
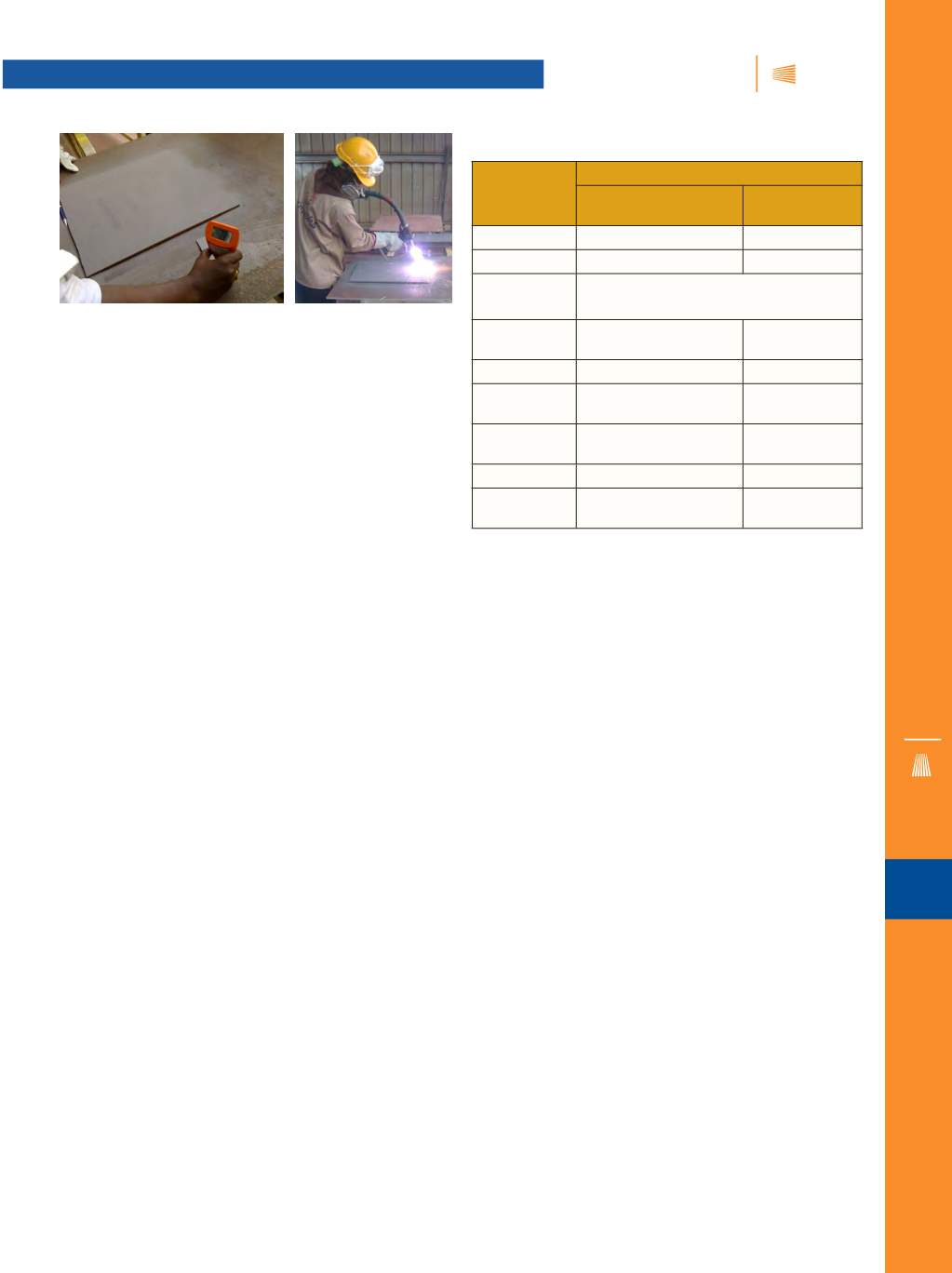
iTSSe
TSS
A D V A N C E D
M A T E R I A L S
&
P R O C E S S E S |
N O V E M B E R / D E C E M B E R
2 0 1 5
4 9
iTSSe
TSS
FEATURE ARTICLE
Fig. 2 —
Surface profile measurement.
Fig. 3 —
Thermal spray alu-
minum coating application
in progress on test panel.
