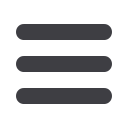
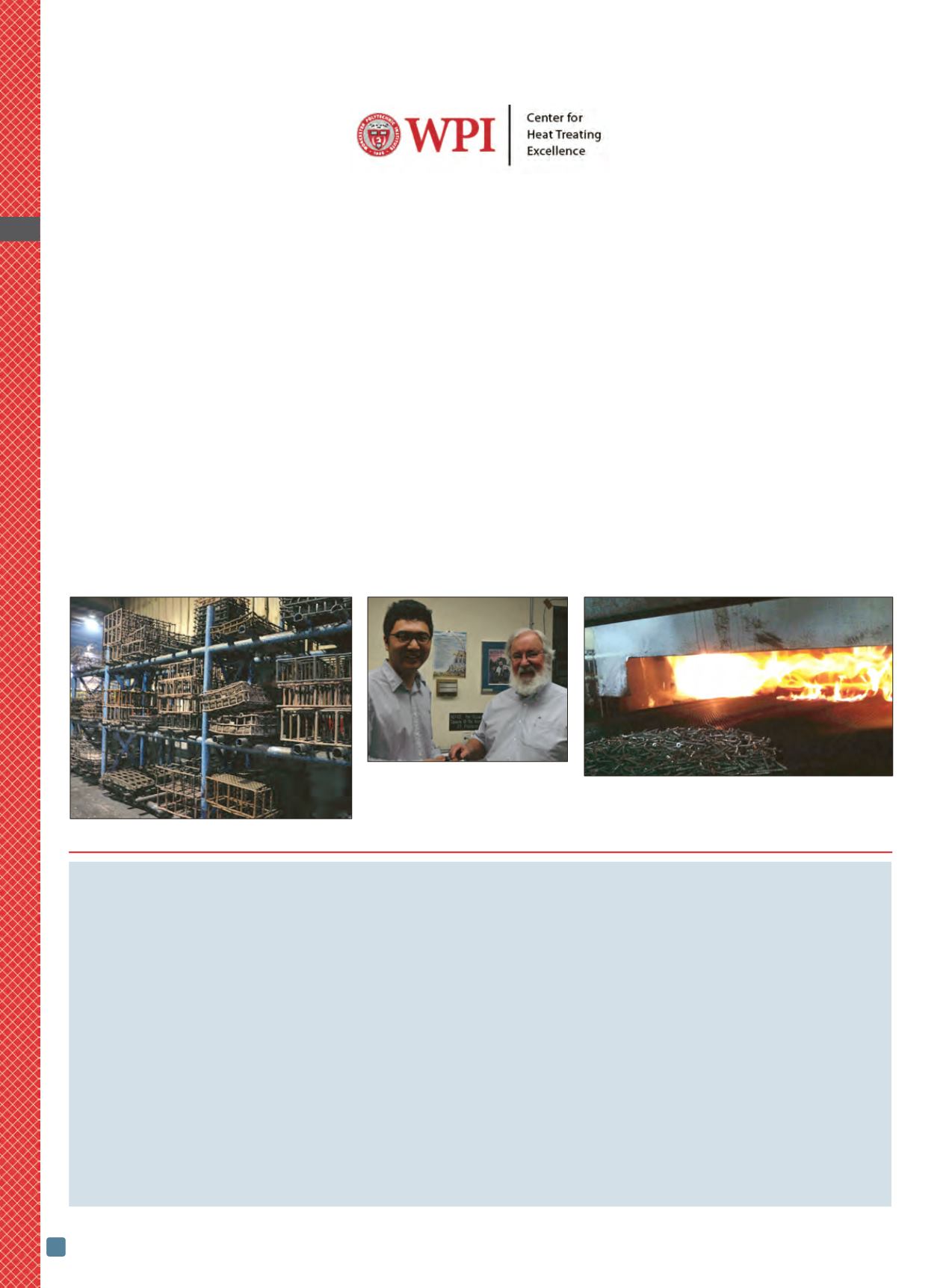
Heat treating companies spend a signifi-
cant amount of time and money replacing
furnace parts and furnace fixtures. Extend-
ing the service life of these components
and reducing the time to heat them up and cool them down
could result in considerable savings. The Alloy Life Extension Proj-
ect currently under way at the Center for Heat Treating Excellence
(CHTE), Worcester Polytechnic Institute (WPI), is aimed at solving
those problems.
