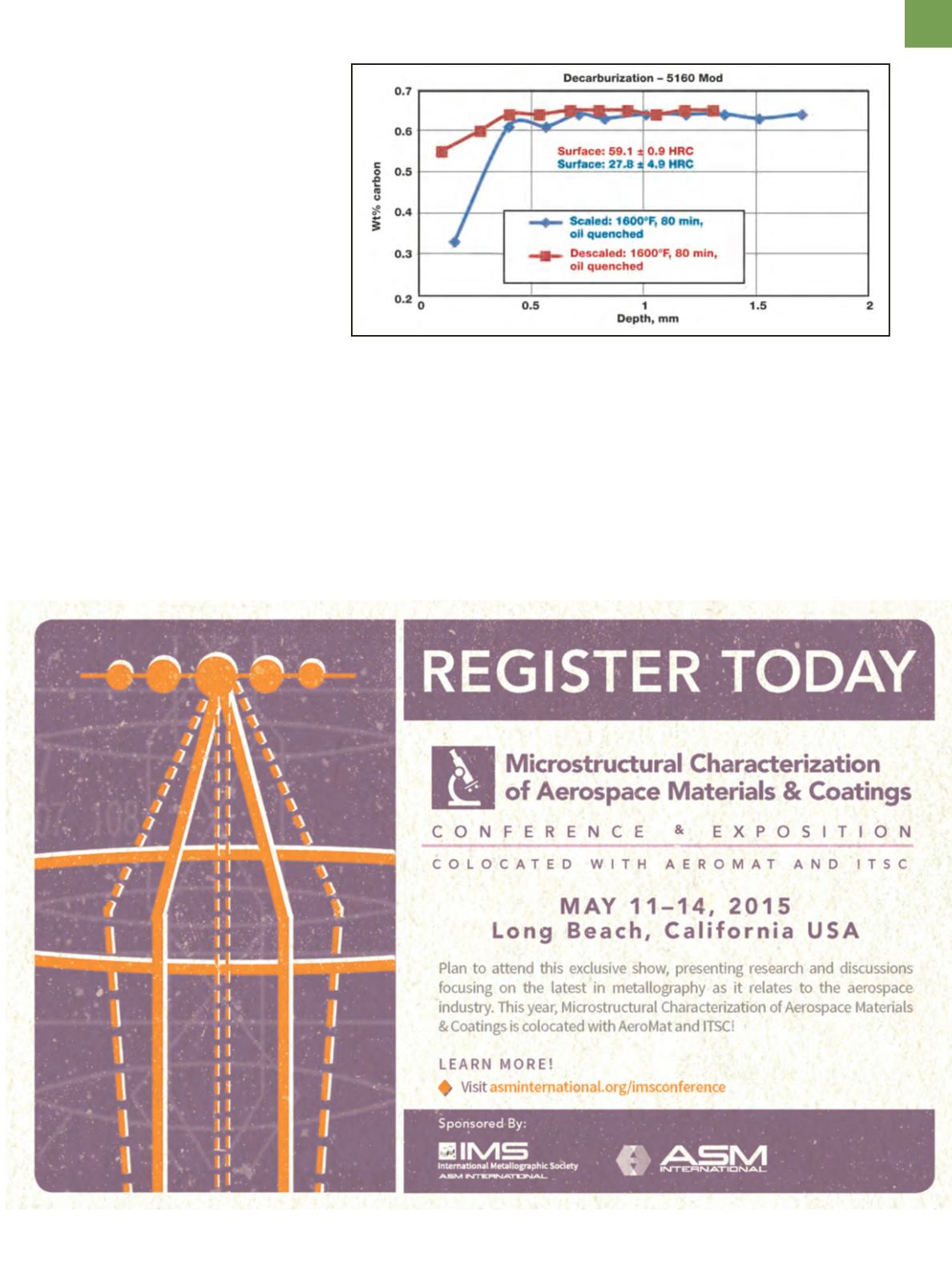
not present). If free ferrite is present,
the free-ferrite layer’s maximum depth
(often variable) plus the depth of partial
decarburization to the unaffected core
is measured. This total—FFD + PDD—is
called maximum affected depth (MAD).
These depths are not uniform and can
vary substantially, leading to measure-
ments of average FFD, PDD, and MAD,
as well as maximum values for each.
ASTM E1077 covers decarburization
measurement.
In practice, decarburization should
be evaluated on a plane transverse to the
hot working axis, as depth variation is
greater around the bar on the transverse
plane than at a specific constant position
along a longitudinal plane. Decarburiza-
tion depth can vary substantially around
the periphery of a bar, as shown in Fig. 1.
Qualitative measurements can be sub-
jective and biased. Free-ferrite depth
can also be erratic, even over a small sur-
face area, as shown in Fig. 2. Corners of
square or rectangular sections normally
exhibit greater decarburization depths
than planar surfaces. Sampling schemes
for large cross-sections are also illustrat-
ed in ASTM E1077.
To obtain good data, edge reten-
tion must be perfect—the surface must
be perfectly flat to the extreme edge. If
edges are rounded, the exact location
of the outer surface is difficult to define
with precision and depth measurement
accuracy suffers. Good edge retention
requires mounting of the specimen in a
resin, such as DuroFast, that does not ex-
hibit shrinkage gaps between the mount
and specimen after polymerization.
Grinding and polishing procedures must
emphasize maintaining flatness. While
Fig. 3
—Decarburization of 5160 modified spring steel defined by surface hardness and
incremental turnings analyzed chemically for carbon content as a function of whether or not the
surface was descaled or was covered by mill scale, and austenitizing at 1600°F for 80 minutes.
A D V A N C E D
M A T E R I A L S
&
P R O C E S S E S | F E B R U A R Y
2 0 1 5
2 3