
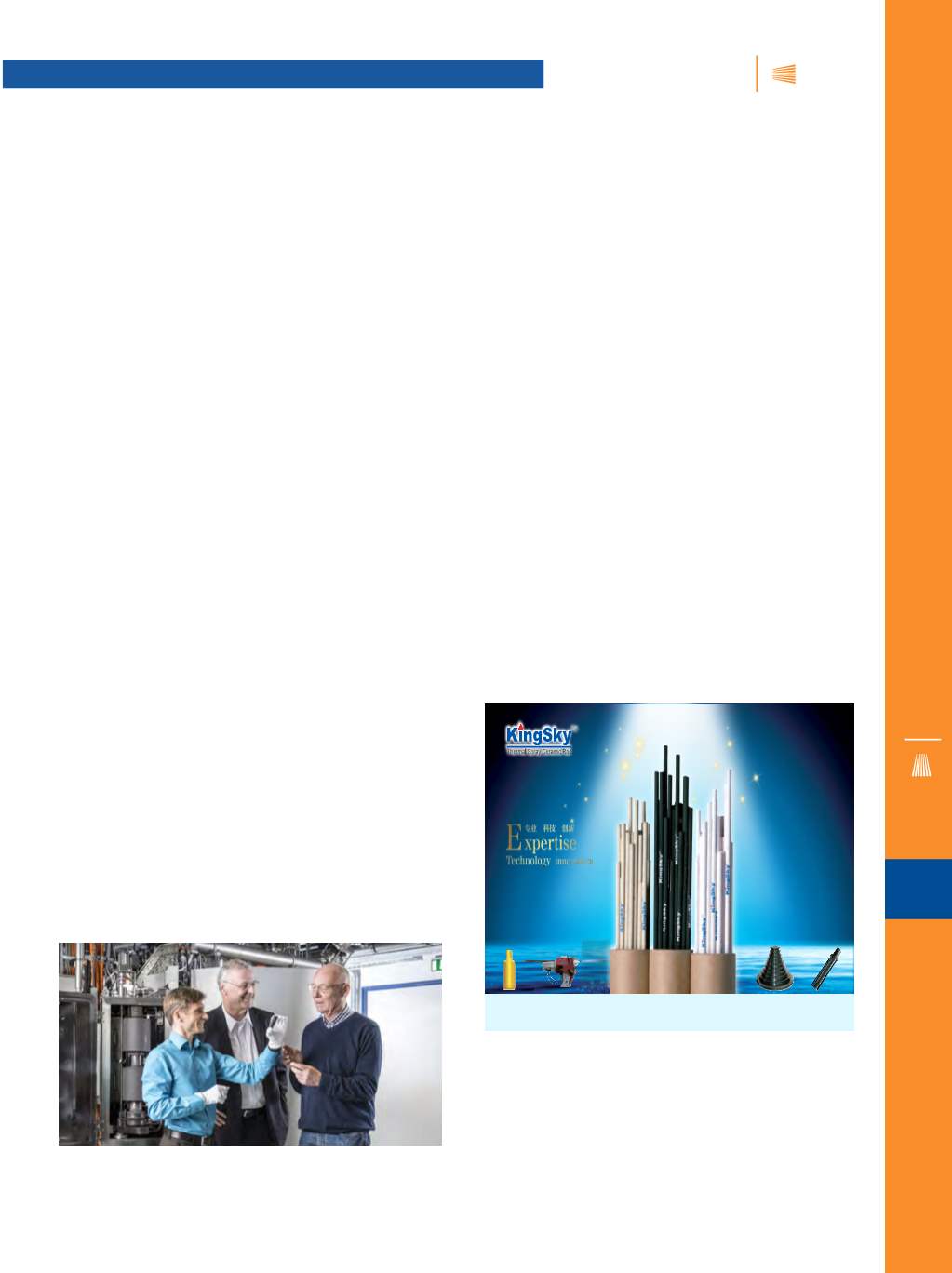
iTSSe
TSS
A D V A N C E D
M A T E R I A L S
&
P R O C E S S E S |
N O V E M B E R / D E C E M B E R
2 0 1 5
5 1
CASE STUDY
ENHANCED DIAMOND-LIKE COATINGS
BOOST FUEL EFFICIENCY
A new laser arc method is being used to apply a hard carbon
coating to engine components on the production line.