CASE STUDY
A customer’s specifications for application and perfor-
mance of TSA coatings are listed in Table 1. Note that these
specifications are relatively stringent. Per the protective coating
requirements in this case, the following components were coat-
edwith TSAbut ran intopractical and technical difficulties in the
application process.
All structural parts in the -3 to 6 m MSL range including
jacket structures, jacket legs, braces, nodes, conductor guide
framing, launch trusses, mud mat risers, boat landings, barge
bumpers and guides, riser clamps, boat fenders, stairways and
cross supports, sump cassion/pump, and cassions were coated
with TSA by twin arc spray. This method was selected due to its
anticipated quality in the most susceptible and critical zone.
Successful implementation of TSA depends on several fac-
tors, and both relative humidity and dew point can affect coat-
ing quality. In very humid environments, blast cleaned steel
may re-rust or exhibit a rust bloommore rapidly than under nor-
mal ambient conditions. Thermal spray coatings should never
be applied after rust bloom appears on the surface. Because of
this, the ambient temperature is required to be at least 3°C (5°F)
above the dew point. As in painting, surface preparation is the
most crucial part of the TSA coating process. Pre-blasting and
blasting operations should be carefully monitored.
Pre-blasting operations include grinding of sharp edges,
fillets, corners, and welds, washing weld flux and residues with
clean water, and removing oil and grease contamination per
SSPC/SSPM Volume 2, grade SP1. Blasting should be done with
abrasives that are dry, clean, and free from contaminants
[5]
. In
addition, surfaces to be coated should be clean, dry, free from
oil/grease, and have the specified roughness and cleanliness
when the first coat is applied. The blasted surface should be
coated within four hours after blasting. The surface finish needs
to be minimum white metal (SSPC SP 5) with a sharp anchor
profile greater than 63
μ
m
[5]
.
Proper technique is critical to the success of thermal spray
coatings. Poor spray technique may result in early coating fail-
ure due to poor coating adhesion or de-cohesion, excessive
coating porosity, or high oxide content. Poor spray technique
may also result in highly variable coating thicknesses, including
areas that are deficient. It is essential to engage skilled opera-
tors and experienced applicators.
The spray pattern, stand-off distance, and spray angle are
the most important factors and should be continuously moni-
tored during arc spray. Each type and source of thermal spray
equipment should be set up and operated in accordance with
the manufacturer’s recommended procedures. Spray parame-
ters should be optimized primarily for coating quality and sec-
ondarily for production rate. With respect to these parameters,
the operations sequence is as follows:
1. Preparatory
•
Blasting media (16-24 mesh size)
•
Blasting air (no dust or oil)
•
Comparator-test sample of 18 × 18 in.
•
Mandatory for every shift or applicator: Sample of
50 × 150 × 1.3 mm thick sheet for bend test
•
Degreasing agent (per SSPC SP1)
•
Al wire purity
•
Calibrated inspection gadgets
•
Certified operators and inspectors
•
SHE considerations
2. Surface preparation
•
Inspection: Surface temperature >10°C, relative hu-
midity (<85%), dew point (>3°C), blasting media (20-40
mesh size garnet) for oil and salt content, blasting air
for oil and contamination (less than 20 µg/cm
2
)
•
Degreasing inspection: Surface grade, presence of oil
and grease
•
Blasting inspection: Surface finish (SA3), surface profile
(>65
μ
m) angular sharp profile is preferred to extent of
90-100 microns, surface contamination (Rating 2), salt
content (Bresle patch, less than 10 Kg/cm
2
)
TABLE 1—SUMMARY OF REQUIREMENTS FOR TSACOATINGS
Spray
parameters
Methods of Application
Arc wire spray
Flame wire
spray
Arc voltage
27 V
—
Air pressure
60–80 psi
60–80 psi
Steel surface
cleanliness
NACE-1 white metal/SSPC-SP5 or
NACE-2 near white metal/SSPC-SP10
Steel surface
profile
65
µ
m (min.)
65
µ
m (min.)
Arc current
150 A0200A
—
Coating
adhesion
225
µ
m (nominal)
225
µ
m (nominal)
Coating
Porosity
>2000 psi (total coatings)
>4000 psi (initial body coat)
>1000 psi
Spray distance
6–8 in.
5–7 in.
Spray pass
width
1.5 in. (40 mm)
0.75 in. (20 mm)
7