
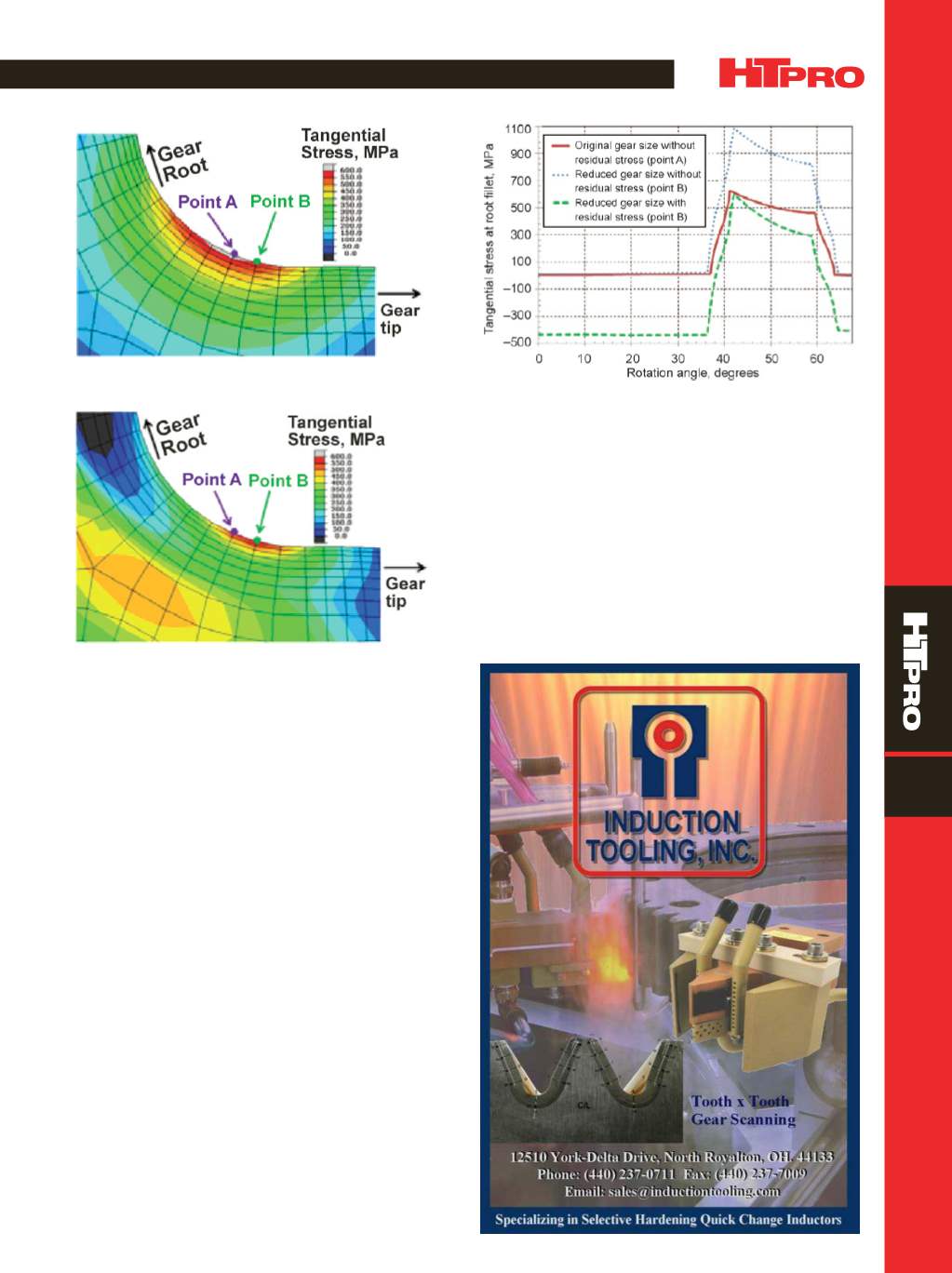
A D V A N C E D
M A T E R I A L S
&
P R O C E S S E S |
O C T O B E R
2 0 1 5
5 3
13
FEATURE
3. B. Ferguson and W. Dowling, Predictive Model and
Methodology for Heat Treatment Distortion, NCMS
Report #0383RE97, 1997.
4. T. Inoue and K. Arimoto, Development and
Implementation of CAE System “HEARTS” for Heat
Treatment Simulation Based on Metallo-Thermo
Mechanics,
J. Mater. Eng. Perform.
, Vol 6, p 51–60, 1997.
5. P. Carlone and G.S. Palazzo, Development and
Validation of a Thermo-Mechanical Finite Element Model
of the Steel Quenching Process Including Solid-Solid
Phase Changes,
Int. Appl. Mech.
, Vol 46, p 955–971, 2011.
6. M. Lusk, et al., On the Role of Kinematics in Constructing
Predictive Models of Austenite Decomposition,
Proc. of
TMS
, p 311–331, 2003.
7. D. Bammann, et al., Development of a Carburizing
and Quenching Simulation Tool: A Material Model for
Carburizing Steels Undergoing Phase Transformations,
Proc. 2nd Intl. Conf. on Quenching and Control of Distortion
,
p 367–375, 1996.
8. V. Warke, et al., FEA Model for Predicting the Response
of Powder Metallurgy Steel Components to Heat
Treatment,
Mater. Sci. Eng. A
, Vol 518(1–2), p 7–15, 2009.
9. Z. Li, et al., Data Needs for Modeling Heat Treatment of
Steel Parts,
Proc. Matls. Sci. & Tech. Conf.
, p 219–226, 2004.
For more information:
Zhichao (Charlie) Li, DANTE Solu-
tions Inc., 7261 Engle Rd., Suite 105, Cleveland, OH 44130,
charlie.li@dante-solutions.com,
www.dante-solutions.com.
Fig. 7 —
Tangential stresses along root fillet under torsional load
of 3287 Nm. (a) Case 1—original gear size without heat treatment
residual stresses, and (b) Case 2—reduced gear size with heat
treatment residual stresses.
(a)
(b)
Fig. 8 —
Comparison of tangential stresses at root fillet during
rotation under torque load.