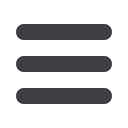
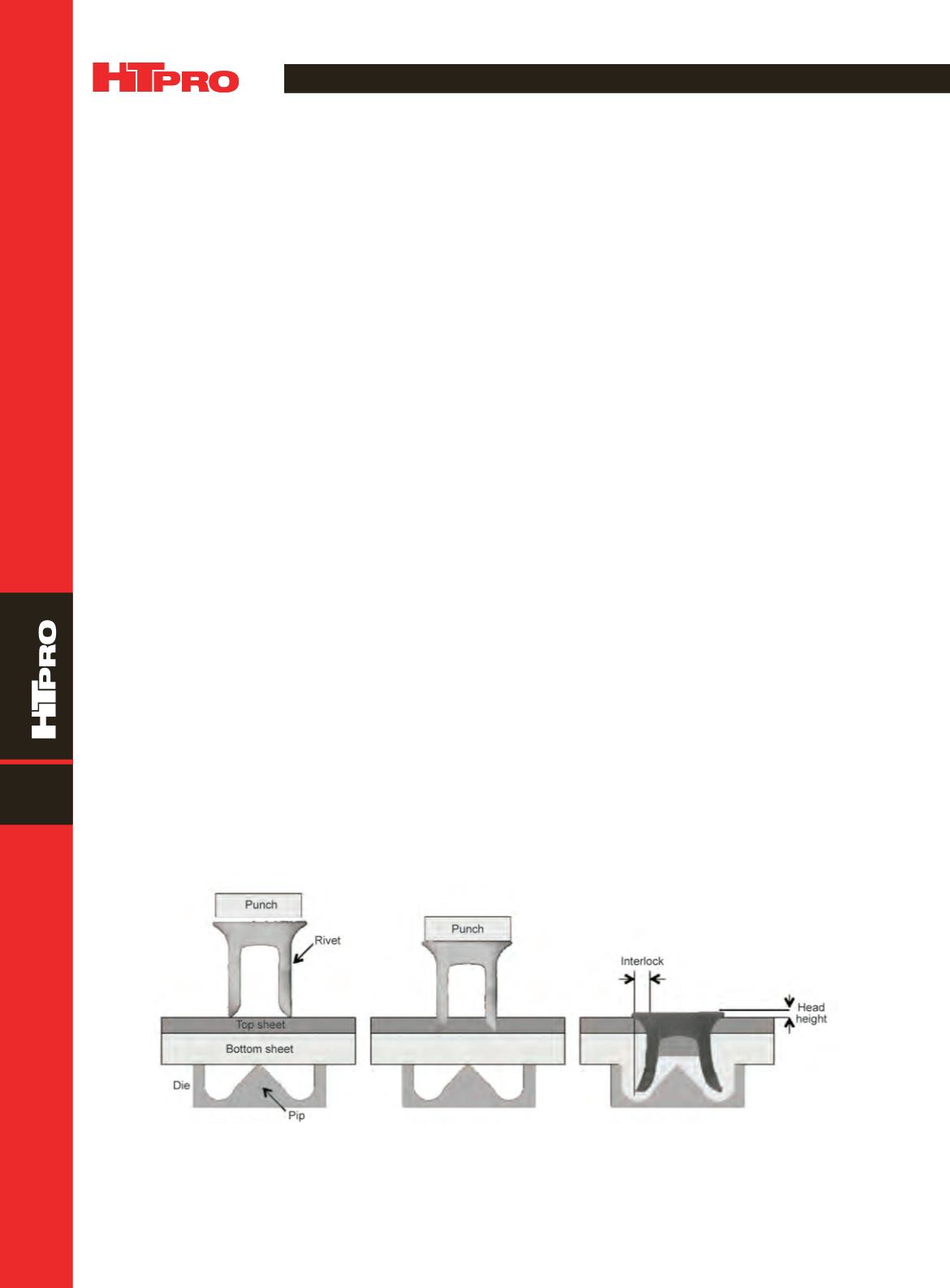
FEATURE
A D V A N C E D M A T E R I A L S & P R O C E S S E S | M A R C H 2 0 1 5
4 4
10
T CHNICAL SPOTLIGHT
by forcing (piercing) a semi or fully tubular rivet through top
sheet(s) using a robotically actuated C-frame containing
a servoelectric punch and opposing die. The die forces the
rivet to flare into the bottom sheet without perforating the
sheet, producing a significant interlock that provides joint
strength. The potential for corrosion isminimal because pre-
viously applied coatings are preserved in the process.
Joining steel and aluminum using SPR is well estab-
lished and widely used in the automotive industry. Increas-
ing interest in using very high-strength steel alloys for vehicle
construction offers an opportunity to extend the use of cur-
rent SPRby further developing rivetmaterial. SPR technology
can be applied to a wide range of materials using rivets with
different hardness levels depending on the application. For
example, rivets with low and medium hardness are used to
join soft materials, providing a large degree of flare, which
creates a largemechanical interlock (more than 0.4mm) that
resists rivet pull through and produces a strong joint. For join-
ing high-strength steels, only 0.2 mm of rivet flare is required
to resist rivet pull through and produce a strong joint.
RIVET MATERIAL DEVELOPMENT
Joining very high-strength steels requires using rivets
at the top end of the rivet-hardness scale and with improved
mechanical properties, which enable producing these chal-
lenging joints. Rivet development is of particular interest for
A
utomotive manufacturers are increasing their use of
high-strength steel with lightweight aluminum body
components to achieve stringent Corporate Average
Fuel Economy (CAFE) standards through weight reduction,
without compromising passenger safety and vehicle dura-
bility
[1]
. Joining aluminum to different materials by welding
presents challenges due to the formation of oxides and dif-
ferent material melting points
[2]
. However, it is possible to
produce joints with adequate strength and durability using
mechanical spot-joining methods, which enables using dif-
ferent material combinations in vehicle design.
SELF-PIERCE RIVETING
One mechanical spot joining technique of particular
interest is self-pierce riveting (SPR), which is used in the con-
struction of the 2015 Ford F-150 pickup truck
[3]
. SPR provides
a robust joint, which often outperforms clinching and spot
welding under both static and fatigue conditions, while pro-
viding fast cycle times, zero waste, and the ability to join dif-
ferent material combinations
[4]
.
Rivets used in automotive applications are cold forged
from a range of steel wire alloys. AISI 10B37 is one of the
most widely used grades (Table 1). Rivets are heat treated to
achieve a fully martensitic microstructure, which provides
the high strength required for a successful joint. A schematic
of the joining process is shown in Fig. 1. The joint is formed
ADVANCINGSELF-PIERCERIVET TECHNOLOGY
THROUGHALLOYDEVELOPMENT
Stephen Van Hall and Kip Findley,*
Colorado School of Mines, Golden
*Member of ASM International
Fig. 1 —
Schematic showing the SPR process of joining two sheet materials: (a) Setting stack up, (b) piercing the top sheet, and (c) flaring
into bottom sheet. Joint strength is provided by the mechanical interlock between the rivet and top sheet.
(a)
(b)
(c)