
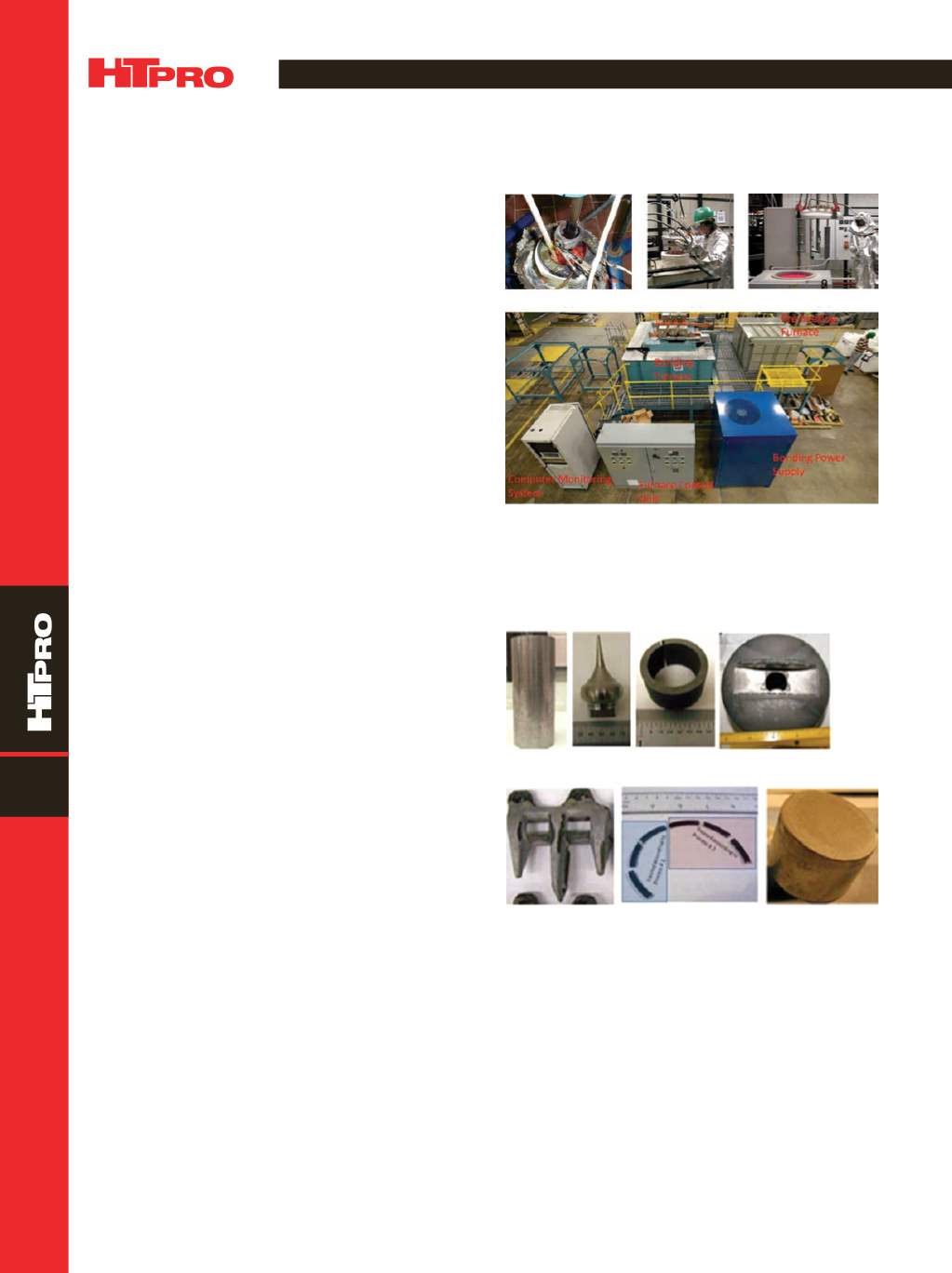
A D V A N C E D M A T E R I A L S & P R O C E S S E S | O C T O B E R 2 0 1 5
6 2
22
TECHNICAL SPOTLIGHT
ULTRAFAST BORIDING: A TRANSFORMATIONAL TECHNOLOGY
A
n ultrafast, efficient industrial-scale boriding process
can drastically reduce costs, increase productivity,
and improve the performance and reliability of a va-
riety of machine parts. Component surfaces are converted
into thick, hard boride layers in minutes, which dramatically
increases resistance to degradation due to wear, abrasion,
erosion, scuffing, and corrosion. By comparison, achieving
such layer thicknesses using traditional pack boriding re-
quires several hours, and surface hardness levels and other
properties are lower than those produced using the newpro-
cess.
