
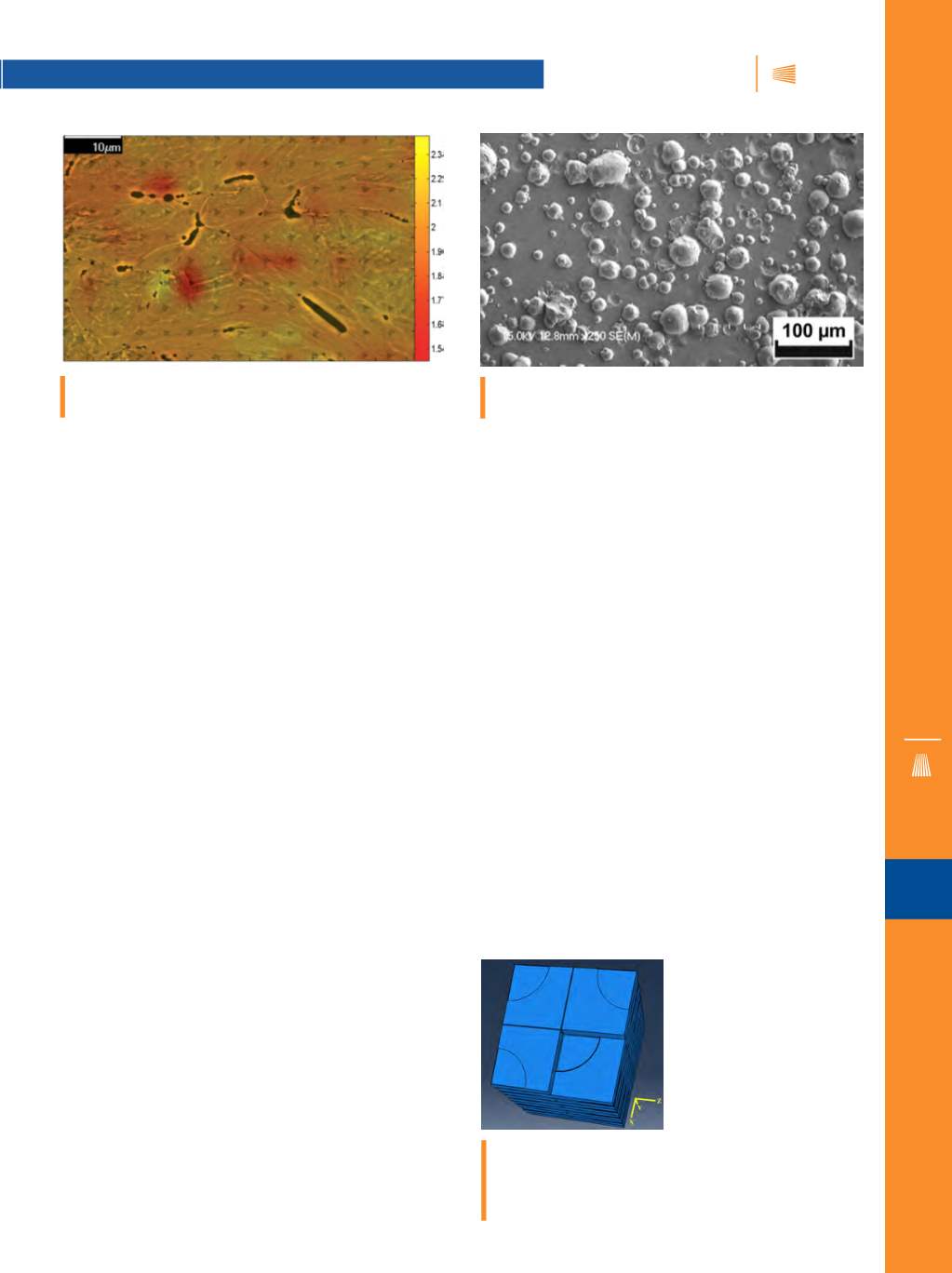
iTSSe
TSS
A D V A N C E D
M A T E R I A L S
&
P R O C E S S E S |
N O V E M B E R / D E C E M B E R
2 0 1 5
5 3
iTSSe
TSS
11
JTST
HIGHLIGHTS
state thermomechanical processing of predominantly mar-
tensitic feedstock powders. During deposition, these powders
undergo high strain rate deformation, leading to shear band
induced transformation of martensitic grains into nanoscale
martensite, equiaxed alpha structures, and nanostructured
alpha grains. The resulting microstructure evolution depends
on the magnitude and direction of shear undergone by the
particles. The specific structure and mechanism for forma-
tion of these regions is discussed in detail using nanohardness
mapping, scanning electron microscopy, and transmission
electron microscopy.
