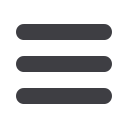
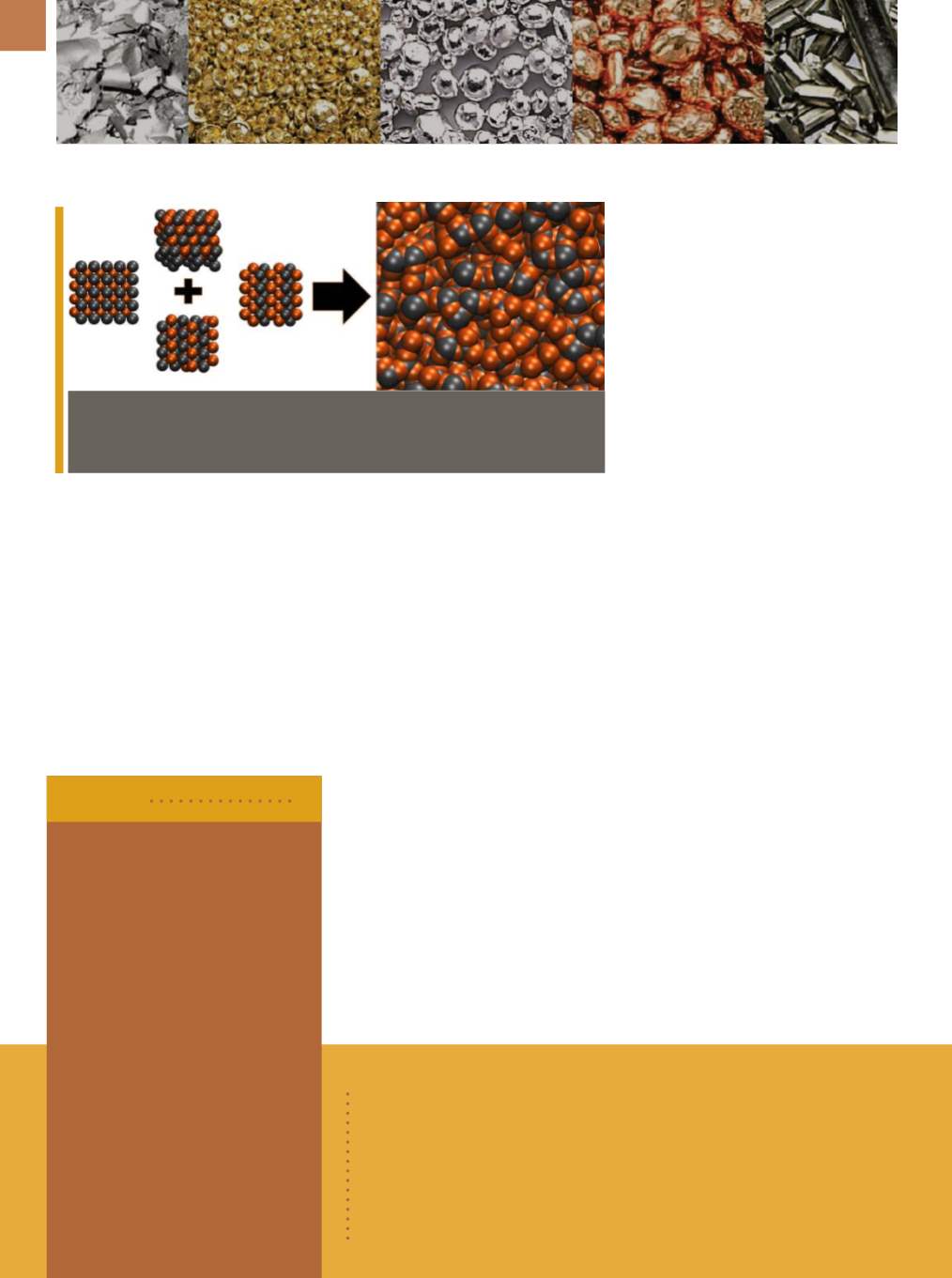
A D V A N C E D M A T E R I A L S & P R O C E S S E S | O C T O B E R 2 0 1 6
8
METALS | POLYMERS | CERAMICS
energies, you get a sort of frustration
as the material tries to crystalize,” adds
Eric Perim, a postdoctoral researcher at
Duke. “The material can’t decide which
crystalline structure it wants to con-
verge to, and a metallic glass emerges.
