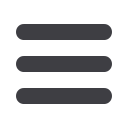
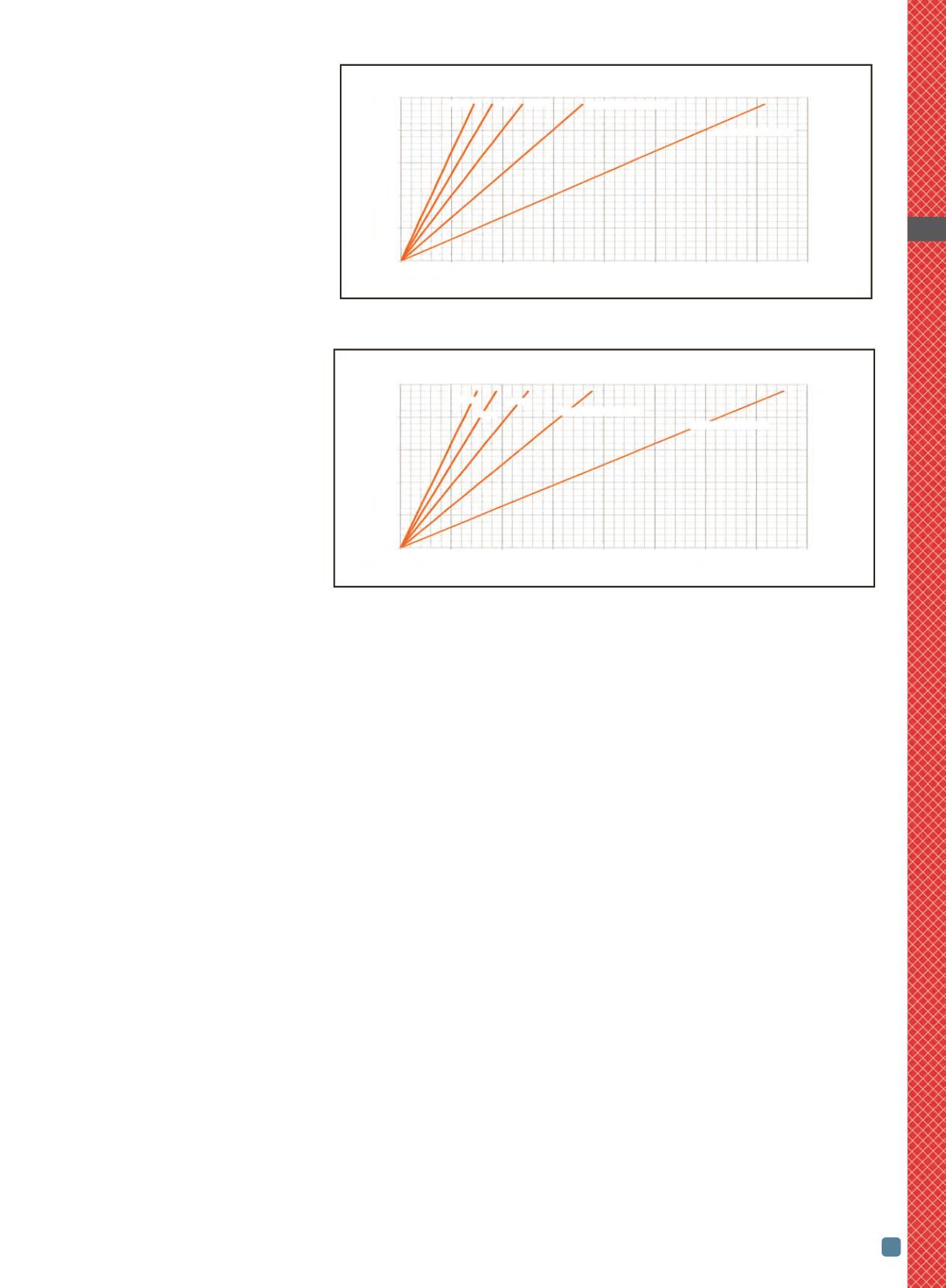
ADVANCED MATERIALS & PROCESSES •
JUNE 2014
43
HTPRO
7
temperature rise of 5°C (10°F) with a
maximum temperature of 45°C (110°F).
For polymer quenchants, it is somewhat
more difficult. The maximum tempera-
ture for polyalkylene glycol (PAG) quen-
chants cannot exceed the cloud point
temperature. This is between 60° and
75°C (135° and 170°F) for most PAG
quenchants, depending on the molecular
weight of the polymer. It is also recom-
mended that the maximum bulk temper-
ature rise be at most 10°C (20°F) below
the cloud point temperature. Polymer
quenchants, besides being sensitive to ag-
itation, are strongly affected by tempera-
ture. The cooling rate decreases
significantly with increasing temperature.
