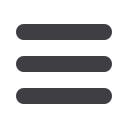
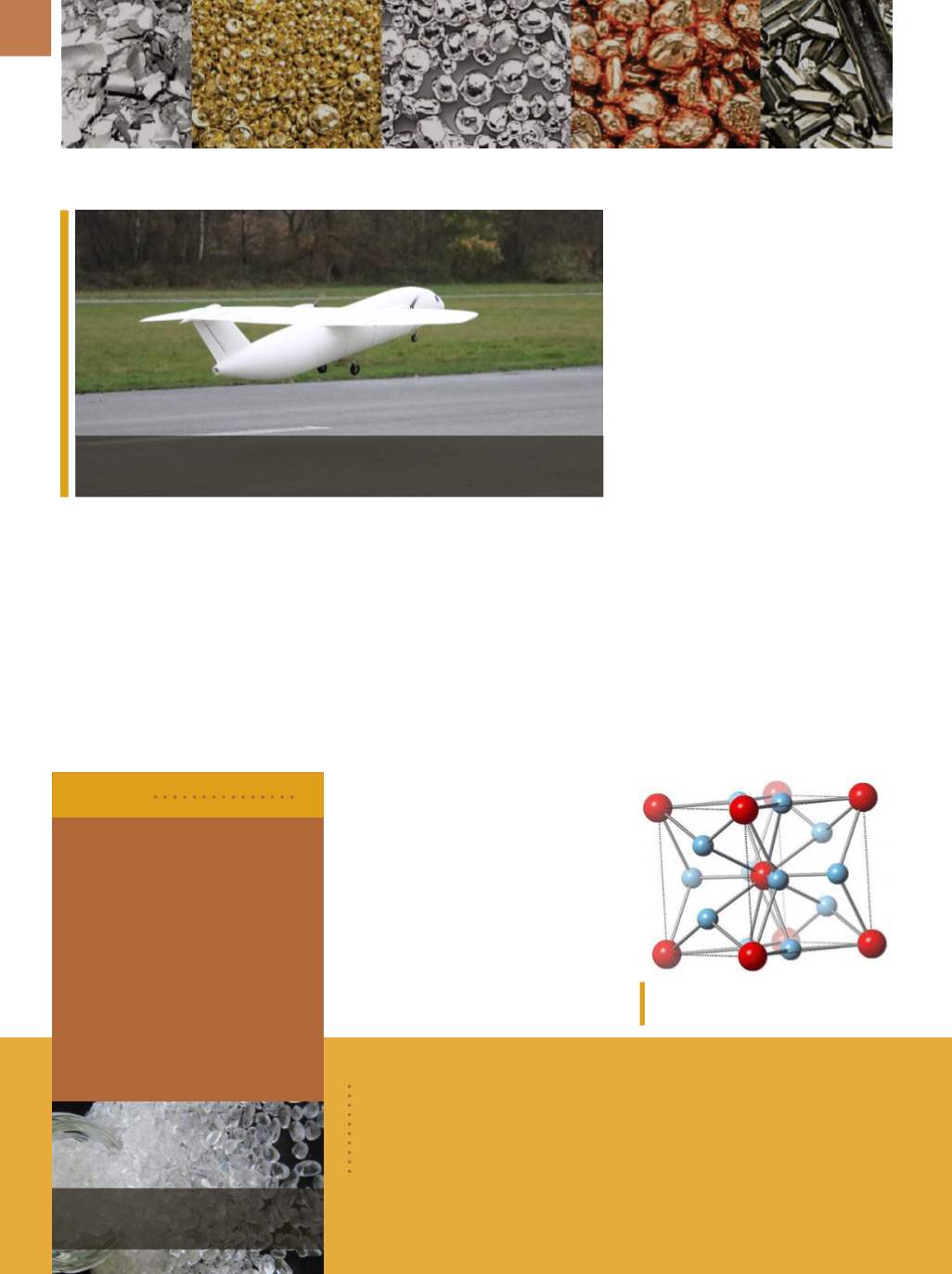
A D V A N C E D M A T E R I A L S & P R O C E S S E S | S E P T E M B E R 2 0 1 6
8
METALS | POLYMERS | CERAMICS
GOLD BOOSTS TITANIUM
KNEE STRENGTH
Titanium is the leading material for
artificial knee and hip joints because it is
strong, wear resistant, and nontoxic, but
adding gold might make implants even
better. “It is about three to four times
harder than most steels,” says Emilia
Morosan, a materials science professor
at Rice University, Houston. The proper-
ties of a 3-to-1 mixture of titanium and
gold with a specific atomic structure
impart the hardness. “It’s four times
harder than pure titanium, which is
what’s currently being used inmost den-
tal implants and replacement joints.” It’s
not clear that Morosan and former grad-
uate student Eteri Svanidzewere the first
to make a pure sample of the ultrahard
beta form of the compound. However,
due to a couple of lucky breaks, they
are the first to document the material’s
remarkable properties.
Researchers measured the hard-
ness of the beta form of the crystal and
also performed other comparisons with
Thor, a 3D-printed flying model, took off for its maiden flight in Germany last
November.
Polyscope Polymers B.V.,
the
Netherlands, expanded its Xiran
heat boost range. Originally
introduced to increase the high
temperature resistance of acry-
lonitrile butadiene styrene and
acrylonitrile styrene acrylate, Xiran
heat boosters can now increase the
heat performance of other styrenic
polymers, such as polystyrene and
styrene acrylonitrile, as well as
polymethylmethacrylate.
www.polyscope.eu.
BRIEFS
Stainless steel rebar produced by
Outokumpu,
Finland, is being used to
reinforce a spill basin at the new liquefied natural gas Gate Terminal on
Rotterdam’s North Sea coast. Both the basin’s concrete and reinforce-
ment must withstand the extreme conditions of a cryogenic environment
and temperatures as low as -165°C.
outokumpu.com/rebar.
PRINT ME AN AIRPLANE
Airbus, France, is using a mini
aircraft project known as Thor (test-
ing high-tech objectives in reality) as a
testbed for futuristic aircraft technolo-
gies—from 3D-printed structural parts
to advanced aerodynamics and even
artificial intelligence. The initial Thor
version weighs approximately 21 kg
and can fit in a 4×4 m square. It is pow-
ered by two 1.5-kW electrically-driven
propellers, and 90% of its structural
components were 3D-printed from
plastic polyamide powder.
“This mini aircraft does not repre-
sent an actual airliner design Airbus is
considering, rather it is a platform to
enable low-risk and fast-track devel-
opment of different technologies in
real flying conditions,” explains Detlev
Konigorski, who oversees the project.
“The first version was to test whether
the slogan ‘Print me an airplane’ can be
converted into reality.”
A major advantage of Thor is the
short lead time of 3D printing, which
significantly reduces development time
for producing the technology demon-
strator compared to traditional man-
ufacturing methods. Using an existing
design concept, it took seven weeks
to print the aircraft’s 60 structural
segments, followed by one week for
assembly and three days to fine tune
the electrical systems before it was
flight-ready.
airbus.com.
Crystal structure of beta titanium-3-gold.
Courtesy of E. Morosan/Rice University.
Xiran heat boosters resist high
temperatures.