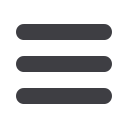
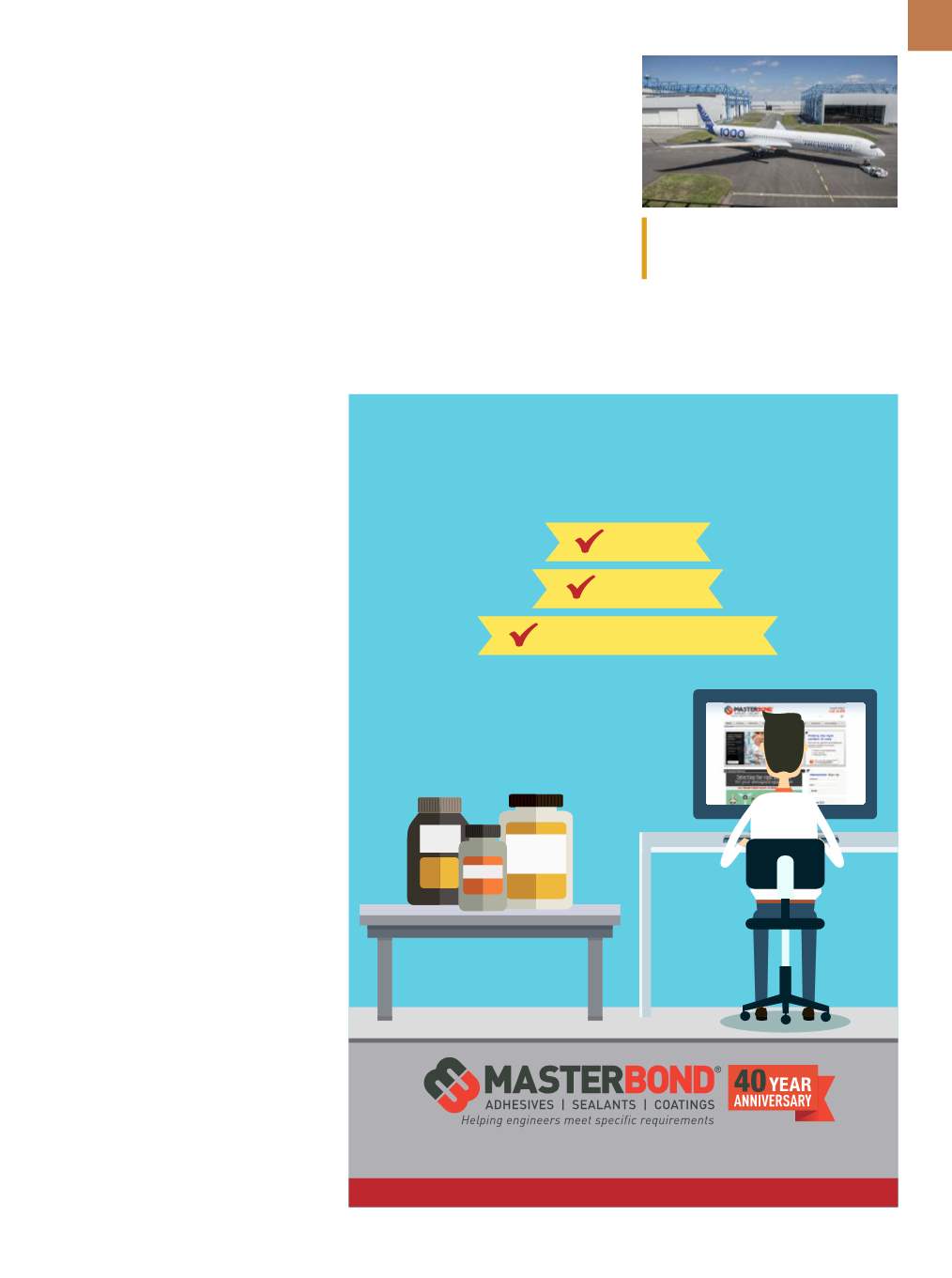
A D V A N C E D
M A T E R I A L S
&
P R O C E S S E S |
O C T O B E R
2 0 1 6
9
light-duty automotive sector is recov-
ered and recycled from vehicles at end
of life. The study, “Automotive Alumi-
num Recycling at End of Life: A Grave-
to-Gate Analysis,” provides a lifecycle
evaluation, which begins the moment
an automobile becomes obsolete and
ends the moment the aluminum met-
al units are completely recycled and
ready to be used as input material for
new applications, including vehicles.
Researchers
attribute
automotive
aluminum’s high recycling rate to its
economic value, citing the “concerted
effort to recover this valuable light-
weight commodity from end-of-life
vehicles.”
drivealuminum.org.
INJECTION MOLDING CREATES
COMPLEX CERAMIC PARTS
Scientific Ceramic Engineering,
Spotsylvania, Va., licensed a Purdue
University, West Lafayette, Ind., ceramic
injection-molding technology that uses
room temperature molding, low pres-
sure machinery, and less toxic materi-
als to produce stronger, faster, and less
expensive complex ceramic parts for a
multitude of industries. The innovation
uses an injection molding technology
to form high-temperature ceramic parts
with complex dimensions by taking
advantage of temperature flow prop-
erties of water-based ceramic suspen-
sions. The molding technique enables
ceramic materials to be machined with
high precision and accuracy. The tech-
nology also provides consistent dimen-
sionsafter sintering for reliableaccuracy
and improved strength and toughness
for a stronger finished product, says
CEO David Forster.
scientificcim.com.
ALUMINUM FLIES HIGH
IN AIRCRAFT
Aleris, Cleveland, signed a multi
year contract with Airbus, France, to
supply aluminum plate and sheet to
be used in the production of all Airbus
aircraft programs. The contract starts
in 2017 and also includes the supply
of technically advanced wing skin ma-
terial. The agreement includes not
only aluminum plate and sheet used in
applications including aircraft fuse-
lage and wing structures, but also the
supply of wing skins—a highly special-
ized product that requires additional
processing and pre-machining. The
contract includes the supply of ma-
terial from the company’s facilities in
Koblenz, Germany, and Zhenjiang,
China, the latter of which represents a
$350 million greenfield project for Aler-
is. This facility was qualified by Airbus
for the production of aerospace materi-
al in 2015.
aleris.com, airbus.com.
Aleris signed a multiyear contract with Air-
bus to supply aluminumplate and sheet
for use in all Airbus aircraft.
www.masterbond.com 154 Hobart St., Hackensack, NJ 07601, USA +1.201.343.8983 mainmasterbond.com FAR Certified NASA Low Outgassing Approved UL Rated EPOXIES SILICONES UV/LED CURING SYSTEMS Helping engineers find the right adhesive system