
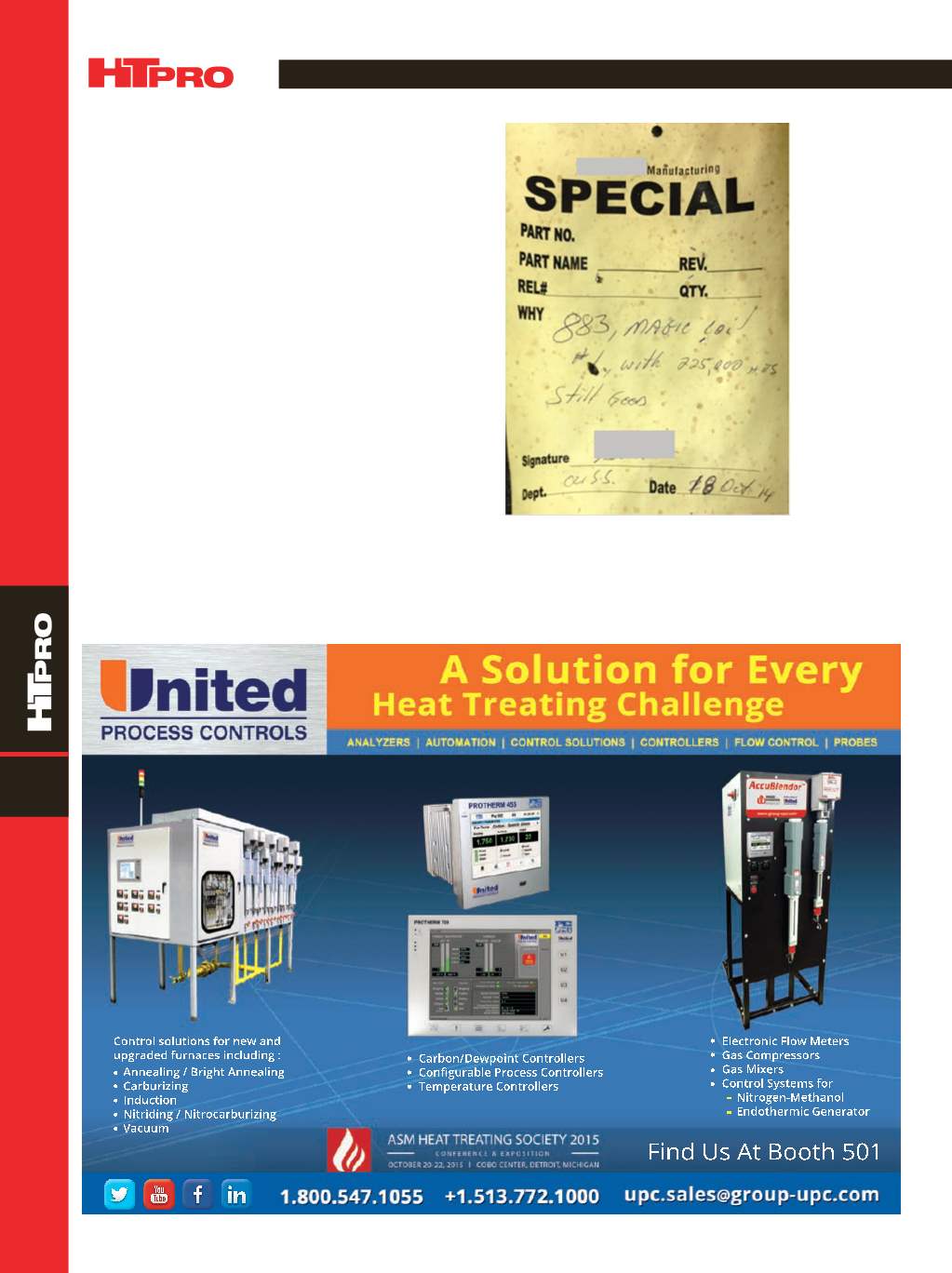
A D V A N C E D M A T E R I A L S & P R O C E S S E S | O C T O B E R 2 0 1 5
6 0
20
FEATURE
In one application of the new inductor, one of the
world’s largest suppliers of automotive parts achieved a
nine-fold increase in a single-shot coil life compared with
that for conventional inductors. This is verified by the man-
ufacturer’s tool-room tag showing that the inductor (which
the customer named “magic coil”) was still considered in
good shape after 225,000 heat cycles (Fig. 6). Other benefits
include measurable improvement in process robustness,
coil reliability, andmaintainability.
Portions of this article are adapted from the chapter
“Systematic Analysis of Induction Coil Failures and Preven-
tion” in
Induction Heating and Heat Treating
, Vol 4C,
ASM
Handbook
, V. Rudnev and G. Totten (Editors), ASM Interna-
tional, 2014.
Coil design details and benefits will be presented in a
paper at Heat Treat 2015, taking placeOctober 20-22 at Cobo
Convention Center in Detroit.
For more information:
Valery Rudnev, FASM, is director,
science and technology, Inductoheat Inc., an Inducto-
therm Group Co., 32251 N. Avis Dr., Madison Heights, MI
48071, 248.629.5055,
rudnev@inductoheat.com;
www.inductoheat.com.
Fig. 6 —
Automotive component manufacturer’s tool-room
tag indicates that Inductoheat’s newly designed inductor is still
considered in good shape after 225,000 heat cycles, a nine-fold
increase in single-shot coil life compared with that for conven-
tionally designed inductors.