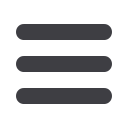
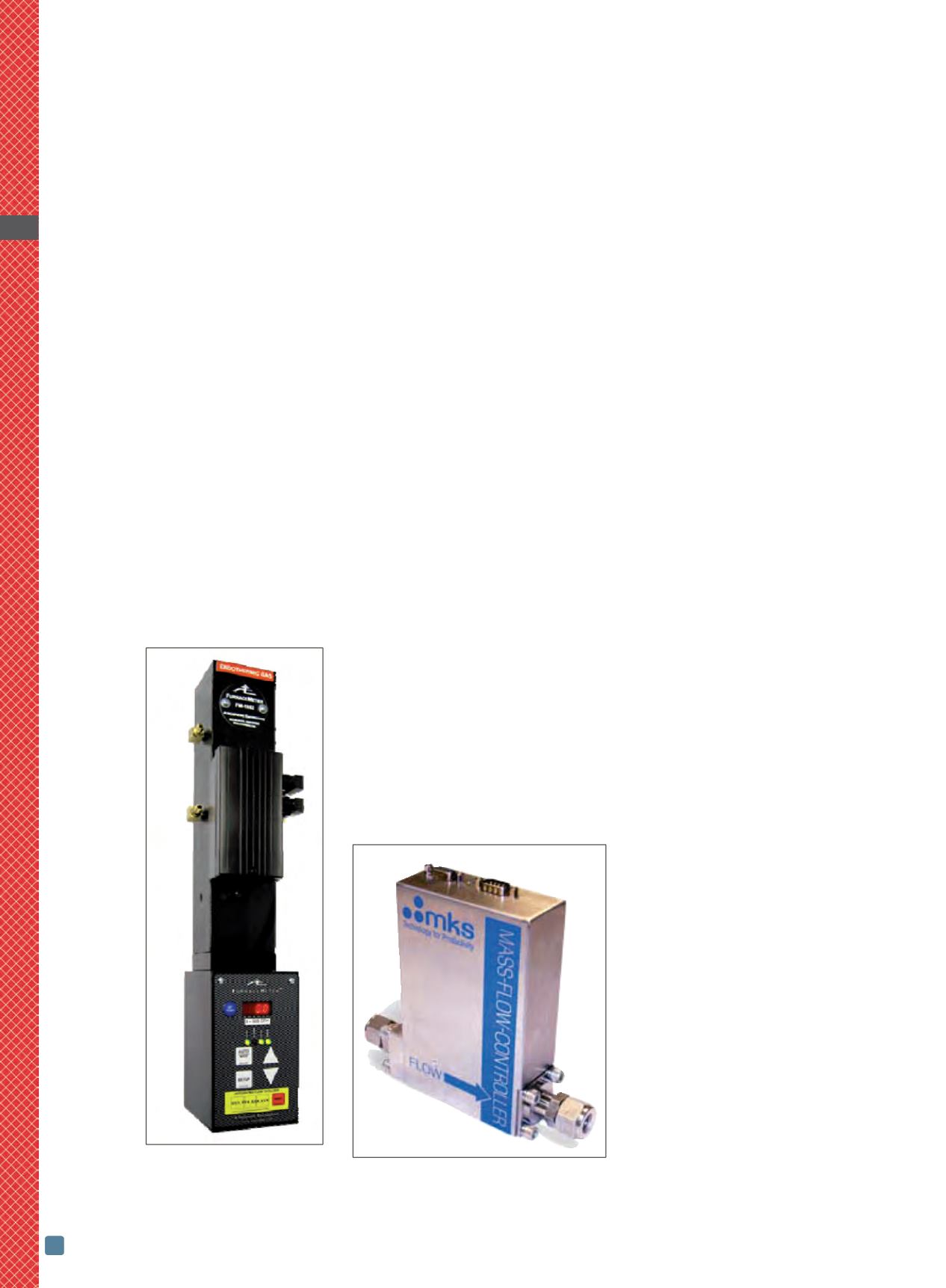
OPERATIONAL PRINCIPLES
OF FLOWMETERS
ONCE A “SET IT AND FORGET IT” TECHNOLOGY, FLOW MEASUREMENT IS AN INCREASINGLY IMPORTANT
PART OF QUALITY CONTROL SYSTEMS IN THE HEAT TREATING INDUSTRY.
Daniel H. Herring*,
The Herring Group Inc., Elmhurst, Ill.
In most heat treating applications, im-
portant flowmeter selection criteria in-
clude reliability, accuracy, ruggedness,
ease of calibration, and ease of mainte-
nance. Given the high accuracy and re-
liability of today’s instruments, users
can run their processes more econom-
ically. This article discusses the most
commonly used flow measurement in-
struments and compares their operat-
ing principles (Table 1).
Types of flowmeters
Flowmeters typically measure either vol-
umetric or mass flow.
Volumetric flow
measurement
looks at the flow of a given
volume of the medium over time (e.g.,
ft
3
/h). This technology uses either me-
chanical flow rate indication or elec-
tronic output (Fig. 1).
Mass flow measurement
looks at the
flow of a given mass over time (e.g.,
lb/h). Industrial thermal mass flowme-
ters are often equipped with electronic
output (Fig. 2). Conversions between
the two measurements can be made if
the pressure, temperature, and specific
gravity of the flowing medium are
known.
Flowmeters can be further subdivided
into several general types. Of these,
variable-area
and
thermal-mass
flowmeters are most often used in heat
treating applications:
•
Variable area
: Fluid flow rate is
measured as the flowing medium
passes through a tapered tube. The
position of a float, piston, or vane
placed in the flow path changes as
higher flows open a larger area to
pass the fluid, providing a direct
visual indication of flow rate.
• Differential pressure
: Calculating a
fluid flow rate from the pressure
loss across a pipe restriction is the
most commonly used flow
measurement technique in
industrial applications. The
pressure drops through these
devices are well understood, and a
wide variety of configurations are
available, each having specific
strengths and weaknesses.
Variations on the theme of
differential pressure flow
measurement include the use of
pitot tubes.
• Mechanical
: In these instruments,
flow is measured either by passing
isolated, known volumes of a fluid
(gas or liquid) through a series of
gears or chambers (positive-
displacement type) or via a
spinning turbine or rotor.
Measurements using a positive-
displacement flowmeter are
obtained by counting the number
of passed isolated volumes.
• Electronic
: Magnetic, vortex, and
ultrasonic devices are available, all
of which have either no moving
parts or vibrating elements and are
relatively nonintrusive.
• Thermal mass
: In contrast to
volumetric flow devices, thermal
mass flowmeters are essentially
immune to changes in gas
temperature and pressure. Because
measurements can be very
accurate and repeatable, these
devices are used in critical flow
measurement applications.
Variable-area types
Variable-area flowmeters are simple,
versatile devices that operate at a rela-
tively constant pressure drop and meas-
ure the flow of liquids, gases, and steam.
The popularity of this type of flowmeter
in the heat treating shop is their direct-
view design, where flow is indicated me-
chanically, which makes it easy to
understand the operating principle. Sev-
eral different designs of variable-area
flowmeters are used throughout the
heat-treating industry (Fig. 3).
*Member of ASM International
ADVANCED MATERIALS & PROCESSES •
JUNE 2014
46
HTPRO
10
Fig. 2 —
Typical mass flowmeter. Courtesy
of MKS Instruments.
Fig. 1 —
Typical volumetric
flowmeter. Courtesy of
Atmosphere Engineering Inc.