The novel, environmentally friendly technology, devel-
oped at Argonne National Laboratory, Ill., enables treating
thousands of industrial components in one batch, without
creating solid or liquid waste and gaseous emissions. The
key ingredient used during boriding is a natural boraxminer-
al, which is safe to handle. Researchers say the new process
is a transformational technology that can complementmany
current surface treatment processes, such as conventional
boriding, carburizing, nitriding, carbonitriding, and physical
and chemical vapor deposition (PVD and CVD).
PROCESS DEVELOPMENT
The ultrafast, large-scale boriding process is the result
of a collaborative effort involving Argonne (lead partner),
Bodycote, and Istanbul Technical University, stemming from
a project fundedby theU.S. Department of Energy-Advanced
Manufacturing Office. The initial part of the project involved
scale-up of a small proof-of-concept unit (1.75-in. diameter
unit with 250-g electrolyte capacity) to 4- and 6-in. diameter
intermediate units, and then to a pilot-scale unit with a 22-
in. diameter crucible size featuring a capacity of 130 kg of
electrolyte. This led to building a production-scale unit with
a melt capacity of 4000 kg. The evolution of the large-scale
boriding technology from inception to large-scale imple-
mentation is shown in Fig. 1.
The ultrafast method uses a battery-like design, where
each electrochemical cell contains a positively charged cath-
ode, negatively charged anode, and molten borax-based
electrolyte. Bath temperature is roughly 1400°F. Parts are
attached to the cathode, and when the unit is connected to
a power source, ions flow from the anode to the cathode,
depositing boron on the cathode and attached workpieces.
Boron subsequently diffuses into the metal and reacts to
convert near-surface regions intometal borides. The process
is completed in minutes, producing a denser, more uniform
coating, and requires 85% less energy than conventional bo-
riding. Traditional pack-boriding, by comparison, involves
baking parts in a complex mixture of powders at a tempera-
ture around 1800°F, often for 10 hours or longer.
Ferrous and nonferrousmetals and alloys (e.g., titanium,
tantalum, zirconium, tungsten, niobium, molybdenum, most
nickel- and cobalt-base superalloys, and cobalt-chrome al-
loys), intermetallics, cemented carbides, and cermets (which
are not possible to treat using conventional boriding meth-
ods) can be treated with the new process. Surface hardness is
increasedby factorsof 3 to10 (i.e., 15 to45GPa), dependingon
the specific alloy. For example, a 300-
μ
mthick complex boride
layerwas formedonNi
3
Al intermetallicmaterial in15minutes,
Fig. 1 —
Evolution of boriding units: (a) initial (1.75 in. diameter),
(b) intermediate (4 and 6 in. diameters), (c) pilot-scale (22 in. di-
ameter), and (d) large-scale (43 in. long
×
57 in. wide
×
54 in. deep)
production units.
(a) (b) (c)
(d)
Fig. 2 —
Industrial parts treated using ultrafast boriding:
(a) engine piston pin, (b) titanium textile guide, (c) superalloy
bearing part, (d) Inconel 718 ball valve, (e) agricultural knife
guard, (f) engine piston ring, and (g) engine tappet.
(a) (b) (c) (d)
(e) (f) (g)