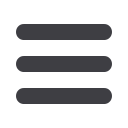
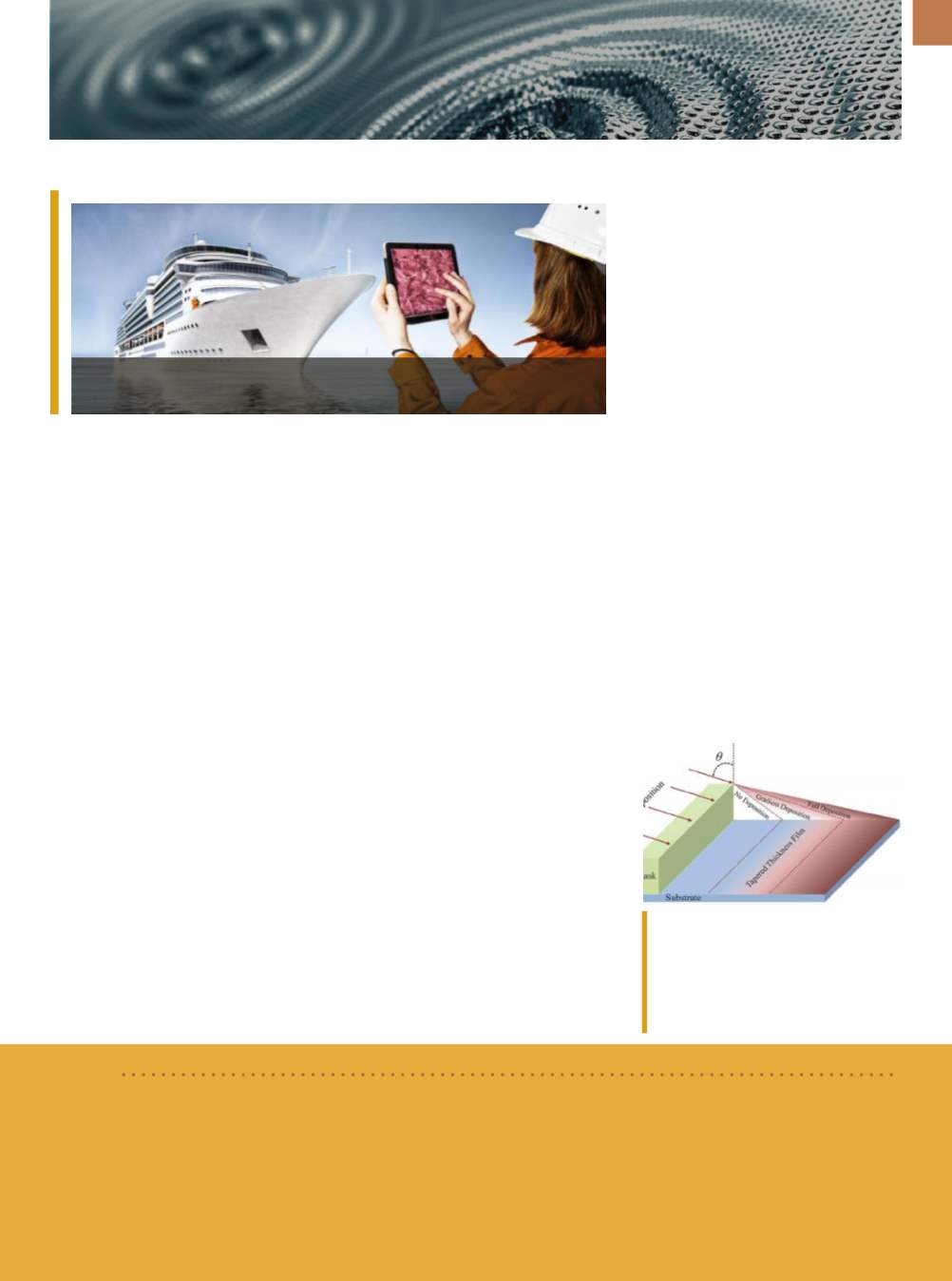
A D V A N C E D
M A T E R I A L S
&
P R O C E S S E S | J U L Y / A U G U S T
2 0 1 6
1 5
SURFACE ENGINEERING
NEW TECHNIQUE PROTECTS
STEEL FROM RUST
Researchers at INM—Leibniz Insti-
tute for New Materials, Germany, devel-
oped a special type of zinc-phosphate
nanoparticles to combat corrosion in
steel plates and girders used in architec-
ture, construction, and bridge building.