“INFLUENCE OF SUBSTRATE SURFACE OXIDE
FILM THICKNESS ON THE DEPOSITION
BEHAVIOR AND DEPOSITION EFFICIENCY
IN THE COLD SPRAY PROCESS”
Yuji Ichikawa and Kazuhiro Ogawa
Cold spray deposition accelerates particles by means of
a supersonic gas jet at a gas temperature that is usually low-
er than the melting point of the powder material, solving ox-
idation and phase transformation problems. Accordingly, it is
expected that an alternative technique of MCrAlY coatings is
used for high-temperature oxidation and hot corrosion protec-
tion. Thus far, MCrAlY coatings havebeendepositedby thermal
spraying techniques (e.g., LPPS or HVOF). Cold spray deposi-
tion for MCrAlY coatings has been demonstrated and, while
the mechanism of this process has been studied with various
approaches, it is not yet completely understood. A previous
study shows that a nascent surface created during the high-
velocity impingement of particles affects the deposition pro-
cess. Large scale plastic deformation of the metallic substrate
and particles easily occurs during impact. In contrast, covered
thin oxide films cannot deform plastically. Unfollowable large
plastic deformation breaks the oxide film. During this defor-
mation process, the native oxide film on the substrate disin-
tegrates; subsequently, the newly formed surface may cause
direct contact and initiate deposition. Therefore, the surface
oxide layer is expected to affect the quantity of generating
newly formed surface formation and consequently the cold
spray deposition process. Clarification of the oxide film influ-
ence for deposition phenomenon is beneficial for understand-
ing the depositionmechanism. Moreover, it is invaluable in the
decision of spray condition optimizing and pretreatment.
“RELATIONSHIP BETWEEN LAMELLAR
STRUCTURE AND ELASTIC MODULUS OF
THERMALLY SPRAYED THERMAL BARRIER
COATINGS WITH INTRA-SPLAT CRACKS”
Guang-Rong Li, Bo-Wen Lv, Guan-Jun Yang, Wei-Xu Zhang,
Cheng-Xin Li, and Chang-Jiu Li
The elastic modulus of plasma-spray top coatings plays
an important role in the thermal cyclic lifetimeof thermal-spray
thermal barrier coatings (TBCs) because thermal stress is de-
termined by the substrate/coating thermal mismatch and the
elastic modulus of the top coating. Consequently, it is critical
to understand the relationship between the elastic modulus
and lamellar structure of the top coating. However, neglecting
the intra-splat cracks connected with inter-splat pores often
leads to poor prediction in the in-plane modulus. In this study,
a modified model taking account of intra-splat cracks and
other main structural characteristics of plasma-sprayed yttria-
stabilized zirconia (YSZ) coatings was proposed. Based on es-
tablishing the relationship between elastic modulus and struc-
tural parameters of the basic
unit, effects of structural pa-
rameters on the elastic modu-
lus of coatings were discussed.
Predicted results are consis-
tent with experimental data on
coating the elastic modulus in
both out-plane direction and
in-plane direction. This study
benefits the further comprehen-
sive understanding of the failure
mechanism of TBCs in thermal
cyclic conditions.
Nanohardness in GPa shown as 2D heat maps overlaid on
microstructures for nitrogen sprayed sample C1.
Morphology of substrates observed at center of sprayed region,
deposited particles on mirror-polished substrate.
Structural model of this
study: The reverse side of
uniformdistribution with
one part missing.