
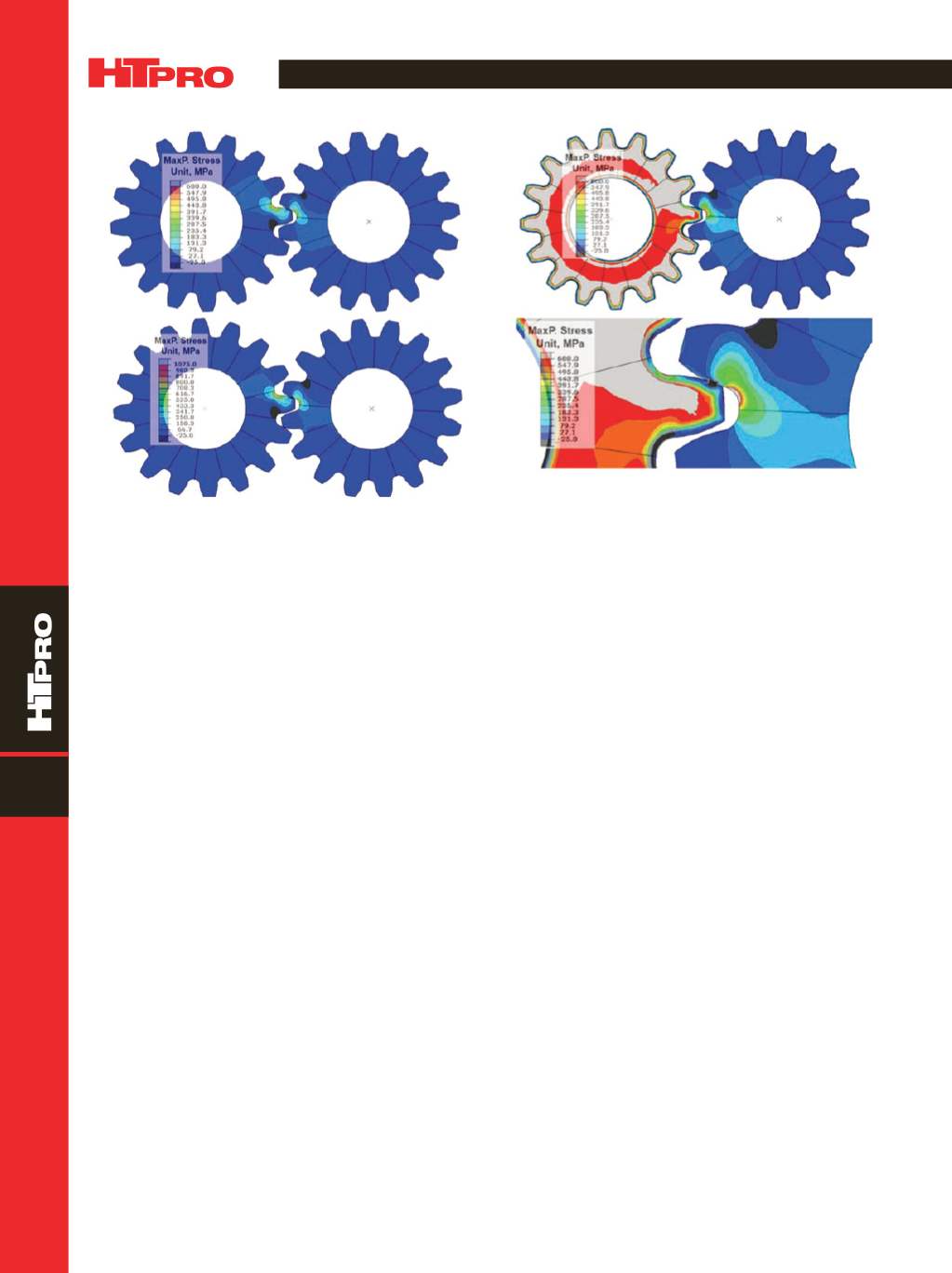
A D V A N C E D M A T E R I A L S & P R O C E S S E S | O C T O B E R 2 0 1 5
5 2
12
FEATURE
DISCUSSION
Carburizing and oil quenching the 8620 steel gear in-
troduces compressive residual stresses in the gear surface,
which significantly reduces the magnitude of actual stresses
at the root fillet under torsional load. Using the local cylindri-
cal coordinate system described in Fig. 4b, predicted actual
stresses in the tangential direction of the root fillet under the
same torsional load of 3287 N·m are compared for the fol-
lowing three cases:
Case 1: Original gear size (4340 steel) without residual
stresses from heat treatment
Case 2: Reduced gear size (8620 steel) with residual
stresses from carburization and oil quench
Case 3: Reduced gear size (4340 steel) without residual
stresses from heat treatment
For Case 1, the highest stress at the root fillet is about
625 MPa, located at point A (Fig. 7a). For Case 2, the highest
stress is reduced to 600 MPa, and is located at point B, as
shown in Fig. 7b, moving slightly from the root toward the
gear tip, which is due to the nonuniformcompressive residu-
al stress at the root fillet. The combination of residual stress-
es and the applied stresses is shown in Fig. 7b. Based on the
logic described above, the benefit of compressive residual
stresses to fatigue performance is further improved by op-
timizing gear geometry and heat treatment, so the highest
applied tensile stress locationmatches the highest compres-
sive residual stress location after heat treatment.
During rotational bending, the history plot of tangen-
tial stresses at the most critical positions (points A and B in
Fig. 7) of the root fillet are compared in Fig. 8 for the three
cases. Either point A or B is used depending on which loca-
tion has the highest actual stress under load. Peak stress is
considered the main driver of bending fatigue failure. The
comparison shows the significant effect of compressive sur-
face residual stresses on bending fatigue performance.
CONCLUSIONS
The selection of gear material and heat treatment pro-
cess is critical to bending fatigue performance. Carburizing
and oil quenching gears made of a carburizing steel grade
generates compressive residual stresses in the surface of the
hardened case. These stresses benefit the high cycle bend-
ing fatigue performance of gears. The concept is validated
by both modeling and previous experiments. In this study,
the concept is further applied to reduce gear size without
reducing its torque load capacity. A mass or volume reduc-
tion of 44% is compensated for by taking advantage of the
compressive residual stresses generated by heat treatment.
Material selection is also critical; clean material is preferred
to reduce potential crack initiation sites under the hard-
ened case, where residual tension exists to balance surface
compression.
References
1. A. Banka, et al., Applying CFD to Characterize Gear
Response during Intensive Quenching Process,
Proc. 24th
HTS Conf. & Expo
, p 147–155, 2007.
2. D. Lohe, et al., Residual Stresses and Fatigue Behavior,
Handbook of Residual Stress and Deformation of Steel
,
ASM International, p 27–53, 2002.
(a)
(b)
Fig. 5 —
(a) Maximumprincipal stress generated in root fillet of
gear under torsion load for (a) original size gear, and (b) reduced
size gear.
(a)
(b)
Fig. 6 —
(a) Maximumprincipal stress generated in root fillet of
gear under rotation bending load of reduced size gear (with heat
treatment residual stresses in the left gear), and (b) zoomed-in
contour of contact teeth.