In contrast to conventional, spheroidal
zinc-phosphate nanoparticles, the new
nanoparticles are flake-like and 10 times
as long as they are thick. As a result of
this anisotropy, gas molecules cannot
penetrate the metal as fast.
Steel plates were immersed in elec-
trolyte solutions with both spheroidal
zinc-phosphate nanoparticles and with
flake-type zinc-phosphate nanoparti-
cles in each case. After just half a day,
the steel plates in the electrolytes with
spheroidal nanoparticles showed signs
of corrosion where the steel plates in the
electrolytes with flake-type nanopar-
ticles were still in perfect condition
and shining—even after three days.
Researchers created their particles using
standard, commercially available zinc
salts, phosphoric acid, and an organic
acid as a complexing agent. The more
complexing agent they added, the more
anisotropic the nanoparticles became.
www.leibniz-inm.de/en.
CONTROLLED DEPOSITION
CREATES COMPLEX
STRUCTURES
A team of researchers at Purdue
University, Lafayette, Ind., developed
an angled vapor-deposition system that
allows for more controlled deposition
for the creation of complex and novel
quasi-3D structures. Physical vapor
deposition (PVD) is a common method
for creating structures such as perfectly
flat thin films. However, the method is
fairly static and deposition occurs per-
pendicular to the vapor source.
In order to deposit complex struc-
tures, the team took advantage of the
line-of-sight properties of vapor depo-
sition. Unlike a traditional PVD setup,
where the deposition angle is perpendic-
ular to the substrate, they used a system
whereboth thedepositionangle and sub-
strateangle canbemanipulated. This sys-
tem, known as glancing angle deposition
Flake-type nanoparticles of zinc-phosphate increase the gas barrier for corrosion
protection in steel. Courtesy of INM/Uwe Bellhäuser.
Mask, angled deposition can be used to
create thickness gradient thin films. The
mask blocks deposition from occurring
on the substrate closest to it, with thick-
ness increasing moving away from the
mask. Courtesy of Alexandra Boltasseva.
(GLAD), creates shadow regions, where
parts of the substrate are blocked from
the deposition line of sight. This allows
for controlled buildup of material in one
area, leaving others untouched.
One of the more straightforward
applications of this system is tapered
thickness films. GLAD can also create
far more complex structures, espe-
cially when nonplanar substrates are
used. Much like a masked flat surface,
a curved surface will receive differing
thickness of deposition. A sphere, for
example, would receive the largest
amount of depositedmaterial at a point
perpendicular to the deposition angle,
with a gradient along the curve. How-
ever, by rotating the substrate, most
of the surface region of the sphere will
be capped by the evaporation source,
leading to an onion-shaped core-
shell structure. Alternating deposition
between metal and dielectric compo-
nents creates a multilayered core-shell
structure.
For more information: Alexan-
dra Boltasseva, 765.494.0301,
aeb@pur- due.edu, www.purdue.edu.BRIEF
Scientists at the
U.S. Naval Research Laboratory,
Washington, discovered that particle atomic layer deposition
(p-ALD) deposits a uniform nanometer-thick shell on core particles regardless of core size. The team grew alumina
on nano- and micron-sized particles of tungsten and measured the shell thickness in a transmission electron micro-
scope. Because of the huge mass/density difference of the two materials, this pairing provides maximum contrast in
the electron microscope and delineation is easily distinguishable between the particle core and shell.
nrl.navy.mil.