
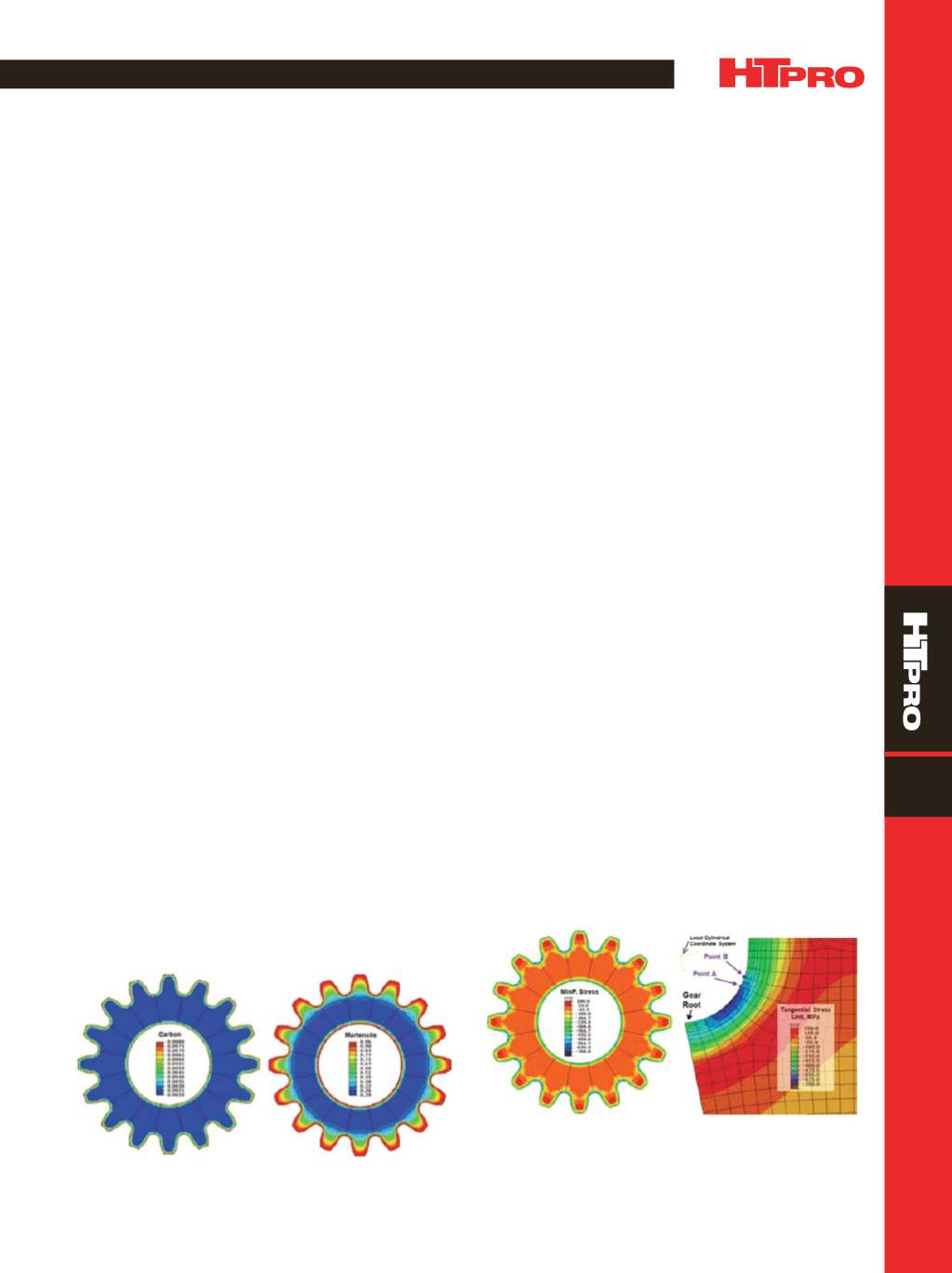
A D V A N C E D
M A T E R I A L S
&
P R O C E S S E S |
O C T O B E R
2 0 1 5
5 1
11
FEATURE
residual stresses is negligible. It is assumed that residual
stress from heat treatment of the original size gear is zero.
