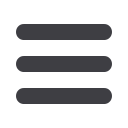
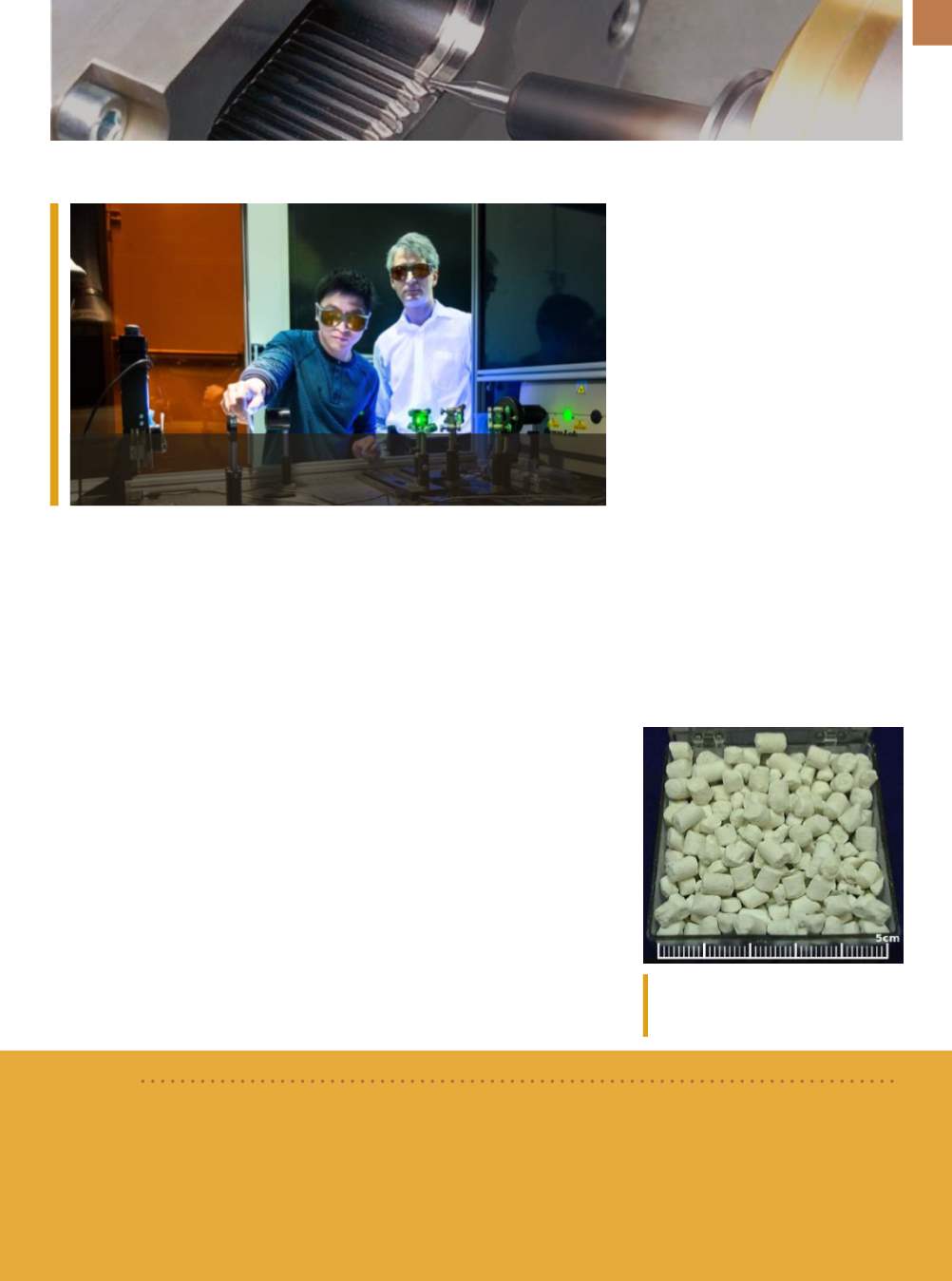
A D V A N C E D
M A T E R I A L S
&
P R O C E S S E S | J U L Y / A U G U S T
2 0 1 6
1 3
PROCESS TECHNOLOGY
Adrian Sabau (right) and Jian Chen work with a laser to prepare the surface of carbon
fiber composites and aluminum to create bonds that can absorb 200%more energy
than conventional joints.
LASERS IMPROVE MULTI-
MATERIAL BONDING
Scientists at the DOE’s Oak Ridge
National Laboratory, Tenn., developed
a new approach to join carbon fiber
composites and aluminum for use in
lightweight cars and other multimate-
rial high-end products. The method,
which uses a laser to prepare surfaces
for bonding, improves joint perfor-
mance and paves the way to automa-
tion. The laser not only removes surface
contaminants—a critical step prior to
bonding—but also penetrates the top
resin layer of the composite, leaving
individual carbon fibers exposed and
increasing the surface area for better
adhesion.
Test results for single-lap shear
joint specimens that used the laser
method show an increase in strength,
maximum load, and displacement at
maximum load of 15%, 16%, and 10%,
respectively, over measurements for
Lithiumpellets. To be used as a raw
material for batteries, lithiummust
be at least 99.5% pure.
BRIEFS
Nucor Corp.,
Charlotte, N.C., is forming a 50-50 joint venture with
JFE Steel Corp.,
Japan, to build and operate a $270 million
automotive plant in central Mexico to supply the local market. Estimated capacity is 400,000 tons per year of galvanized sheet
steel. Operations will begin in 2019.
nucor.com.
SolAero Technologies Corp.,
Albuquerque, N.M., provider of satellite solar power and structural solutions, acquired
Vanguard
Space Technologies Inc.,
San Diego, provider of satellite structural components and assemblies for commercial, defense, and
civil satellites. Founded in 1994, Vanguard has supplied more than 50 spacecraft with 100%mission success.
solaerotech.com.
baseline joints. Further, joints made
with laser-structured surfaces can
absorb approximately 200% more
energy than conventionally prepared
baseline joints, a good sign for crash
safety as well as potential use in vehi-
cle and body armor. Unlike conven-
tional methods of preparing surfaces
by hand using abrasive pads, grit
blasting, and harsh solvents, the laser
method can be automated, enabling a
more economical production process.
ornl.gov.
BATTERY RECYCLING,
PURE AND SIMPLE
For the first time, researchers at
Lappeenranta University of Technology,
Finland, extracted lithium, cobalt, and
nickel from battery waste, all at nearly
100% purity. The team used a liquid-liq-
uid process on a pilot scale, with a high-
flow rate device that simulated the
industrial scale. Extraction took place
between two liquid phases that do not
dissolve in each other, during which
impurities were separated from the
solution, leaving only the three metals.
Ultimately, researchers achieved 99.6%
purity for cobalt, 99.7% for nickel, and
99.9% for lithium. “If the purity of lith-
ium is below 99.5%, it is not suitable
as raw material for batteries. In other
words, the difference between 99.4%
and 99.9% purity is very significant,”
explains postdoctoral researcher Sami
Virolainen.
Previous
extraction
attempts
achieved relatively high purity for only
two of the three metals. While the global
demand for lithium is forecast to qua-
druple between 2011 and 2025, Europe
has few primary resources. Nickel is
more widespread, but the metal is
always found with cobalt in nature, and
separating the two—essential for bat-
tery manufacturing—has previously
proven difficult.
www.lut.fi.