S
cientists already know how to coat components with
diamond-like carbon to minimize friction. But research-
ers at Fraunhofer Institute, Germany, have now devel-
oped a laser arcmethod that applies layers of carbon almost as
hard as diamond at high coating rates andwith high thickness-
es. By applying the carbon coating to engine components such
as piston rings and pins, fuel consumption can be reduced.
“Systematic application of our new method could save
more than 100 billion liters of fuel each year over the next 10
years,” says Andreas Leson, a professor at the Fraunhofer Insti-
tute for Material and Beam Technology IWS.
Although carbon-based coatings are already used in vol-
ume production, the Fraunhofer teamsucceeded in producing
hydrogen-free ta-C coatings on an industrial scale with con-
sistent quality. These tetrahedral amorphous carbon coatings
are significantly harder and thus more resistant to wear than
conventional diamond-like coatings. “Unfortunately, you can’t
just scrape off diamond dust and press it onto the component.
So we had to look for a different method,” says teammember
Hans-Joachim Scheibe.
PULSED LASER CONTROLS LIGHT ARC
In a similar style to old-fashioned film projectors, the
laser arc method generates an arc between an anode and a
cathode (the carbon) in a vacuum. The arc is initiated by a la-
ser pulse on the carbon target. This produces a plasma made
of carbon ions, which is deposited as a coating on the work-
piece in the vacuum. To run this process on an industrial scale,
a pulsed laser is vertically scanned across a rotating graphite
cylinder as a means of controlling the arc. The cylinder is con-
verted evenly into plasma due to the scanning motion and
rotation. To ensure a consistently smooth coating, a magnetic
field guides the plasma and filters out any dirt particles.
Fig. 1 —
Volker Weihnacht, Andreas Leson, and Hans-Joachim
Scheibe (left to right) developed a new laser arc method of depos-
iting friction-reducing, wear-resistant coatings on components.
Courtesy of Dirk Mahler/Fraunhofer.
Ningbo KingSky Thermal Spray Ceramic Rod Co., Ltd Ningbo Kingsky Thermal Spray Ceramic Rod Co., Ltd Add: Cixi High-tech Industrial Park, Ningbo, China Skype:Kingsky-ceramicrod Phone: 86-18605745092 Tel: 86-0574-23708405 www.kingsky-ceramicrod.com E: kingsky-ceramicrod@hotmail.com Kingsky™A AluminumOxide 3/16" x 24"& 1/4" x 24" Kingsky™C ChromeOxide 3/16" x 24"&1/4" x24" Kingsky™AT AluminumTitanium 3/16" x 24"& 1/4" x24" Kingsky™Z ZirconiumOxide 3/16" x 24"& 1/4" x 24" Kingsky™ is one of China’s leading manufacturers and suppliers of thermal spray ceramic rod and thermal spray industrial coating services. Kingsky™ rods are available in many ceramic oxide compositions for a wide range of applications: Kingsky™ A (Aluminum Oxide) 3/16”x24” & 1/4”x24” Kingsky™ C (Chrome Oxide) 3/16”x24” & 1/4”x24” Kingsky™ AT (Aluminum Titanium) 3/16”x24” & 1/4”x24” Kingsky™ Z (Zirconium Oxide) 3/16”x24” & 1/4”x24” We welcome potential buyers to contact Edwin Tan for additional information at kingsky-ceramicrod@hotmail.com . Thanks!The laser arcmethod canbe used todeposit very thick ta-C
coatings up to 20
μ
m at high coating rates. “High coating thick-
nesses are crucial for certain applications—especially in the auto
industry, where components are exposed to enormous loads
over long periods of time,” says researcher Volker Weihnacht.
One of the early adopters of this promising technology is
BMW. The auto manufacturer is working intensively on indus-
trial-scale implementation of ta-C engine components in its
various vehiclemodels with the aimof reducing fuel consump-
tion. Leson views this as the first major step in using the laser
arc method to save resources. And as a motorcycle aficionado
himself, he sees another positive effect stemming fromthis de-
velopment. “The fact that our research is helping tomake mo-
torcyclingmore environmentally friendly easesmy conscience
every time I go for a ride,” he says.
iTSSe
For more information:
Andreas Leson, Fraunhofer Institute
for Material and Beam Technology IWS, 49.351.83391.3317,
Winterbergstr. 28, 01277 Dresden,
www.fraunhofer.de/en.html.9
iTSSe
TSS