
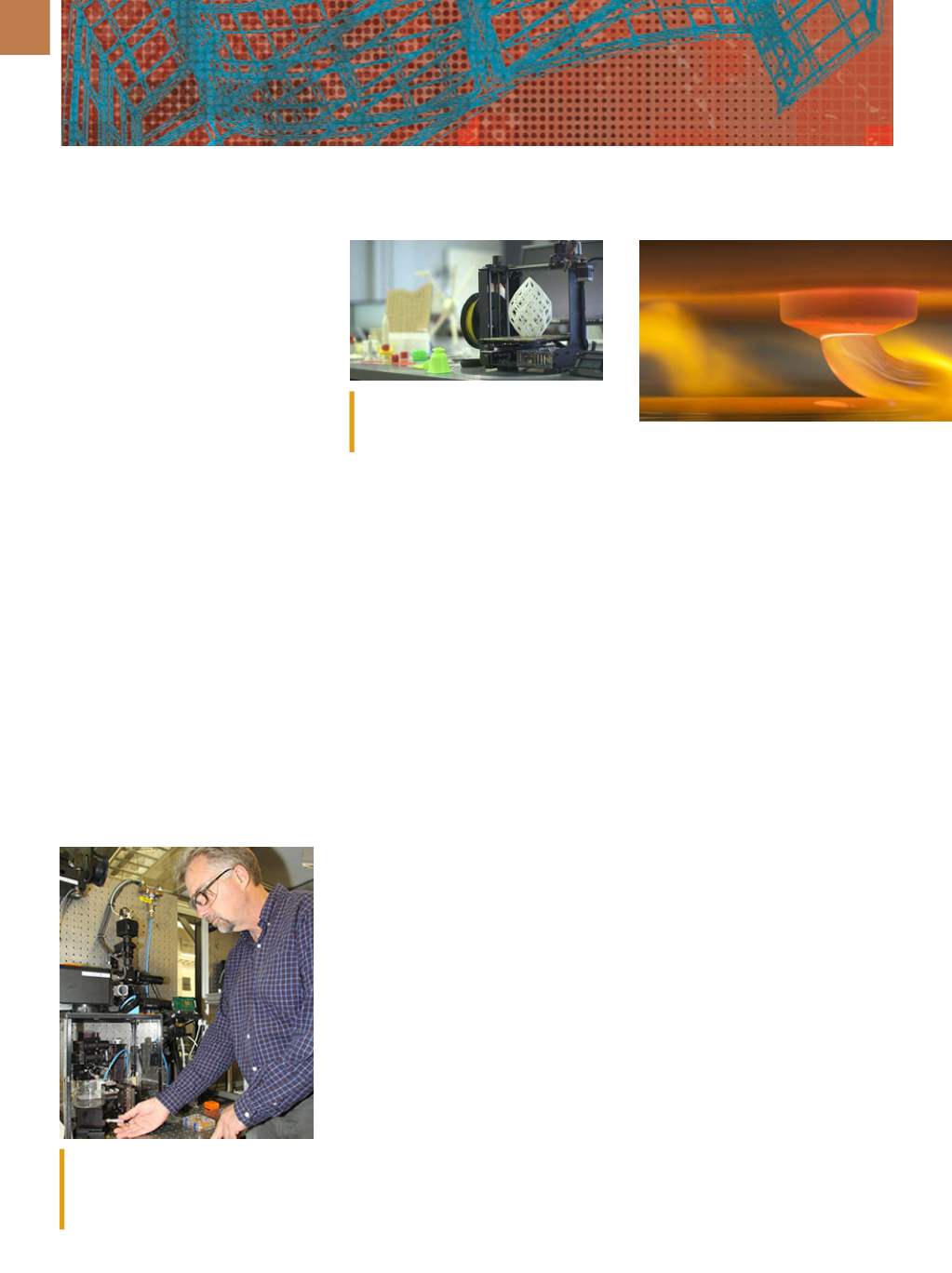
A D V A N C E D M A T E R I A L S & P R O C E S S E S | J A N U A R Y 2 0 1 6
7 6
NEW PRINTER OFFERS BEST OF BOTH WORLDS
3D PRINTSHOP
A
3D-printing device developed by
a Lawrence Livermore Nation-
al Laboratory (LLNL) engineer
won a 2015 Federal Laboratory Consor-
tium (FLC) Far West Region Award for
outstanding technology development.
