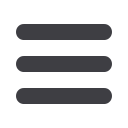
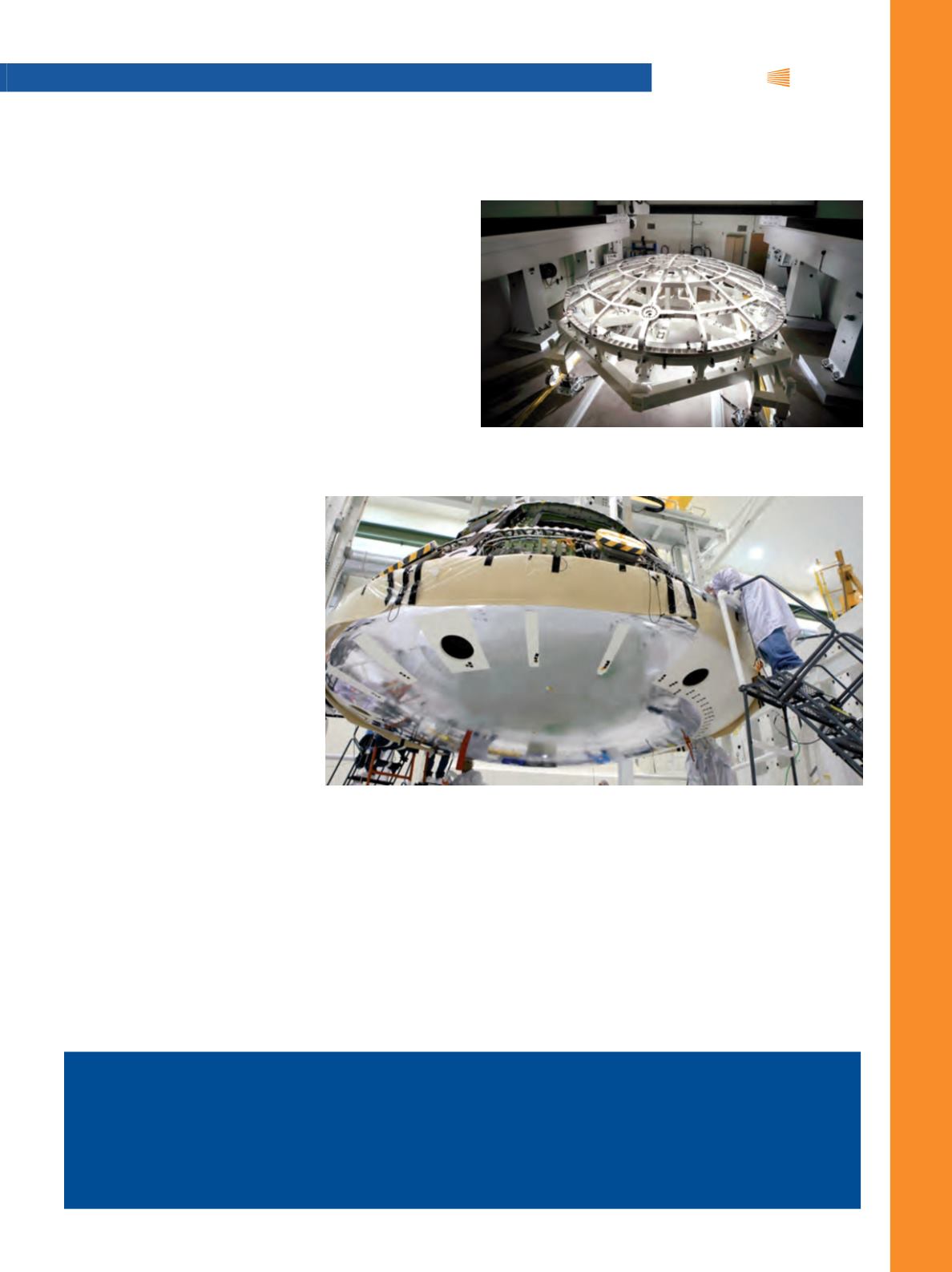
CASE STUDY
ORION HEAT SHIELD HANDLES extreme temps
H
ave you ever imagined how hot it would be at the
Earth’s core? What about stepping on molten lava?
The Orion spacecraft built by Lockheed Martin endured
those temperatures (and higher) when re-entering the terres-
trial atmosphere late last year. Boosted to an altitude of 3604
miles, Orion fell back to Earth on December 5 at nearly 20,000
mph. During re-entry, Orion’s heat shield protected the vehicle
from external temperatures of 4000°F—nearly half the heat of
the sun’s surface.
The heat shield is the forebody or wind-facing side of an
aeroshell system. Due to its size, the aeroshell experiences
tremendous entry loads as a result of dynamic pressures from
the atmosphere and the high velocity of vehicle descent. Lock-
heed Martin constructed all eight of the aeroshells that have
protected NASA’s Mars-bound space-
craft—but Orion is unique.
At 16.5 ft in diameter, it is the
largest composite heat shield ever
made. Orion is also designed for
long-duration, human exploration
of deep space. That means the
shield will play a critical role in pro-
tecting future astronauts on their
return to Earth.
Not only is the new heat shield
the largest ever built, it also fea-
tures a unique resin system that can
withstand higher temperatures and
landing impact. After testing in ex-
treme environments and simulating
re-entry, engineers verified that the
thermal insulator on the outside of the composite material
could be thinner, making the spacecraft lighter and allowing
more payload to join the mission. The resin was developed
by the Lockheed Martin Orion thermal protection system
team in partnership with TenCate Advanced Composites,
Morgan Hill, Calif.
The heat shield is built around a titanium skeleton and
carbon-fiber skin that gives the shield its shape and provides
structural support for the crew module during descent and
splashdown. A fiberglass-phenolic honeycomb structure fits
over the skin, and each of its 320,000 cells is filled with a ma-
terial called Avcoat. The surface is designed to burn away, or
ablate, as thematerial heats up, rather than transfer heat back
into the crew module. At its thickest, the heat shield is 1.6-in.
thick, and about 20% of the Avcoat will erode as Orion travels
through Earth’s atmosphere.
Test parameters
During the high orbital test flight, Orion traveled a total
of 60,000 statute miles and as far out as 3600 statute miles
Fig. 1
— At 16.5 ft in diameter, the Orion heat shield is the largest
composite version ever made.
Orion heat shield details:
• The Orion heat shield is the largest ever made.
• The melting point for titanium is about 3000°F and the surface temperature of the sun is about 10,000°F.
Orion can handle temperatures around 5000°F.
• Orion must withstand landing loads of 300,000 to 400,000 lb, roughly equivalent to the mass of a school
bus crashing into the ocean at 20 mph.
A D V A N C E D
M A T E R I A L S
&
P R O C E S S E S | F E B R U A R Y 2 0 1 5 |
i T S S e
1 1
iTSSe
|
TSS
Fig. 2
— Engineers attach the heat shield to the Orion spacecraft.