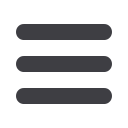
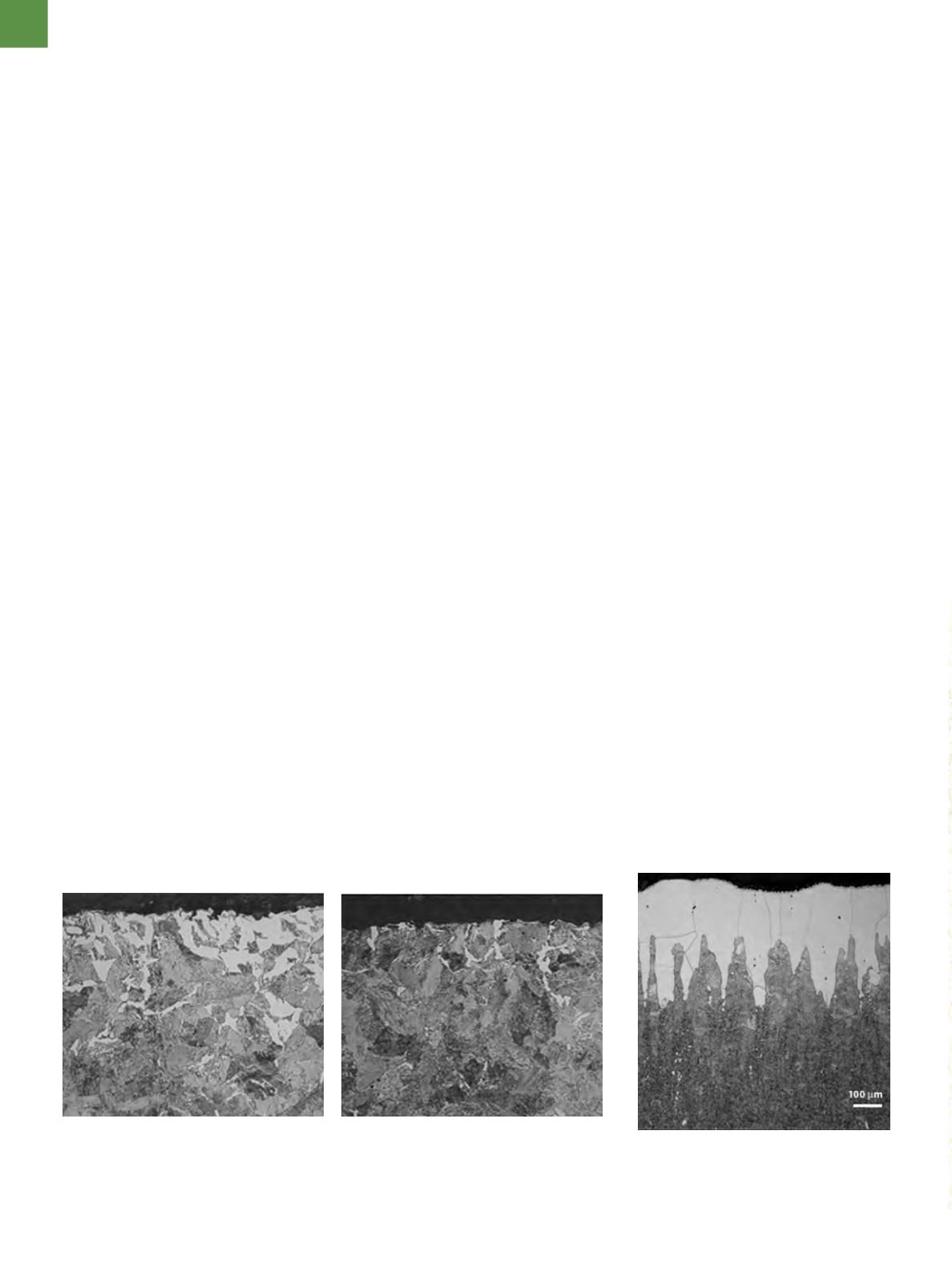
D
ecarburization is detrimental to
the wear life and fatigue life of
steel heat-treated components.
This article explores some factors that
cause decarburization while concentrat-
ing on its measurement. In most produc-
tion tests, light microscopes are used to
scan the surface of a polished and etched
cross-section to find what appears to be
the greatest depth of total carbon loss
(
free-ferrite depth,
or FFD) and the great-
est depth of combined FFD and partial
loss of carbon to determine the
maxi-
mumaffected depth
(MAD).
In some cases, there is no free
ferrite at the surface. In research stud-
ies, this may be supplemented with a
Knoop hardness traverse to determine
the depth where hardness becomes con-
stant. The Knoop-determined MAD is of-
ten somewhat deeper than the visually
determined MAD, as variations in the mi-
crostructure of carbon contents close to
the core may be difficult to discern. The
MAD determined by hardness traverse
may be slightly shallower than that de-
termined by quantitative carbon analysis
with the electron microprobe. This is es-
pecially true when the bulk carbon con-
tent exceeds about 0.45 wt%, as the rela-
tionship between carbon in the austenite
before quenching to formmartensite and
the as-quenched hardness loses its linear
nature above this carbon level.
Decarburizationbasics
Decarburization occurs when car-
bon atoms at the steel surface interact
with the furnace atmosphere and are
removed from the steel as a gaseous
phase
[1-8]
. Carbon from the interior diffus-
es towards the surface, moving fromhigh
to low concentration and continues until
the maximum depth of decarburization
is established. Because the carbon dif-
fusion rate increases with temperature
when the structure is fully austenitic,
MAD also increases as temperature rises
above the Ac
3
. For temperatures in the
two-phase region, between the Ac
1
and
Ac
3
, the process is more complex. Carbon
diffusion rates in ferrite and austenite
are different, and are influenced by both
temperature and composition.
Decarburization is a serious prob-
lembecause surface properties are infe-
rior to core properties, resulting in poor
wear resistance and low fatigue life. To
understand the extent of the problem,
two characteristics that may be present
at a decarburized steel’s surface can be
measured: Free-ferrite layer depth (FFD,
when present) and partial decarburiza-
tion depth (PDD, when free-ferrite is
UNDERSTANDING
ANDMEASURING
DECARBURIZATION
Understanding the forces behind decarburization is the first step toward
minimizing its detrimental effects.
George F. Vander Voort, FASM*, Struers Inc. (Consultant), Cleveland
*
Life Member of ASM International
Fig. 1
—Decarburized surface of as-rolled, eutectoid carbon steel (Fe-0.8%C-0.21%Mn-0.22%
Si) at two different locations around the periphery show a substantial variation in the amount
and depth of ferrite at the surface. The matrix should be nearly all pearlite (4% picral etch, 500×).
Fig. 2
— Erratic depth of free ferrite at
the surface of a bar of 440A martensitic
stainless steel after quenching from 2000°F
(1093°C); etched with Vilella’s reagent.
A D V A N C E D M A T E R I A L S & P R O C E S S E S | F E B R U A R Y 2 0 1 5
2 2