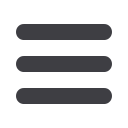
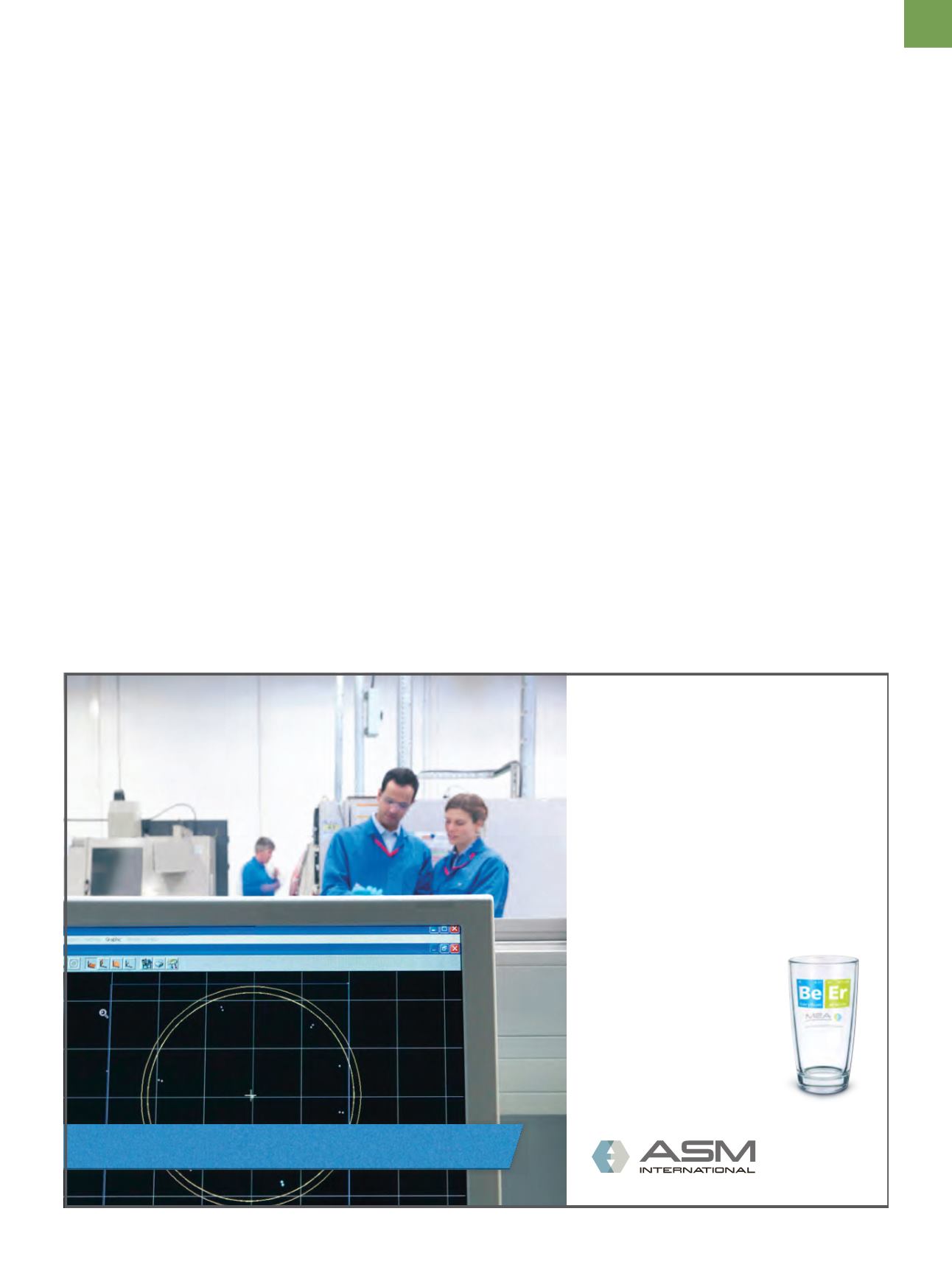
A D V A N C E D
M A T E R I A L S
&
P R O C E S S E S | F E B R U A R Y
2 0 1 5
2 7
quantitative average, which was based
on 25 randommeasurements around the
periphery. If it was assumed that the vi-
sual estimate of the greatest MAD around
the bar periphery would be deeper than
themean MAD of 25 randomly chosen lo-
cations, then the actual result would be
rather surprising.
