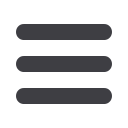
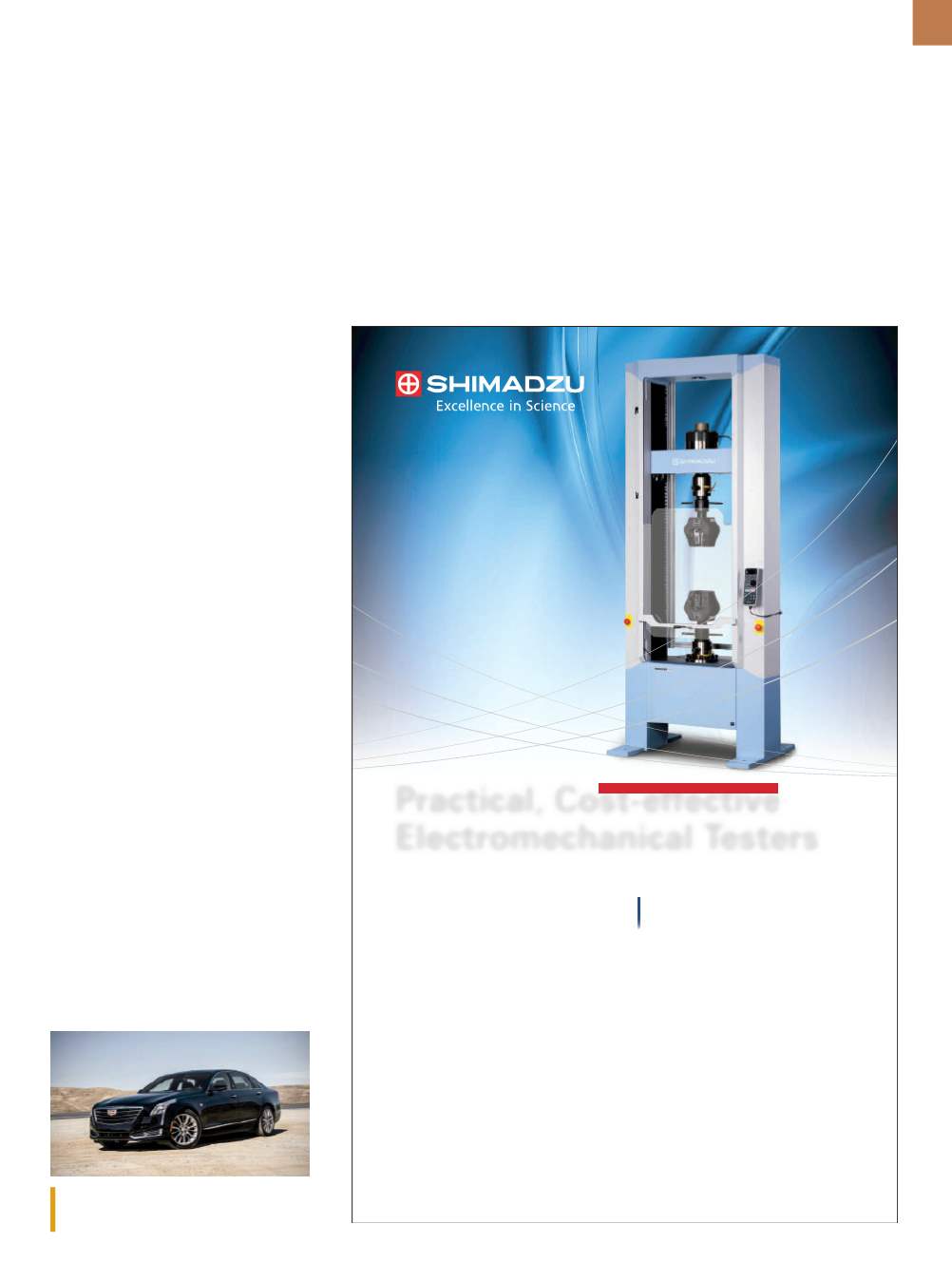
A D V A N C E D
M A T E R I A L S
&
P R O C E S S E S | J U L Y / A U G U S T
2 0 1 6
9
The Cadillac CT6 features a body made of
62% aluminum.
from Ichikoh Japan and INEOS Styrolu-
tion, Singapore. Ichikoh was searching
for a processing solution that looks
good at the weld joints of plastic parts.
As conventional weldingmethods were
unable to meet the innovative design
parameters, a new laser welding tech-
nique was used for the rear lamp hous-
ing, which offers more design freedom
and better surface appearance. The
new laser welding technique also has
the potential to generate more stabil-
ity and higher mechanical strength at
welded areas compared to conven-
tional methods.
In addition to the new technique,
the right material was needed. The
challenge with most black or dark
colored polymers is their high sensi-
tivity to laser beams, which results in
uneven surfaces at the weld joint when
a laser is applied. INEOS Styrolution
custom developed Novodur HH-112,
a high-heat acrylonitrile butadiene
styrene (ABS) specialty styrenic grade
that meets Ichikoh’s performance and
aesthetic requirements. This is the
first time an ABS resin has been used
for a black laser welded application.
ineos-styrolution.com.
CADILLAC CT6 SHAVES
WEIGHT WITH ALUMINUM
The 2016 Cadillac CT6 sports a
body made of 62%aluminum fromNov-
elis, Atlanta. By using aluminum and
advanced joining techniques, Cadillac
achieved significant weight savings,
making the full-size luxury sedan com-
parable in weight to the midsize CTS
sedan. When compared to a similar
size vehicle using predominantly high-
strength steel, the CT6 is approximately
220 lb lighter.
In both North America and Asia,
Novelis aluminum is used throughout
the vehicle body, including the pas-
senger and rear compartments, roof
structure, outer body panels, and door
and deck lid structures. The CT6 fea-
tures one of the most advanced mixed
use automotive body structures in
the industry, including all-aluminum
exterior body panels and rear-drive
architecture. GM’s advanced joining
methods are used to fabricate the
vehicle structure, including a propri-
etary aluminum spot welding technol-
ogy that reduces weight and increases
strength and efficiency. Laser weld-
ing, flow drill fasteners, and self-
piercing rivets are also used, along
with nearly 600 ft of advanced struc-
tural adhesives. The CT6 also features
a 10%stiffer body than its competitors.
novelis.com, gm.com.
Combining advanced specifications with an affordable, modern design, Shimadzu’s AGS-X Series of floor and tabletop universal testers delivers practical solutions across a wide range of applications. By incorporating multiple control options, load cells with maximum capacities from 1 N to 300 kN, and the utmost in safety considerations, the AGS-X series is the choice for easier, more efficient testing . Shimadzu’s AGS-X Series features: ■ Accurate stress-strain curves with Class 0.5 load cells ■ High-speed data sampling up to 1 msec (1 kHz) ■ Precise stress- and strain-controlled testing ■ Comprehensive safety measures ■ Easy-to-use software with a refined user interface for more efficient, effective testingShimadzu Scientific Instruments Inc., 7102 Riverwood Dr., Columbia, MD 21046, USA
Learn more. Call (800) 477-1227 or visit us online at www.ssi.shimadzu.com/AGSX Practical, Cost-effective Electromechanical Testers In addition, a comprehensive selection of grips, compression plates, jigs, extensometers, and other accessories allow configurations to be tailored to almost any application. Adaptable to Countless Applications