What we created is basically a measure
of that confusion.” The team at Duke
developed a database to simulate the
hundreds of crystalline structures each
alloy could potentially take. They cre-
ated a program to analyze the various
structures and compare the energy
required to form them. Alloys that can
form many different structures whose
energy is similar are likely candidates
to form a metallic glass. The teams
at Harvard and Yale then verified the
predictions experimentally. The new
approach is able to predict the forma-
tion of known metallic glasses 73% of
the time and has identified hundreds of
new candidates for metallic glass made
from simple, two-element alloys. Now
that the researchers can predict good
candidates for metallic glass, they can
start looking for new material systems.
seas.harvard.edu.
AUTOMOTIVE ALUMINUM
RECYCLING GOING STRONG
New research from Worcester
Polytechnic Institute’s (WPI) Center
for Resource Recovery and Recycling
confirms an overall recycling rate of
91% for automotive aluminum in the
U.S. The peer-reviewed study, funded
by the Aluminum Association, exam-
ines how much aluminum used in the
Whenmetal alloys are melted, the atoms lose their ordered structure and become
amorphous, as seen above. Courtesy of the Vlassak Group/Harvard SEAS.
A hydrolysis-resistant, bio-based
polyamide, EcoPaXX, from
Royal
DSM,
the Netherlands, was recent-
ly approved for use by a German
car manufacturer. A thin-walled
T
connector for a coolant hose in
this grade, Akulon PA66, is now
available in two versions: HR-HG6
and HR-HG7, containing 30% and
35% glass fiber reinforcement, re-
spectively. Both comply with OEM
requirements for a high retention
of flexural strength after immer-
sion in the solution for 1000 hours
at 135°C. Targeted applications
include expansion tanks, air intake
manifolds, oil pans with integrated
cooling channels, and oil filter/
cooler modules.
dsm.com.
BRIEFS
Hot rolled or hot forged bars of AUTO-Steel from
Advanced Materials
Development (AMD) Corp.,
Canada, can be used in car and truck car-
burized powertrain and transmission components such as camshafts,
gears, axles, and shafts. Carburized Grade1 features surface hardness of
HRC 61-62 and core hardness of HRC 45-46. Grade2 is a medium carbon,
deep nitriding composition suited for high precision components. After
quenching and tempering, Grade3 features hardness of HRC 58-60 and
UTS of 325-335 ksi.
info@amdoncorp.com.
FINDING ALLOYS TO FORM
BULK METALLIC GLASS
Researchers from the Harvard John
A. Paulson School of Engineering and
Applied Sciences (SEAS), Cambridge,
Mass., in collaboration with colleagues
from Duke and Yale universities, re-
cently developed a method to predict
which alloys might form a bulk metal-
lic glass. “For the first time, we’ve ob-
served a strong correlation between
the glass-forming ability of an alloy and
properties that we can easily calculate
ahead of time,” says Joost J. Vlassak, a
materials engineering professor at SEAS.
When metal alloys are melted, the
atoms lose their ordered structure—al-
though most will snap back to their rigid
crystal structures when cooled. Howev-
er, bulk metallic glasses, if cooled at cer-
tain rates, will retain the random amor-
phous structure even in the solid state.
Yet some alloys havemore options when
it comes to their crystal structures. When
these alloys are being cooled into solids,
their atoms could crystallize in many dif-
ferent ways. “If a particular alloy compo-
sition exhibits many structurally differ-
ent, stable or metastable crystal phases
that have similar formation energies,
these phases will compete against each
other during solidification,” explains
Vlassak. “Essentially, the liquid becomes
so confused, it remains amorphous as it
solidifies.”
“When you get a lot of structures
forming next to one another that are
different but still have similar internal