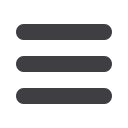
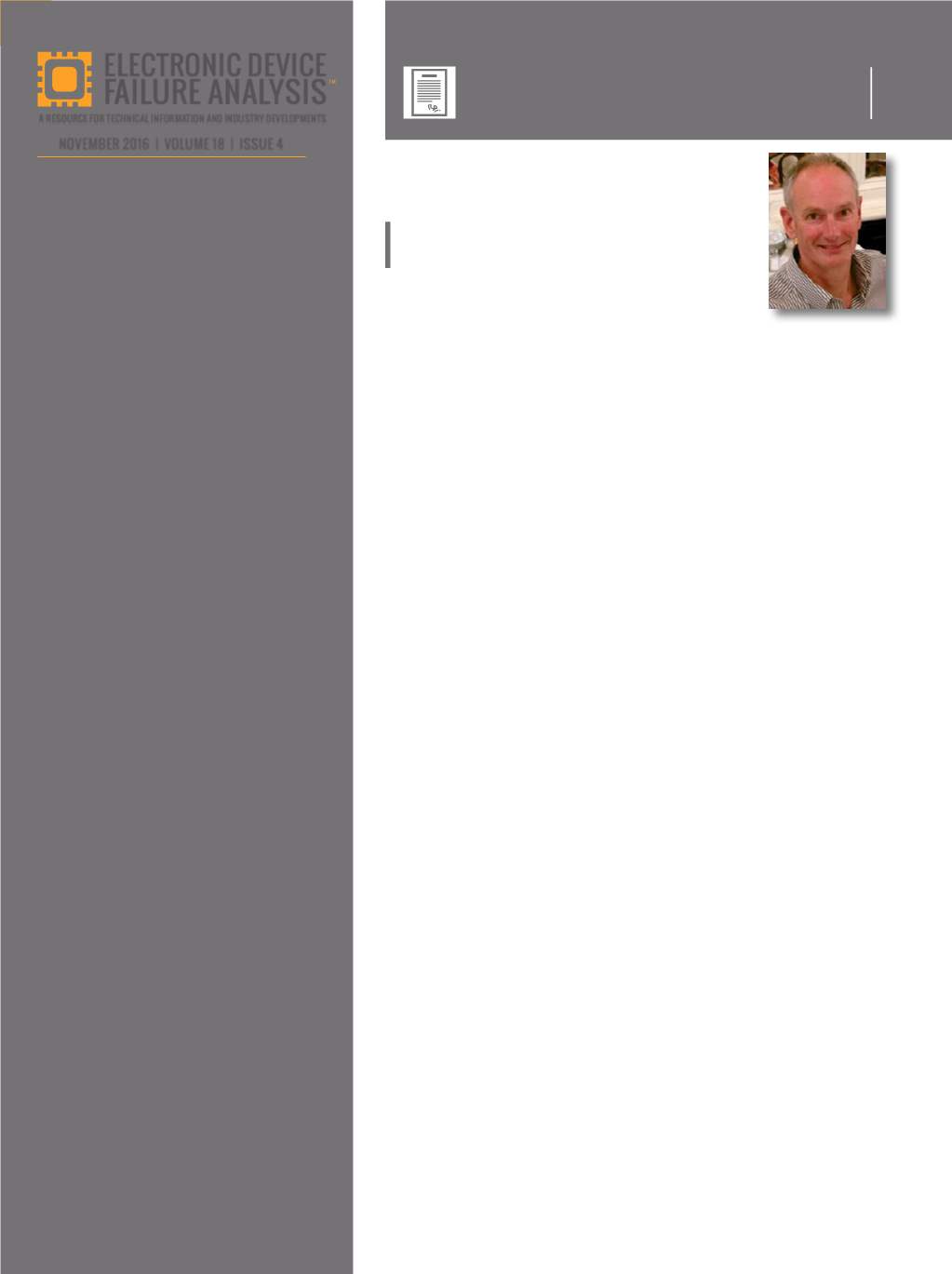
edfas.org
ELECTRONIC DEVICE FAILURE ANALYSIS | VOLUME 18 NO. 4
2
PURPOSE:
To provide a technical condensation of
information of interest to electronic device failure
analysis technicians, engineers, and managers.
Felix Beaudoin
Editor/Globalfoundries; felix.beaudoin@
globalfoundries.com
Scott D. Henry
Publisher
Mary Anne Fleming
Manager, Technical Journals
Kelly Sukol
Production Supervisor
Liz Marquard
Managing Editor
ASSOCIATE EDITORS
Michael R. Bruce
Consultant
David L. Burgess
Accelerated Analysis
Lihong Cao
ASE Group
Jiann Min Chin
Advanced Micro Devices Singapore
Edward I. Cole, Jr.
