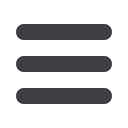
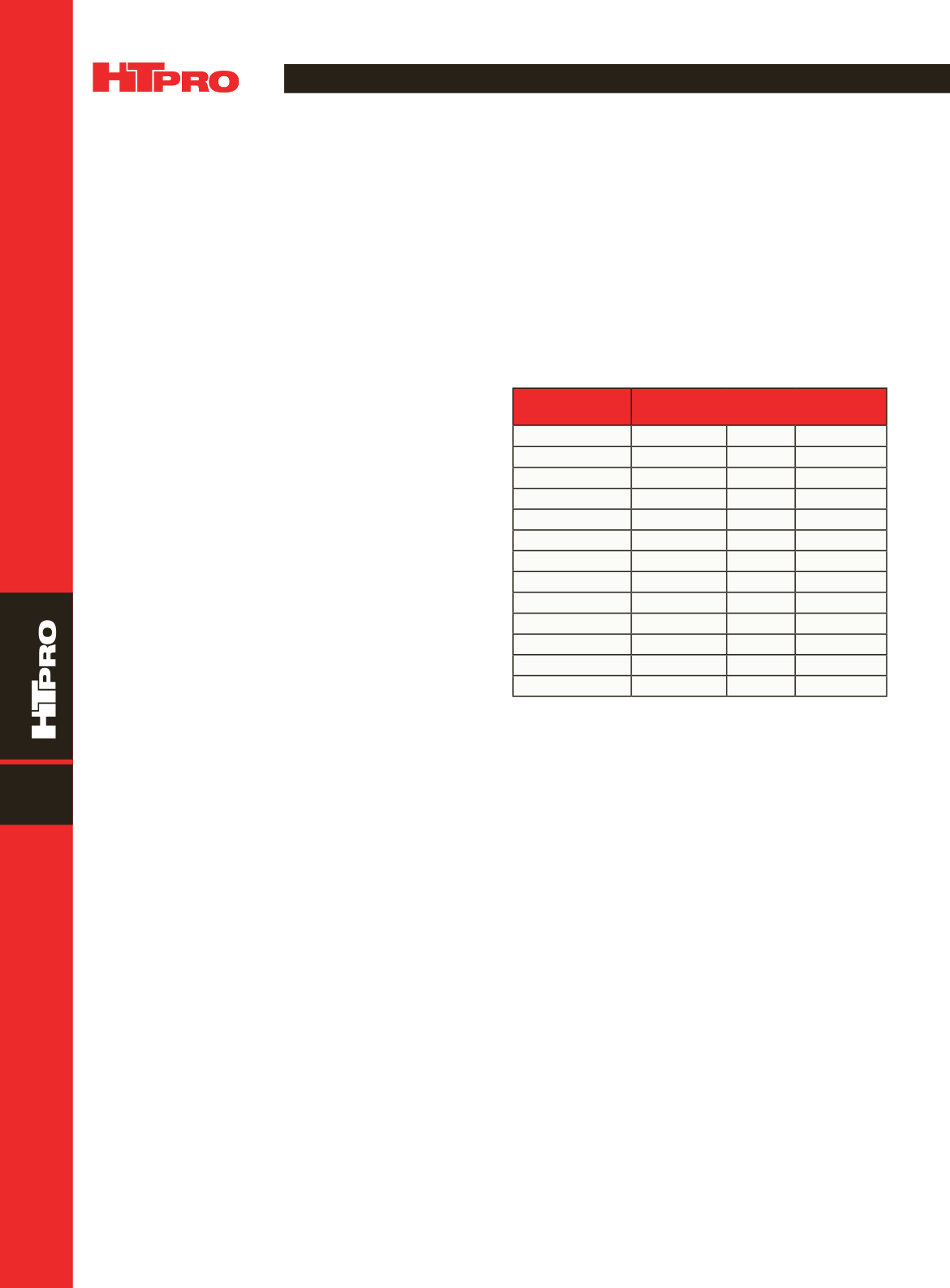
FEATURE
A D V A N C E D M A T E R I A L S & P R O C E S S E S | M A R C H 2 0 1 5
4 0
6
USINGWORKLOAD-EMISSIVITYFACTORSTOPROJECT
HEATINGRATES INAVACUUMFURNACE
Emissivity is a term used to define the ability of a surface to emit and absorb radiation.
