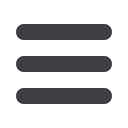
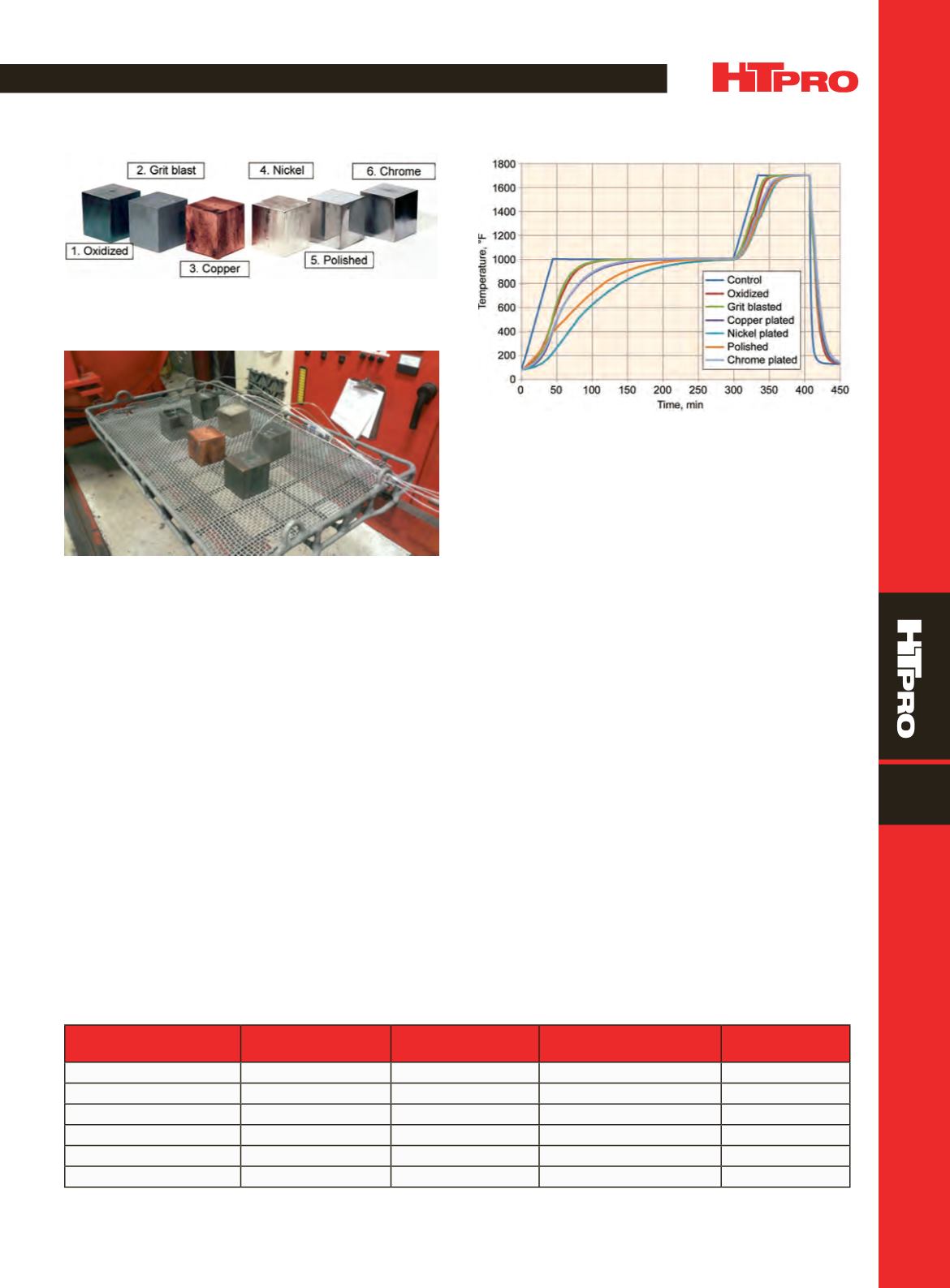
FEATURE
A D V A N C E D
M A T E R I A L S
&
P R O C E S S E S |
M A R C H
2 0 1 5
4 1
7
Fig. 1 —
Carbon-steel test blocks with different surface conditions
and emissivities used to determine heating times to temperature.
Fig. 2 —
Carbon-steel test blocks with inserted thermocouples
used to determine the effect of surface condition on times to heat
to temperature in a vacuum furnace.
Fig. 3 —
Effect of surface condition and corresponding emissivi-
ties on time to heat carbon-steel test blocks in a vacuum furnace.
TABLE 2— EFFECT OF SURFACE CONDITION AND EMISSIVITY ON TIME
TO HEAT CARBON STEEL TEST BLOCKS IN VACUUM FURNACE(a)
Surface condition
Approximate
emissivity
Heating time to
1000
°
F, min
Heating time from
1000
°
to 1700
°
F, min
Total heating
time, min
Grit blasted
0.75–0.80
111
49
160
Oxidized
0.80–0.95
114
54
168
Chromium plated
0.20–0.40
152
68
220
Copper plated
0.04–0.57
168
68
236
Polished
0.12–0.40
241
74
315
Nickel plated
0.045–0.08
264
75
339
(a) 2.5 in. cubes with different surface conditions
1. Pump furnace down to initial vacuum of less than
1 × 10
-3
torr
2. Heat furnace to 1000
o
F at 15
o
F per minute
3. Hold at 1000
o
F until all blocks are within 10
o
F of set
point and hold 15 minutes
4. Heat furnace to 1700
o
F at 15
o
F per minute
5. Hold at 1700
o
F until all blocks are within 10
o
F of set
point and hold 15 minutes
6. Cool load and furnace back to unloading temperature
Figure 3 shows the plots of thermocouple readings as a
function of time. The curves illustrate the important role that
emissivity or absorptivity plays relative to heating materials
in a vacuum furnace. Table 2 shows the effects of emissivity
and surface condition on heating time for the same part size.
Carbon steel blocks of the same size can take up to twice the
time to heat to temperature, depending on surface condition.
The approximate emissivity value of the surface condition is
closely reflected in the relative heating times. This informa-
tion enables predicting relative heating rates for different sur-
face conditions and their respective emissivity values (Fig. 4).
EFFECTS OF TEST BLOCK MASS
AND CROSS SECTION
A second series of test blocks was used to further
demonstrate the importance of correct cross section and
surface condition in thermocouple test blocks. Pairs of three
different block sizes (1, 1.75, and 2.5 in. cube) consisted of
polished and oxidized blocks.
Dummy blocks were loaded into a workbasket similar
to that described above (Fig. 5), and the workbasket was
placed into the furnace. Process cycle steps were as follows:
1. Pump furnace down to initial vacuum of less than
1 × 10
-3
torr
2. Heat furnace to 1150
o
F at 15
o
F per minute
3. Hold at 1150
o
F until all blocks are within 10
o
F of set
point and hold 15 minutes