The award, given for the Large Area
Projection Micro Stereolithography
(LAPµSL) technology, was presented
to Bryan Moran at the recent FLC Far
West/Mid-Continent Region meeting in
San Diego. The LAPµSL is an image pro-
jection micro-stereolithography system
that rapidly produces very small fea-
tures over large areas by using optical
techniques to write images in parallel.
This approach is a departure from con-
ventional techniques, which either re-
quire mechanical stage movements or
the rastering of beams to expose pixels
in series. LAPµSL combines the advan-
tages of laser-based stereolithography
(large area and speed, but poor resolu-
tion) and digital light processing stereo-
lithography (fine details and speed, but
only over a small area), enabling rapid
printing of fine details over large areas.
“
The LAPµSL system is conceptu-
ally similar to building a mosaic of tiles
that thencombine tomakeamuch larger
picture,
”
says Moran. He adds that many
applications could benefit from the abil-
ity to create complex shapes and small
features, unlike other 3D printers, which
sacrifice overall part size for small fea-
ture size. For example, parts produced
with the new machine can be used as
master patterns for injection molding,
thermoforming, blow molding, and var-
ious metal casting processes.
For more
information: Bryan Moran,
925.423.3568, moran5@llnl.gov,
www.llnl.gov.
PARTNERSHIP EXPLORES
HEALTH IMPACT OF PRINTER
EMISSIONS
UL, a safety science organization
based in Northbrook, Ill., recently an-
nounced partnerships with Georgia
Institute of Technology and Emory Uni-
versity’s Rollins School of Public Health
to study the impact of 3D printing on
indoor air quality. The research is de-
signed to characterize chemical and
particle emissions of 3D printing tech-
nologies and to evaluate their poten-
tial impact on human health. The first
research phase, led by Rodney Weber
of Georgia Tech, is to define the appro-
priate analytical measurement and risk
evaluation methodologies for character-
izing and assessing particle and chemi-
cal emissions from 3D printing technol-
ogies. The second phase, conducted by
The Rollins School of Public Health at
Emory, will assess potential health haz-
ards from exposure to the emissions.
ul.com,
gatech.edu,
emory.edu.
UNIQUE SYSTEM PRINTS
TRANSPARENT GLASS
Researchers at Massachusetts In-
stitute of Technology, Cambridge, have
developed the ability to print optically
transparent glass objects. A major ob-
stacle to accomplishing this task is the
extremely high temperature needed
to melt the material. Others have used
tiny particles of glass, melded togeth-
er at a lower temperature via sinter-
ing. But such objects are structurally
weak and optically cloudy. In contrast,
the system developed at MIT produces
glass objects that are both strong and
fully transparent to light. Molten glass is
loaded into a hopper after being gath-
ered from a conventional glassblowing
kiln. When complete, the finished piece
must be cut away from the moving plat-
form on which it is assembled. In oper-
ation, the device’s hopper and a nozzle
through which the glass is extruded to
form an object are maintained at tem-
peratures of roughly 1900°F, far higher
than those used for other 3D printing.
The new process could allow unprec-
edented control over the glass shapes
that can be produced, including vari-
able thicknesses and complex inner
features. Additional work will focus on
the use of colors in the glass, which the
team has already demonstrated in lim-
ited testing.
web.mit.edu.
LLNL optical engineer Bryan Moran
makes an adjustment to the Large Area
Projection Micro Stereolithography ma-
chine. Courtesy of Steve Wampler/LLNL.
UL is coordinating research on 3D printer
emissions with Georgia Tech and Emory
University.
MIT’s glass 3D printing process.
Courtesy of Steve Keating.