
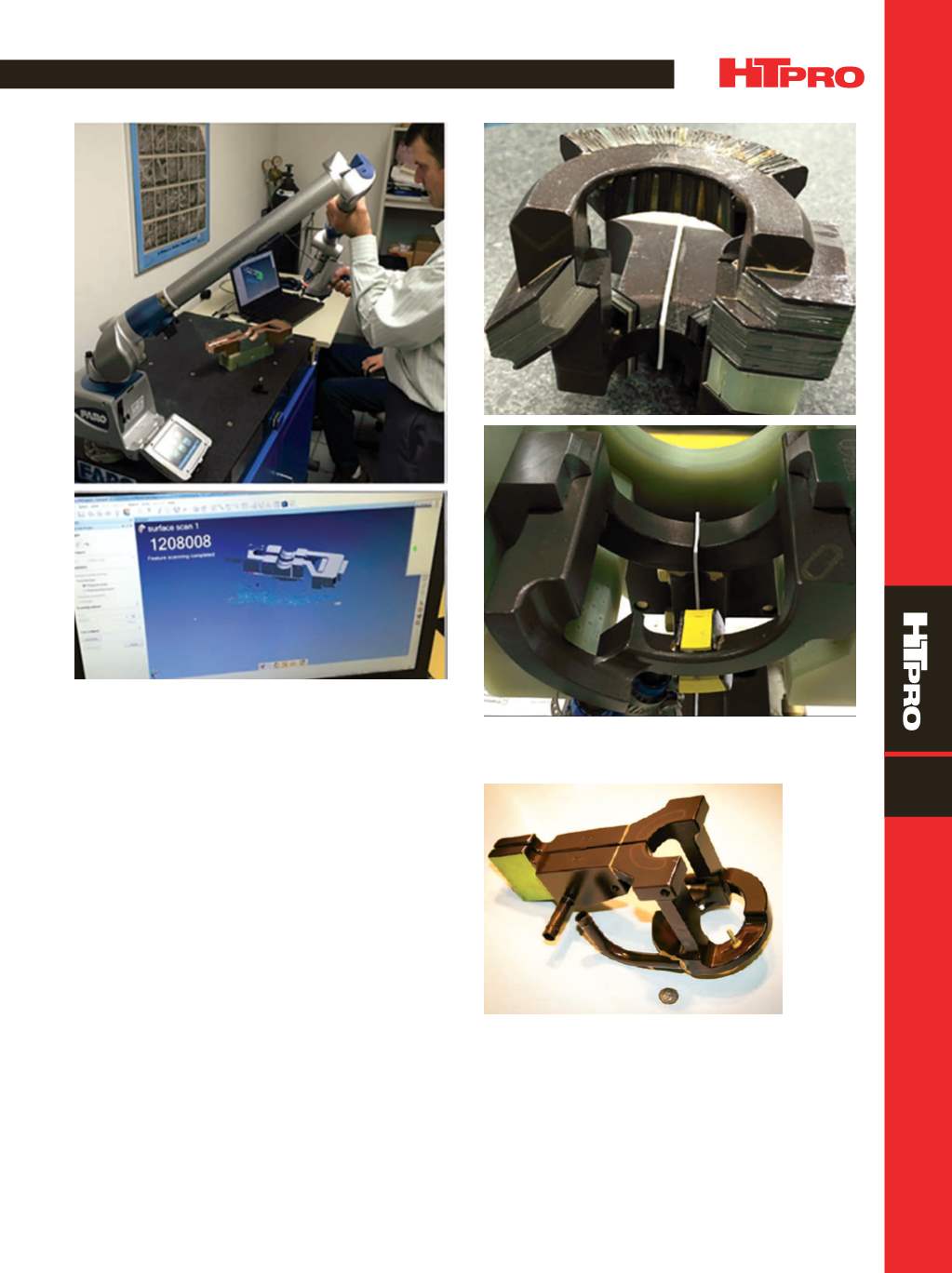
A D V A N C E D
M A T E R I A L S
&
P R O C E S S E S |
O C T O B E R
2 0 1 5
5 9
19
FEATURE
Fig. 3 —
A computerized 3Dmetrology laser scanner is used to
evaluate fabricated coils to ensure geometrical accuracy and
alignment, storing measurement data for inductor certification.
Conventionally fabricated single-shot inductors exhibit
high process sensitivity, which has a negative effect on the
repeatability of part heating and the quality of hardened
components. High sensitivity is associated with an electro-
magnetic proximity effect. A change in positioning of the
shaft inside the single-shot inductor due to bearing wear,
incorrect part loading in the inductor, and other factors pro-
duces an immediate variation of heating intensity, particu-
larly within the fillet region. This results in a local heat deficit
and therefore reduced hardness depth.
INDUCTOR BREAKTHROUGH
Inductoheat recently developed a new inductor design
(patent pending) that dramatically reduces localized coil
current density in areas prone to overheating and cracking
(Fig.5). The presence of a two-collar section reduces coil cur-
rent by one half, which dramatically reduces localized heat
generation in the copper and significantly extends coil life.
In addition, for a shaft positioned asymmetrically with-
in the inductor, there is a reduced heating effect produced
in one of the two half-collar sections that has an increased
Fig. 4 —
A magnetic flux concentrator is attached to certain areas
of the hardening inductor coil to enhance localized heat intensity.
Fig. 5 —
Novel inductor design (patent pending) dramat-
ically extends coil life in single-shot hardening of complex
shaft-like components.
inductor-to-shaft gap. This is offset by an increased induced
heating effect produced in the other half-collar section that
has a reduced inductor-to-shaft gap. Consequently, process
sensitivity associated with positioning the shaft within the
inductor is reduced over that with a conventionally designed
single-shot inductor.