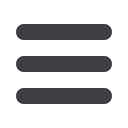
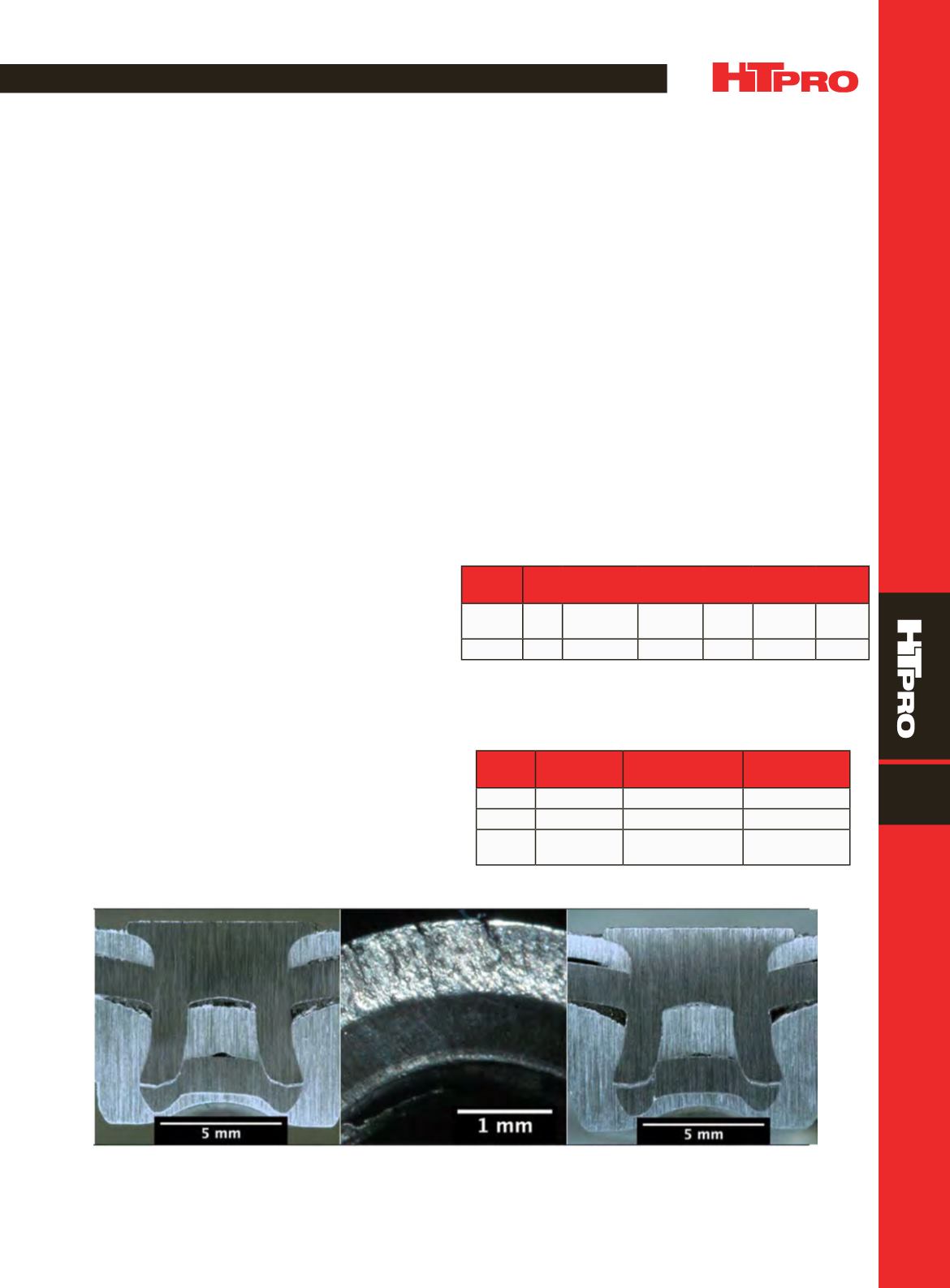
A D V A N C E D
M A T E R I A L S
&
P R O C E S S E S |
M A R C H
2 0 1 5
4 5
11
TECHNICAL SPOTLIGHT
Fig. 2 —
(a) Cross section of an aluminum-press-hardened steel-aluminum joint with a rivet tempered to a high hardness level; (b) bottom
view of rivet extracted from joint shown in (a), which indicates cracking in the rivet tail; and (c) cross section of an aluminum-press-hardened
steel-aluminum joint with a rivet tempered to a lower hardness level, where no rivet tail cracking occurred.