The focus of the project is identifying and testing alloys and coat-
ings that can improve the service life of parts like fans, burners,
rollers, tubes and mesh belts, as well as fixtures like wire baskets
that carry the parts to be heat treated.
Researchers are also analyzing fixture design and material selection
to reduce the energy needed to repeatedly heat fixtures. The goal
is to find alloys for use in the heat treating industry that will last
twice as long as current materials, resulting in significant savings.
According to Rick Sisson, George F. Fuller professor of mechanical
engineering at WPI and director of CHTE, “Manufacturers are spend-
ing lots of money for alloy fixtures that go into carburizing furnaces.
The goal of this study is to explore options that will allow industry
to work more efficiently, lessening fixture replacement costs, reduc-
ing energy consumption, and improving product quality.”
The project has already produced some in-
teresting findings. For example, the main
reason for alloy failure is excessive carbur-
ization, which causes furnace parts and fixtures to become brittle
and easily fracture. Based on this information, a series of carburiza-
tion-resistant alloys have been identified for commercial furnace
testing, including RA602CA, Inconel 625, and Stellite 250. Samples of
these alloys are being tested at the facilities of CHTE member com-
panies Sikorsky Aircraft and Bluewater Thermal Solutions.
Different alloys are being assessed for their resistance to oxidation
and carburization at two Bluewater facilities in Illinois. Multiple
sets of each alloy are run for different times in test furnaces, and
one of each set is removed periodically to evaluate the extent of
alloy degradation. Based on visual inspection, samples are re-
moved for metallographic characterization.
Another test being carried out at Bluewater is aimed at determin-
ing whether an aluminized section of an industrial furnace mesh
belt holds up better than regular mesh belts. Craig Zimmerman,
technical director at Bluewater, explains, “Mesh belts last only nine
months and they are extremely expensive to replace. We are hope-
ful that this study will help us and everyone in the industry to
identify which materials can drive down costs. If we can make any
of the parts and fixtures last longer, it will be a huge savings.”
ADVANCED MATERIALS & PROCESSES •
JUNE 2014
40
Improving the Service Life of Furnace Materials
HTPRO
4
About CHTE
The CHTE collaborative is an alliance between the industrial sector and university researchers to address short-term and long-term
needs of the heat-treating industry. Membership in CHTE is unique because members have a voice in selecting quality research proj-
ects that help them solve today’s business challenges.
Member research process
Research projects are member driven. Each research project has a focus group comprising members who provide an industrial per-
spective. Members submit and vote on proposed ideas, and three to four projects are funded yearly. Companies also have the op-
tion of funding a sole-sponsored project. In addition, members own royalty-free intellectual property rights to precompetitive
research, and are trained on all research technology and software updates.
CHTE also periodically undertakes large-scale projects funded by the federal government or foundations. These endeavors keep mem-
bers informed about leading edge technology.
CHTE current research portfolio
Other projects now in progress include:
Nondestructive Testing for Hardness and Case Depth, Induction Tempering, Gas Quench Steel Hardenability, Enhancements to CHTE
software (CarbTool, CarboNitrideTool, and NitrideTool), and Cold Spray Nanomaterials (supported by ARL).
For more information about CHTE, its research projects, and member services, visit
wpi.edu/+chte, call 508.831.5592, or email Rick
Sisson at
sisson@wpi.edu, or Diran Apelian at
dapelian@wpi.edu.
Furnace fixtures at various levels of degradation.
Part of the research is looking at ways to extend the
life of mesh belts so that companies don’t have to
replace them every nine months at significant
expense.
Rick Sisson (right) and Anbo Wang
work together to identify ways to
extend the life of alloy parts and
fixtures. Mei Yang also contributed
to the study.