Small temperature rises during quench-
ing reduce variations in cooling rate and
quench rate effectiveness. This also re-
duces drag-out, produces more uniform
quenching, and prolongs the life of the
quenchant. Limiting the temperature rise
greatly increases the quench tank size.
For PVP-type quenchants, there is no
cloud point temperature. However, the
maximum peak temperature is generally
limited to 65°C (150°F) or lower to pre-
vent destructive oxidation of the quen-
chant. This also reduces the amount of
drag-out and chemical consumption in
the system.
As an example, consider the design of a
quench tank containing Aqua-Quench
3699, a hybrid polymer quenchant that
does not have a cloud point. Steel parts
will be quenched from 1095° to 205°C
(2000° to 400°F), with a maximum load
weight of 2270 kg (5000 lb). The quench
tank operates at 45°C (110°F) nominally.
What volume of quenchant is required
in gallons?
To solve this, the maximum allowable
temperature rise must first be deter-
mined. For this quenchant, the maximum
temperature is 65°C (150°F). Because the
quench tank is operating at 150°F, the
temperature rise of the quenchant (Δ
T
q
)
is 40°F (i.e., 150°–110°F). From the equa-
tion above, and rearranging to determine
the mass of water required:
M
m
Cp
m
D
T
m
=
M
q
Cp
q
D
T
q
or
M
q
=
M
m
Cp
m
D
T
m
/
Cp
q
D
T
q
therefore
M
q
= 5000 lb (0.17 Btu/lb/F)
(1600)/0.95 Btu/lb/F (40F)
M
q
= 35,800 lb (16,270 kg)
polymer quenchant
A gallon of water weighs 8.33 lb/gal
(1 kg/liter), so the number of gallons re-
quired to quench 5000 lb of steel is 4296
gal (16,260 liters). Temperature rise for
polymer and oil quenchants are shown
in Figs. 1 and 2.
System temperature control
Maintaining the temperature of the
quench bath is as important as the size
of the quench tank, which requires a
means of temperature control.
Quenchant heating
is achieved using sev-
eral methods, including electrical resist-
ance heating elements, gas- and oil-fired
radiant tubes, and waste heat from the
furnace exhausts. In some systems, the
quenchant is heated by quenching a
“dummy” hot load of parts. The energy
density of radiant tubes and electrical
heating elements should not exceed 1.5
W/cm
2
(10W/in.
2
). This prevents heaters
from preferentially oxidizing the oil and
depleting the oxidation additive package.
This energy density guideline should also
be followed for polymer quenchants, with
the additional provision that maximum
heater temperature should be about 70°C
(160°F) to prevent exceeding the cloud
point of the material. Heaters should also
be interlocked with the agitation system
so they shut off if the agitation system is
shut off or fails. The system should also
be designed to make it impossible to turn
on the heating system without the agita-
tion operating.
Quenchant cooling
. Various methods are
available to cool quenchants including:
• Submerged water-cooling pipes
• Cooling jackets
• External water-cooled heat
exchangers
• Forced air-cooled radiators
• Refrigeration systems
Fig. 1 —
Relationship of volume of oil quenchant and weight of quenched workload to
prevent specific temperature rise of quench bath when quenched from 1600° to 140°F
(870° to 60°C).
Fig. 2 —
Relationship of volume of polymer quenchant and weight of quenched workload to
prevent specific temperature rise of quench bath when quenched from 1600° to 140°F
(870° to 60°C).
2500
2000
1500
1000
500
0
2500
2000
1500
1000
500
0
Weight of batch load
quenched, lb
Weight of batch load
quenched, lb
0 1000 2000 3000 4000 5000 6000 7000 8000
Oil required in tank to limit bath temperature rise, gal
0 1000 2000 3000 4000 5000 6000 7000 8000
Polymer required in tank to limit bath temperature rise, gal
1135
910
680
455
230
0
1135
910
680
455
230
0
Oil required in tank to limit bath temperature rise, liters
0 3785 7570 11,355 15,140 18,925 22,710 26,495 30,280
Polymer required in tank to limit bath temperature rise, liters
0 3785 7570 11,355 15,140 18,925 22,710 26,495 30,280
Weight of batch load
quenched, kg
Weight of batch load
quenched, kg
100°F 80°F 60°F 40°F Temperature rise
(55°C) (45°C) (35°C) (20°C)
20°F (10°C)
50°F (25°C) 30°F (15°C)
40°F (20°C) 20°F (10°C) Temperature rise
10°F (5°C)