To reduce gear size, a combination of carburization and
oil quench is proposed to introduce compressive residual
stresses to the gear surface for improved bending fatigue
performance. AISI 8620 alloy carburizing grade was selected
as the gear material, with a 25% reduction in the
x
-
y
plane
while keeping the same axial dimension (Fig. 2b). Gear di-
mensions are 42 mm OD, 19 mm ID, 33 mm root diameter,
and 50 mm thick. The volume or mass of the smaller gear
is 56% that of the original gear, with the centerline distance
between the gear pair reduced proportionally to 77 mm.
MODELING HEAT TREATMENT
The smaller gear is gas carburized, followed by oil
quenching and low temperature tempering. The entire gear
surface is carburized using process conditions of 925°C for
8 hours, with a carbon potential of 0.8%.
Figure 3a shows the predicted carbon-distribution
(wt% C) contour. Predicted effective case depth (ECD) is
0.75 mm, assuming 0.4 wt% carbon as the threshold of ECD
definition. After carburization, the gear is cooled to 875°C in
the furnace, followed by oil quenching and tempering. Pre-
dicted martensite distribution is shown in Fig. 3b. The gear
tooth is mainly martensite, the core about 20% martensite,
and the remaining structure bainite. About 10% retained
austenite is predicted on the carburized surface of the as-
quenched gear prior to tempering.
Compressive residual stresses are generated in the gear
surface after quenching. Predictedminimumprincipal stress
is shown in Fig. 4a. Both bore and tooth surfaces are under
compression due to the delayed martensitic transformation
in the high carbon case. The root fillet has higher compres-
sive stress compared with that at the tooth flank region,
which is due to the stress concentration of the geometry ef-
fect during quenching.
The directions of minimum principal stresses vary
at different locations of the gear. Minimum principal
residual stress at the root fillet is in the tangential direction
after quench hardening. Tangential stress also directly re-
lates to fatigue crack initiation and propagation at the root
fillet. A local cylindrical coordinate system is defined to plot
the tangential stresses in the gear root fillet (Fig. 4b). The
center of the cylindrical coordinate systemmatches the cen-
ter of the gear fillet. The highest residual compression at the
fillet is about 700 MPa, close to the center of the root. Using
the local coordinate system, the stress contour close to the
root fillet represents tangential stress, but stresses in this di-
rection aremeaningless for locations far away from the fillet.
MODELING GEAR STRESSES UNDER LOAD
Using the rotational bending setup shown in Fig. 2,
stress evolution under a constant torque load of 3287 Nm
is modeled using a linear elastic model. The highest tensile
stress occurs at the root fillet during gear rotation. Without
considering residual stresses from the heat treatment, snap-
shots with the highest stress magnitude are shown in Figs.
5a and 5b for both gear pair sizes. Reducing the gear size by
25% in the
x
-
y
plane generates 1075 MPa tensile stress at the
root fillet compared with 600 MPa for the original size gear.
Compressive residual stresses introduced by heat
treating significantly benefits the gear’s high-cycle bending
fatigue strength. In this study, residual stresses from the
hardening process shown in Fig. 4 are imported to the tor-
sion load model. Under the same constant torque load of
3287 Nm, predicted maximum principal stress contour is
shown in Fig. 6. To more clearly show the effect of residual
stresses, the values are imported to the left (driven) gear
only. The highest stress generated at the surface of the root
fillet is slightly below 600 MPa, significantly lower than the
value of 1075 MPa without considering residual stresses.
From the contour plots shown in Fig. 6b, the highest stress
is under the surface. The location under the surface could
have a lower probability of crack initiation than that at the
surface, even with higher tensile stress.
(a) (b)
Fig. 3 —
Predicted distributions of (a) carbon, and (b) martensite
after hardening.
(a) (b)
Fig. 4 —
Distribution of residual stresses after carburization and
oil quench: (a) minimumprincipal stress (MPa), and (b) tangential
stress along the root fillet of gear using defined local cylindrical
coordinate system.