Conclusions
Decarburization of steel parts is a
serious problem as the weaker surface
layer reduces wear resistance, enabling
fatigue failures to occur more easily. A
simple screening test was discussed,
which can be used for certain shapes
and high production runs. If the sur-
face hardness is below some predeter-
mined limit, which varies with grade,
then a microstructural examination is
required. Chemical analysis of carbon
on incremental turnings (or millings)
can be performed, although this is
more applicable to research than pro-
duction. Metallographic rating of de-
carburization depth requires properly
prepared specimens with good edge
retention. This can easily be achieved
with modern equipment and is reason-
ably fast. Qualitative measurements of
the free-ferrite depth (when present)
and the maximum affected depth of de-
carburization are usually adequate. But
such measurements are subject to bias
and the reproducibility is not as good as
when quantitative measurements are
made using at least 25 randomly select-
ed locations around the bar periphery.
Microindentation hardness traverses
are excellent for defining the MAD. The
FFD is easily observed by light micros-
copy and adequate inspection of the
periphery is needed to detect the deep-
est amount present.
~AM&P
For more information:
George F. Vander
Voort is a consultant for Struers Inc.,
24766 Detroit Rd., Cleveland, OH 44145,
847.623.7648,
georgevandervoort@yahoo. com, www.georgevandervoort.com.
References
1. A. Bramley and K.F. Allen, The Loss of
Carbon from Iron and Steel When Heated
in Decarburizing Gases,
Engineering
(Lon-
don), Vol 133, p 92-94, 123-126, 229-231,
and 305-306, 1932.
2. J.K. Stanley, Steel Carburization and De-
carburization – A Theoretical Analysis,
Iron
Age,
Vol 151, p 31-39 and 49-55, 1943.
3. F.E. Purkert, Prevention of Decarburiza-
tion in Annealing of High Carbon Steel,
J. Heat Treating,
Vol 2, p 225-231, 1982.
4. H.W. Grasshoff, et al., Effect of Different
Dew Points of the Heat Treating Atmo-
sphere on the Skin Decarburization of
Heat-Treatable Steels,
Stahl ünd Eisen
,
Vol 89(3), p 119-128, 1969.
5. G.E. Wieland and E.M. Rudzki, Effects of
Furnace Design and Operating Parameters
on the Decarburization of Steel,
Metal
Progress,
p 40-46, February 1979.
6. R. Rolls, Heating in the Drop Forge:
Formation and Properties of Scales on
Iron-Base Alloys,
Metal Forming,
Vol 34,
p 69-74, 1967.
7. K. Sachs and C.W. Tuck,
Surface Oxida-
tion of Steel in Industrial Furnaces,
ISI SR
111, London, p 1-17, 1968.
8. E. Schuermann, et al., Decarburization
and Scale Formation,
Wire Journal,
Vol 7,
p 155-164, 1974.
FREEPERIODICBEERGLASS! Get a FREE Periodic Beer Glass when you ask for your no-obligation training assessment. Contact Ravi Dodeja for complete details. Phone: 440.338.5414 Email: ravi.dodeja@asminternational.org CUSTOMIZEDTRAINING COMESTOYOU ASM’s Customized On-Site Training brings personalized courses to your facility that will elevate performance and increase production. Features include: • A productive use of your staff’s time with convenient access to world-class instructors at your facility • Information that is immediately applicable to • Programs customized to fit your needs your business after the course is completed REGISTER NOW AT ASMINTERNATIONAL.ORG/LEARNING/COST