Sandia National Labs
James J. Demarest
IBM
Christopher L. Henderson
Semitracks Inc.
Jason M. Higgins
TSMC (Wafertech)
Bobby Hooghan
Weatherford Laboratories
Eckhard Langer
Globalfoundries
Philippe H.G. Perdu
CNES France
Rose M. Ring
Qorvo, Inc.
H.S. Silvus, Jr.
Southwest Research Institute
E. Jan Vardaman
TechSearch International, Inc.
Martin Versen
University of Applied Sciences Rosenheim, Germany
Lawrence C. Wagner
LWSN Consulting Inc.
GRAPHIC DESIGN
www.designbyj.comPRESS RELEASE SUBMISSIONS
magazines@asminternational.orgElectronic Device Failure Analysis™
(ISSN 1537-0755) is pub-
lished quarterly by ASM International
®
, 9639 Kinsman Road,
Materials Park, OH 44073; tel: 800.336.5152; website: edfas.
org.Copyright©2016byASM International.Receive
Electronic
Device Failure Analysis
as part of your EDFAS membership
of $88 U.S. per year. Non-member subscription rate is $135
U.S. per year.
Authorizationtophotocopy itemsfor internalorpersonaluse,
orthe internalorpersonaluseofspecificclients, isgrantedby
ASM Internationalfor librariesandotherusersregisteredwith
theCopyrightClearanceCenter(CCC)TransactionalReporting
Service, provided that the base fee of $19 per article is paid
directlytoCCC,222RosewoodDrive,Danvers,MA01923,USA.
Electronic Device Failure Analysis
is indexed or abstracted by
Compendex, EBSCO, Gale, and ProQuest.
T
he ever-increasing financial stakes faced by semi-
conductor high-volumemanufacturing (HVM) on
moving to the next node have propelled failure analysis (FA) to levels
unimaginable even 20 years ago. The primary driving forces behind this can
be summed up as resulting from:
• Increased process complexity (new materials and structures)
• Increased number of mask steps per device node
• Tighter process control
The increased process complexity derives from the fact that 20 years
ago shrinkage simply entailed shrinkage. However, excessive leakage (short
channel effects, etc.) in logic devices brought an end to this Dennard scaling
at approximately the 130 nm node (launched in 2001, at which time copper
interconnects and low-k dielectrics were already mainstream). Progressing
beyond 130 nm required the introduction of strain engineering, high-kmetal
gate stacks, and movement to 3-D structures.
The increased number of mask steps arises from the increased process
complexity discussed above, and the fact that ArF lithography (193 nmwave-
length) has been used throughout the 90 to 14 nm logic nodes, with the latter
being well beyond the dry ArF lithography diffraction limit. Surpassing this
limit has required the introduction of new approaches, such as immersion
lithography (193
i
), phase shift masks (PSM), optical proximity correction
(OPC), litho-etch-litho-etch (LELE) techniques, self-aligned double pattern-
ing (SADP), and so on. Moving to 7 nmwithout the use of extreme ultraviolet
(EUV) lithography will likely require the extension of LELE, that is, LELELELE,
implementation of self-aligned quadruple patterning (SAQP), and so on.
These processes have driven the number of mask steps from ~50 steps for
the 28 nmnode when using OPC, PSM, 193
i
, etc., to ~66 steps for 14 nmwhen
using OPC, 193
i
, PSM, SADP, etc., to an expected ~80 steps for the 7 nm node
if not using EUV.
Tighter process control drives the need for additional metrology andmore
stringent control of contamination/particles. In this vein, airborne particle
sizes have not changed over the last 20 years, which implies that their impact
should increase in a quadratic fashion with each subsequent node. In addi-
tion, smaller particles are having a greater impact.
The scope of FA labs can encompass everything fromthe chemical analysis
of incoming chemicals, qualification/matching of process tools/recipes/envi-
ronment, to the evaluation of the root cause of electrical issues noted at the
unfinished die through to the shipped package level. As withHVM, the FA labs
have had to derive newanalytical solutions to the questions raised onmoving
NOVEMBER 2016
|
VOLUME 18
|
ISSUE 4
A RESOURCE FOR TECHNICAL INFORMATION AND INDUSTRY DEVELOPMENTS
ELECTRONIC DEVICE
FAILURE ANALYSIS
(continued on page 45)
GUEST EDITORIAL
FAILURE ANALYSIS IN HIGH-VOLUME
MANUFACTURING
P.A.W. van der Heide, Globalfoundries
paul.vanderheide@globalfoundries.com