(a)
(b)
(c)
TABLE 1 —CHEMICAL COMPOSITION OF SELECT STEEL RIVETS
Steel
grade
Element, wt%
Fe C Mn Si Cr B
10B37 Bal 0.35–0.41 0.7–0.8 0.1
max 0.2–0.3 0.005
max
4340 Bal
0.41
0.73 0.29 0.84
…
joining press-hardened steel (1500 MPa tensile strength) to
6000 series aluminum. Joining high-strength steel requires a
rivet skirt hard enough to pierce the material, strong enough
to resist compressing and buckling, and ductile enough to
flare outwards at least 0.2 mmwithout cracking.
Thisapplicationrequiressufficientrivetcolumnstrength
andductility toprovide flaring into thebottomsheet to create
a strong interlock. The joint cross section in Fig. 2a shows that
if the rivet hardness is too high without the required ductili-
ty, fractures form on the periphery of the rivet tail. Fractures
are visible in the bottom view of the extracted rivet (Fig. 2b);
joints in which fractures occur in the rivet cannot be used in
automobiles. The cross section of a rivet (Fig. 2c) tempered to
obtain sufficient ductility to accommodate the flare without
forming fractures in the rivet tail shows that tempering also
reduces column strength, which can cause buckling when
piercing press-hardened steel. Development of a rivet ma-
terial that provides greater ductility at the required column
strength would enable the use of SPR technology for a great-
er range of high strength steel-to-aluminum joints.
New rivet materials also could simplify production.
Currently, dozens of rivet and die combinations are required
to join the wide range of different stack material combina-
tions in a vehicle body. A rivet with the necessary ductility
at strength levels that prevent buckling could simplify as-
sembly by reducing the total number of unique rivet and die
combinations and the associated robotic machinery. The
process of reducing the number of different combinations
to reduce cost and complexity is referred to as “
commoniza-
tion
.” In addition, in joints where a slightly longer rivet can be
used, selecting a rivet material with increased ductility could
enable achieving evenmore commonization. In joints where
higher ductility allows using a different rivet hardness, more
commonization benefits are realized by reducing the num-
ber of different rivet hardness levels.
Improved ductility at high rivet hardness would in-
crease possible SPR applications. Fractures on the periphery
of the rivet tail (Fig. 2a) are believed to develop froma tensile
hoop stress at the rivet tail that evolves during flaring. Alter-
native steel alloys and thermal processing techniques are
under investigation to provide improved ductility.
Prototype 4340 alloy steel rivets were evaluated in riv-
eting trials. The chemical composition of the 4340 alloy used
is provided inTable 1. Rivetsweremachined fromwire rodby
Henrob Corp., New Hudson, Mich., and heat treated to vari-
ous hardness levels under laboratory conditions. They were
inserted into a press-hardened steel and 6000 series alumi-
num sheet metal stack (Fig. 2) to evaluate the impact of im-
proved mechanical properties on rivet performance. Figure
3a shows a joint cross section containing a prototype rivet
tempered to a high hardness. Interlock distances for 10B37
rivets and prototype 4340 rivets are shown in Table 2. Initial
TABLE 2—CHARACTERISTICS OF 10B37 FORGED
RIVETSAND 4340 MACHINED PROTOTYPE RIVETS
Steel
grade
Hardness
(HV)
Interlock
distance, mm
Failure
mode
10B37
590
0.47
Tail fracture
10B37
550
0.62
Buckling
4340
595
0.64
None
apparent