At any given temperature, the emissivity of a body (or surface) equals its absorptivity.
Reàl J. Fradette and Trevor Jones,*
Solar Atmospheres Inc.
D
evelopment work on a vacuum carburizing process
revealed the need to better understand the effect of
workload surface emissivity and the proper use of
dummy thermocouple test blocks. The process involved car-
burizing areas of a partially copper-plated alloy steel part;
areas of the part that were not to be carburized were cop-
per plated. Because part configurationmade it impossible to
place a thermocouple inside, a dummy test block made of
carbon steel with approximately the same cross section as
the workpiece was used for the process thermocouple with-
out proper consideration (as determined subsequently) of
the test block surface.
Using the test block as the control, carburizing was
initiated when it reached the predetermined temperature.
Examination of the part at the end of the test showed that
the depth of carburized case was shallow in areas that were
not plated. This indicated that the carburizing cycle did not
hold the part at the correct temperature long enough before
carburizing. Thus, it was concluded that when using dummy
test blocks to control process times and temperatures, many
factors must be considered including surface emissivity. This
led to evaluating the effects of surface condition and work-
piece size on emissivity and time to heat to temperature.
PART SURFACE EMISSIVITY
In a vacuum furnace, heat is imparted to a workload
via radiation from the furnace heating elements. In practice,
most materials and surfaces are “gray bodies,” having an
emissivity factor less than 1.0. For practical purposes, it is
assumed that a good reflector is usually a poor absorber.
The surface condition of amaterial can greatly affect its
ability to absorb radiant energy. To heat the same material
with equal cross section and mass to final temperature can
take up to twice as long, depending on surface condition. Ta-
ble 1 shows the approximate emissivities of various metals
and surface conditions.
In vacuum furnace heating, several complex factors af-
fect the total time it takes for materials to reach uniformpro-
cess temperature, including load weight, part cross section,
and heating rate. As stated previously, emissivity is also an
important factor directly affecting the heat absorption capa-
bility of the material being processed.
Knowing the emissivity of a material is most critical
when using separate dummy thermocouple blocks to sim-
ulate actual workload temperature. The thermocouple
block must not only represent the average cross section of
parts, but also must represent the surface condition (color,
roughness, or amount of oxidation) of the material being
processed.
TEST PROCEDURE
To illustrate the importance of the emissivity factor in
load heating and dummy thermocouple blocks, six carbon
steel blocks with different surface conditions were prepared
for testing. Blocksmeasured 2.5
×
2.5
×
2.5 in., with a 0.093 in.
diameter hole drilled 1.25 in. deep at the center into which
a thermocouple was inserted. Block surface modifications
included oxidized, grit blasted, copper plated, nickel plated,
polished shiny, and chrome plated (Fig. 1).
Dummy blocks were loaded into a workbasket with
generous spacing between blocks and relatively equal dis-
tance from the heating elements. Thermocouples were
inserted into the blocks (Fig. 2), and the workbasket was
placed into the furnace. Process cycle steps were as follows:
TABLE 1 — EFFECT OF SURFACE CONDITION
ON EMISSIVITY OF SELECT METALS
Metal
Surface condition
Polished Rough Oxidized
Aluminum
0.04
0.055 0.11–0.19
Brass
0.03
0.06–0.2
0.60
Chromium
0.08
--
0.17
Copper
0.018–0.02
--
0.57
Gold
0.018–0.035
--
--
Steel
0.12–0.40
0.75
0.80–0.95
Stainless steel
0.11
0.57
0.80–0.95
Lead
0.057–0.075 0.28
0.63
Nickel
0.045–0.087
--
0.37–0.48
Silver
0.02–0.035
--
--
Tin
0.04–0.065
--
--
Zinc
0.045–0.053
--
0.11
Galvanized iron
0.228
--
0.276
*Member of ASM International and Heat Treating Society